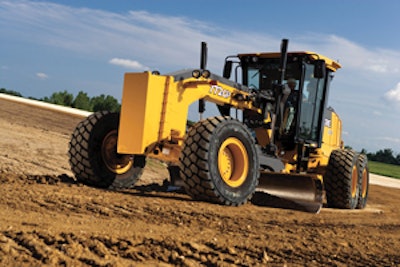
A well-adjusted and maintained motor grader has always been able to achieve precise grades with an experienced operator in the seat. But the growing popularity of grade control systems is re-defining the term "precise." This places an even greater emphasis on maintenance of the moldboard system.
"With more and more contractors going to automatic blade control (GPS, sonic, laser guided) for grade control, some of these systems are operating at precision levels approaching +/- 1/8 in.," notes Gary J. Atkinson, Southeast region product manager - road products, Volvo Construction Equipment North America. "Of course, the tighter the tolerance is between the blade support arms attached to the mainframe of the grader, the turn circle and the moldboard itself, the tighter the tolerance the total system can maintain."
Having too much play in the moldboard system is a common occurrence. Atkinson often delivers new motor graders for jobsite demonstrations. These machines are set up to factory spec.
"Essentially, these machines come from the factory with virtually zero total vertical clearance," he notes. "Operators have a hard time adapting to it because the machine they got off of is essentially worn out. They have an inch or more of vertical movement in the entire system. The moldboard on the grader is essentially operating in float control.
"When we bring out a brand new grader that is absolutely tight, where you set the moldboard is where it is going to be," he continues. "That is what you want with automatic blade control."
Keep it tight
Wade Porter, motor grader product and application specialist, Caterpillar Inc., asserts that no movement in the moldboard system is acceptable. There are several ways to check for excessive play. "Lift the drawbar, circle, moldboard off the ground," he advises. "If the lift cylinder rods move without immediate cutting edge movement, then this linkage is considered loose and needs to be adjusted properly.
"The moldboard will begin to 'chatter' when the slide rail inserts need to be adjusted," he adds. "Chattering is when the moldboard wiggles back and forth, fore and aft. This will create a washboard effect on the finished surface. This can also be inspected by removing the end cap for the slide rail inserts, lifting the moldboard in the air, and checking gaps between the insert and the rail. The drawbar wear inserts can be checked by raising the moldboard off the ground and inspecting for a gap between the wear insert and the drawbar plate."
The frequency of inspections depends on the accuracies required. "The need to check for excessive play in the lift cylinder ball and sockets, the circle turntable and the moldboard slides is dependent on the type of work being done," says Nathan Horstman motor grader product specialist, Deere Construction & Forestry Division. "Fine grading work requires a 'tighter' machine than rough grading work. Many operators will check the play in these joints before starting a fine grading job."
It's also important to keep the moldboard clean and in good working condition. "Material buildup on a moldboard will adversely affect the material flow characteristics," Porter points out.
"The moldboard face should be kept clean," agrees Horstman. "Mud or debris stuck to the face of the moldboard will prevent material from rolling properly and flowing down."
According to Porter, "Many customers chrome their moldboards to provide a smooth surface that prevents material buildup [especially in sticky material]. If material is not allowed to move freely along the moldboard surface area, it can negatively affect fuel consumption and productivity."
"Some corrosive materials and wet conditions can eventually damage the moldboard, and very abrasive materials can wear a moldboard thin," adds Dan Gillen, motor grader product support supervisor, Caterpillar. "Some customers chrome the moldboard, providing a harder, less porous surface to counteract the corrosion and wear."
When the grader is not in use, take steps to prevent rust from forming on the moldboard surface. "A rust preventative can be used to prevent corrosion during prolonged storage," Horstman notes. "However, common paint should not be used, as it can take too long to scour the moldboard when the motor grader is put back into service."
Keep it sharp
No matter what the application, a sharp cutting edge is essential.
"Cutting edge sharpness is the single most important factor for material penetration and material action on the moldboard," says Gillen. "Most complaints of poor material action... are due to a dull cutting edge and incorrect moldboard position. A sharp cutting edge will reduce the amount of rimpull required to push the blade through the cut, thus reducing overall operating costs."
The operator plays the most critical role in keeping the cutting edge sharp. "An experienced operator realizes that operating continuously with the blade rolled all the way forward will eventually dull the tip," says Horstman. "An experienced operator also knows that cutting with the moldboard rotated rearward will work to sharpen the edge.
"The sharper the cutting edge bevel, the better it will penetrate the soil in a cut," he continues. "Double-bevel cutting edges are the most versatile and common of motor grader cutting edges. [They feature] a bevel on the cut surface for good cutting penetration and a curvature to create good rolling action of the material."
Thick or thin?
There is a trade off between cutting edge thickness and penetration, wear life and strength of the edge. "A thicker edge will wear longer and be less susceptible to breakage," Horstman states, "but will have less penetration than a thinner edge. Generally, 5/8- or 3/4-in.-thick double-bevel cutting edges work well for most dirt applications."
Cutting edge thickness also impacts grading cost per hour. "As the cutting edge thickness increases, the maximum amount of moldboard down pressure per sq. in. is reduced. The maximum down pressure remains constant, but that force is spread over a larger surface area," says Gillen. "Therefore, a thicker edge requires the operator to use more down pressure to penetrate and cut material."
Excessive down pressure can have negative consequences. "[It] increases rimpull requirements, burning more fuel; increases frequency of tire slip, accelerating tire wear; increases forces on the frame, reducing component life; sends higher torque loads through the driveline; and builds excessive heat on the cutting edge, which can exceed heat treat tolerances," Gillen points out.
But you shouldn't go too far the other way either. "Using a cutting edge that is too small or too thin can make the edge more susceptible to damage and early wear, which will increase owning and operating cost and potentially damage other components, such as moldboard cutting edge hardware," says Porter.
Of course, there are applications where a thick cutting edge is preferred. "For long life in road maintenance, use the thickest edges that allow you to do the job," advises Porter. "If you use excessive down pressure in hard material, the machine's front end appears light. If penetration is a problem, use thinner cutting edges, a serrated edge or a scarifier to loosen the material."
Cutting edge composition
The type and composition of the cutting edge has a substantial impact on its longevity.
"Over the years, I have received many calls regarding cutting edge life. Depending upon the application and roadway material, a cutting edge can wear out in a day or last for several months of use," says Atkinson. "In a lot of cases, people haven't experimented and don't know what is out there in terms of alternatives."
It's important to match the cutting edge material to the application. "Caterpillar uses DH2 steel for our standard cutting edges," says Porter. "There are carbide and tungsten edges available that provide long life in light-duty applications, but are brittle and break easily if used in high-impact or abrasive conditions."
In some instances, carbide cutting edges can last dramatically longer than a standard edge. "If you could change the cutting edge material that you are using and go for 100 hours or longer vs. four or five hours, just think of the thousands of dollars you would save," Atkinson comments. "The purchase price of carbide cutting edges is substantially higher. But if it costs you $200 to change a standard set of edges and you are doing it every other day, the payback for a $2,500 carbide blade would be just a couple of weeks."
Bear in mind that not all edges are built to the same standards. "John Deere has its own stringent quality requirements for steel composition and heat treatment," notes Horstman. "Dura-Max edges are manufactured from special steel hardened for excellent wear resistance and strength and tempered for improved impact resistance. The result is that [they] are designed for optimum performance and wear life in a variety of working conditions."
Impact of edge wear
Different applications will create different wear patterns. "Severe operations where grading wear is concentrated on the 'toe' or leading edge of the moldboard can cause premature wear at the outboard corners of the cutting edges," says Horstman. "Overlay end bits are recommended in severe conditions, like haul road maintenance, to protect the vulnerable outside corners of the cutting edge.
"On the other hand, 'crowning' is a wear pattern that develops from constant gravel road maintenance, where the cutting edge in the center of the moldboard wears more quickly than the outside corners," he continues. "Extremely abrasive materials can also cause premature wear. A cutting edge that is worn unevenly will make it difficult to cut an accurate grade along the length of the moldboard."
An experienced operator can reduce the frequency of cutting edge replacement. "If an operator is able to evenly wear the cutting edge across the entire length of the edge or keep the edge properly maintained, then accuracy will not be sacrificed and productivity will remain constant," says Porter.
It is advised not to let the cutting edge wear too close to the moldboard. "The cutting edges should be replaced when they are worn to within 2 in. of the moldboard, or when they are worn unevenly across the length of the moldboard," says Horstman. "An evenly worn and sharp cutting edge can provide adequate accuracy and productivity throughout its life. If the cutting edge is worn down too far, the moldboard can be damaged."
Finish grade operators can't get as much life out of a cutting edge due to the accuracy required. "For fine grade work, you need to have a 100% straight and true cutting edge," says Atkinson. "You can pull a string across it, lay it on a flat surface or just look at it. You can tell very easily if it is worn to excess.
"In a fine grade application where precision is critical, you are never going to wear the cutting edge down to the moldboard itself," he adds. "Your operators are going to get maybe an inch of wear on that cutting edge, then will want it replaced. Once again, in critical applications the level of precision will suffer if the cutting edge is less than perfect."
The application and desired end product will really determine how frequently a cutting edge needs to be replaced. But with the accuracy possible via today's automated grade control systems, you really need to keep a close eye on all the acceptable tolerances for best results.