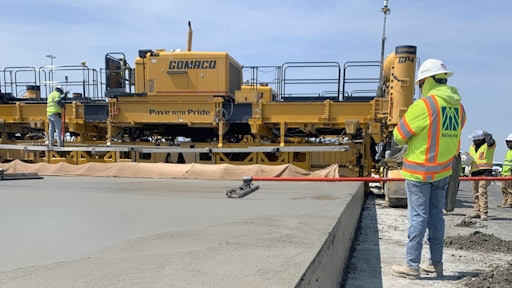
The Indianapolis Airport Authority received an Envision award by the Institute for Sustainable Infrastructure for the innovative and environmentally sustainable approach to a reconstruction project for the Indianapolis International Airport (IND). When it came time for the concrete pavement replacement of runway 5R-23L and taxiway D, they turned to local concrete paving company Milestone Contractors to earn a second.
The work done earned an Envision: Platnium award in 2023.
Based in Indiana and one of the larger contractors in the state, Milestone is a multifaceted company, providing services for concrete and asphalt construction. Not one to shy away from a too large or too small of a job, they work on everything from bridges, curbs, sidewalks, driveways, work for the Department of Defense, as well as airports. As Steve Friess puts it, “We pretty much cover the whole gamut.” Milestone Contractors
Friess is the vice president of concrete operations at Milestone. He’s been with the company for 11 years and has an extensive background in concrete paving. For those in the Indiana concrete pavement world, if the name sounds familiar – it should. He was named Chairman of the Board of the American Concrete Pavement Association (ACPA) in December 2022. In his nearly 40 years of experience in the pavement industry, Friess has enhanced Milestone’s concrete offerings by developing Heritage Construction + Materials and seeing the company earn accreditation in ASHTO R-18 and ASTM C1077. Ernie Peterson from Ash Grove Cement Company is the current ACPA chairman.
While Milestone does put down a greater amount of asphalt, its concrete work is still nothing to scoff at. Friess expects Milestone to place 3 million tons of asphalt and about 700,000 yards of concrete this year. The company has a ready-mix division and owns seven portable plants they move around for airport and freeway jobs.
Milestone is owed by The Heritage Group, a fourth-generation family-owned business out of Indianapolis led by Amy Schumacher, chief executive officer. “Even as big as we are,” says Friess, “they are still very family-oriented. Milestone has a motto that says ‘We make lives better one road and bridge at a time.'”
The Heritage Group celebrated 90 years in business in November 2020. In the 1930s, John Fehesenfeld opened a residential home heating oil delivery service which evolved into a brand of convenience stores and eventually sold to Speedway. In the 1950s, the company moves into the paving industry with Fehesenfeld's sons at the helm. Milestone originally began as Columbus Paving Company in 1954 by the Meshberger family and Herman Newen, after several mergers and purchases, it eventually became Contractors United Incorporated (CUI) in the 1970s and made of a unification of a handful of local companies—making it the largest construction firm in the area in 1971. CUI, Fauber Construction Company, and Astro Paving joined to become Milestone Contractors LC in 1994. They added Speedway Co. in 2022 to supply ready-mix concrete.
Indianapolis Concrete Pavement
Reportedly, the Indianapolis Airport Authority was aiming for another Envision award – something extremely difficult to earn. Friess and his team were up for the challenge. He saw what needed to be done and went to work. Milestone was hired for the second and third phases of the project. Phase three is scheduled for this year April to October.
Phase one was the center point of the runway and taxiway 23, the middle 5,000-6,000 ft of an 11,000-ft. long runway (plus a little). This also included the adjoining taxiway in front of the FedEx location – a major hub for the airport (the second largest in the country for FedEx).
Milestone Contractors
Phase Two
Milestone was hired for phases two and three. At about $88 million, according to the request for bids document, major work items for phase two included:
- 79,000 square yards of concrete pavement removal
- 104,000 square yards of P-501concrete pavement at 37.5 ft. wide, 22 in. thick
- 104,000 square yards of asphalt pavement removal
- 54,000 cubic yards of unclassified excavation
- 75,000 cubic yards onsite borrow
- along with work in storm sewer, watermain, airfield electrical, signage, lighting, NAVAIDs, and pavement marking
Aside from the men and women of the Milestone crew, carrying the load of the major paving work was GOMACO equipment. The paving line included two spreaders (a second with a conveyor to increase production), a GP4 slipform paver, and dump trucks to transport the concrete mix from an Erie Strayer concrete plant. They used a portland limestone cement from Buzzi Unicem USA and injected captured carbon into the mix. Milestone purchased the GP4 about four years ago, paving up to 30-32 ft. for different interstates. When they were finally awarded the job, they also purchased a PS460 placer/spreader – capable of paving to 40 ft. wide.
Milestone Contractors
Having paved for the Atlanta Hartsfield and Cleveland Hopkins airports previously, he’s had experience paving to 37.5 ft. before. Friess’ advice: “it all comes down to good mix and good setup on your equipment.” Needing to pave 22 in. of concrete, the challenge in Indianapolis was the depth. While they had worked on 18 in. before for "fill-in" work. Indianapolis required them to pour without forms, reinforcing the need for a good mix. The concrete was specified to be 625 psi in accordance to FAA flexural strength tests with a 0.25 to 0.5 slump. Their test lab was able to keep on target to avoid any panel removals due to strength. The pavement was finished with transverse grooves.
“With this new paver and the QC team that I have, they were spectacular from day one,” he says. “In fact, the first day I kind of looked at it and said, ‘If this goes this good the rest of the time, we’re going to be golden.’ It even went better. We had a great team out there. I can’t say enough about the team we had, they were spectacular,” says Friess.
With the amount of concrete and the tight schedule to keep, they needed their Erie Strayer plant to be able to produce. “We had to have a plant that would do 500 yards an hour. It would do 600 yards an hour if there was the area for it – that’s almost a load a minute for 10-yard loads,” explains Friess. “It will produce more concrete than you know what to do with sometimes.”
Ultimately, they recycled the existing runway and asphalt shoulders for base material.
Recycled Materials
- 135,000 cubic yards of the existing runway into base material
- 65,000 tons of asphalt from shoulders for under the pavement and shoulders
- Reused more than 4 million gallons of water
Friess explains that most of the construction was kept to a centralized location onsite to minimize the carbon footprint of the project. Crushed concrete pavement was pulverized into multiple sizes for the reuse of base materials, pipe backfill, and a special fill for lighting. “In the words of sustainability, this is what it was all about…because these quantities are just unbelievable,” he notes.
Milestone Contractors
As the breaker shattered the pavement, off-road trucks hauled material a short distance—less than 1,500 ft.—into a pile. While Milestone were able to recycle themselves, they subcontracted it out to a crushing company from Chicago. “This was such a mammoth project, we figured we’d let them do it," says Friess. "Since then, they have crushed almost everything that they had onsite at the airport above and beyond our current job. We had them crush at least another 150,000 tons of this material that they’ve used on other projects at the airport.”
The concrete runway included 2 in. dowels in both directions on every joint cut into 6 ft. sections to help with the weight. “If you pick six 18.5 lbs. dowels, plus the weight of the basket unit itself, you’re like 120 lbs. for a six footer. We were pouring 30-37.5 ft. across, so there’s no way to pick up 36 ft. of dowels.” A Minnich drill made quick work of drilling the 2 1/8 in. holes.
No one said concrete work was easy. “Just the fact of putting in 500 bars a day at just under 20 lbs. a piece, you know, that’s a lot of weight,” says Friess. “The whole crew worked very hard.”
Sustainability efforts also included injecting CO2 with technology from CarbonCure into the concrete mix to encapsulate the captured carbon. Unfortunately, the carbon injection plans didn’t go exactly as intended. While injection was successful, Milestone wasn't able to get captured carbon close enough to the plant to make it a viable option and had to purchase carbon from within a 60-mile radius.
With carbon injection, Friess says that they might have been able to conduct tests to potentially reduce cement content after some time. However, the pouring ended before they were able to do so.
Signage and constant reminders urged everyone to keep trucks off to keep emissions down.
Waste and water sources were another issue. Milestone set up three settling ponds to capture water and used an ozonator to oxygenate and help clean the water. They used this as well as any collected rain water to spray the grade for dust control and compaction efforts. They kept track of every tanker load, how many times they filled the truck up, and where it was filled (pond or hydrant). “After a big rain, there were four ponds around the airport that would fill up and we’d go suck it up out of there—there was a lot of effort made to recycling everything.”
Circle City
Phase Three
Phase three is on the far west end of the airport which includes the construction of a 5-acre $15 million solar panel field. “With the solar, we'll actually be able to do one of the complete runways at the airport. Going back to sustainability and all that, the Indy airport is really probably ahead of the times in that kind of work,” comments Friess.
According to an announcement from IND in July 2023, phase three is being funded by the nation's largest allotment of funding via the Airport Improvement Program of the FAA: $22.58 million. The funding is part of $92 million to help airports reach the net-zero emissions by 2050.
This project exemplified the value of organization and communication. “We learned sustainability isn’t a bad word…with good organization and good communication, you can run one of these jobs and you don’t have to work day and night, seven days a week.
When we got down to the end, when we were paving, we were working 10-hour days, and still getting our 200-300 yards a day. We found out we don't have to work 24 hours a day, 365, seven days a week. You just don't have to. You just have to be organized and have a plan.” Beyond that, he strongly suggests any concrete paving contractors to join the national ACPA and attend the airport workshops.