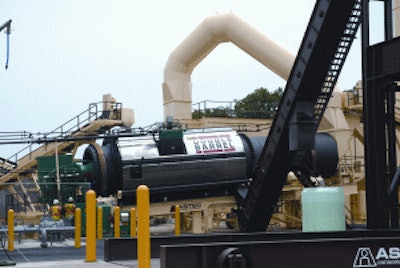
Making a decision to purchase a new piece of equipment in a challenging economy is not easy. Making a decision to purchase a new asphalt plant costing several million in a challenging economy is definitely not easy. But for Independence Construction Materials (ICM) it was clearly the right decision and the right time; and earlier this summer, ICM, a division of Pennsylvania-based American Infrastructure held an open house to celebrate its new Jessup, MD facility.
"The decision to open a completely new facility is based on the good market studies the company conducts to determine what will benefit our customers and generate a fair return on the investment," says Rob Schwear, area operations manager for ICM. "This is ICM's eighth asphalt facility and second 500-tph facility. It was really great being able to develop a ?green field' facility starting totally from scratch. It even allowed us to demonstrate our warm mix asphalt capabilities by paving the entire site."
ICM chose a strategic location in the corridor between Baltimore and Washington, D.C. for its newest facility. The asphalt producer/contractor was already bidding on jobs in that area, supplying asphalt out of its Aberdeen facility. The new plant now enhances the company's ability to better serve customers and projects in the area and do so in a more competitive way.
Established in 1983 as a division of American Infrastructure, Independence Construction Materials has grown to include five quarries and eight asphalt plants serving the Mid-Atlantic region. Most ICM asphalt plants are located adjacent to company-owned quarries, yielding production efficiencies that translates into superior quality control and efficient delivery that meets the demanding expectations of customers.
American Infrastructure, ICM's parent company, is a vertically integrated, heavy civil construction company and material supplier strategically positioned to serve a four-state market in the Mid-Atlantic region. American Infrastructure began in 1939 as a local hauling company serving the Philadelphia area.
The Jessup plant
The new state-of-the-art Astec Double Barrel facility is capable of producing 500 tph. The facility is also equipped with the Double Barrel Green System for making warm mix asphalt. With the Double Barrel Green System, Independence Construction Materials can lower mix temperature. A temperature reduction of just 50°F results in fuel savings of 14% corresponding to a 14% increase in production. And because the volatile organic compounds in the liquid asphalt cement never reach the boiling point, there is no smoke or smell associated with warm mix asphalt.
Independence Construction Materials' decision to pave the Jessup site with warm mix not only helped demonstrate the facility's capability to produce the mix, but also demonstrate the environmentally friendly benefits associated with producing and placing a warm mix design.
The new facility was built on a green site in Howard County. Starting with a clean slate, or open field in an industrial park, ICM had the luxury of choosing the type of plant, layout, location, and plant manufacturer who could make it all happen. ICM chose Astec as its plant manufacturing partner, calling it one of the best, premier plants out there.
Among the features that make Astec the "best" for Independence:
- The production rate at this plant - one of the highest capacity plants in the state of Maryland, allows ICM to produce up to 5,000 ton in a single day.
- Three 300-ton storage silos that store mix for up to 48 hours
- Fractionated RAP system allows for increased utilization of reclaimed asphalt in mixes
- Double Barrel Green System - state-of-the-art warm mix system reduces energy consumption and results in fewer emissions and allows use of higher percentage of RAP.
For Schwear, "Astec is the leader in plant design and plant technologies when it comes to green technologies, energy efficiency and recycle capability, Astec products are one of the better, premier plants out there on the market today. ICM is proud to have built one of the cleanest, greenest and most efficient plants in the state."
As Schwear points out, the new facility should serve both internal and external customers well for many years to come.
"We have our own paving crews working out of this facility, so we'll be able to do a better job of controlling quality and delivery of mix to those crews," Schwear says. "We also have customers who have their own requirements to meet. This facility provides the right balance in serving the needs of our crews as well as our outside customers. We have capacity to handle different mix designs and volume needs."
Other components at the Jessup facility include three 300-ton Astec storage silos, eight cold feed bins, three recycle bins for running fractionated RAP as well as shingles, and three Heatec 35,000 gallon liquid asphalt cement tanks. Production is controlled with the Astec TCII control system.
"We've equipped this facility with an Astec mobile screen system that will allow us to fractionate RAP in order to produce mix designs around a high RAP content," Schwear says. "Our state DOT partners are very open to mixes with high RAP because of the environmental benefits of recycling pavement. As long as those high RAP designs perform as well as virgin mix designs, our customers in general are very accepting in specifying that type of mix for their project."
To avoid encroaching on a wetland on the property, Astec designed and constructed a conveyor of approximately 600 feet. One of the longest that Astec has ever constructed.
Stimulus, warm mix & the future
Earlier this year American Infrastructure was awarded the nation's first stimulus funded job ? Maryland Route 650 in Montgomery County. The company utilized the new Jessup facility from its ICM division to produce the mix for the project.
If Maryland approves a warm mix design, ICM will use warm mix for this high profile project. To date, the Astec Double Barrel Green System is the only warm mix system that has been approved for Maryland state highway projects. American Infrastructure milled Highway 650, and paving started in July.
During the open house earlier this summer, ICM introduced area planners, DOT officials, contractors and suppliers to the benefits of using warm mix.
With added stimulus money for road projects, ICM has been bidding on more work this summer and was able to secure several of those stimulus-funded projects. The new facility will supply those projects.
"We were fortunate to work with good partners in building this new facility," Schwear says. "From the county government to all the vendors involved, we appreciate all the effort required to make this happen. And to think we were able to do all this in an economy where many contractors have delayed equipment investments and even downsized their operations.
"Making this kind of investment to improve the level of service to our customers and allow us to pursue future growth opportunities is really all we need to justify our decision," Schwear notes. "We're always looking for ways to improve the quality of our product and the quality of our service so that customers think of us first when deciding who they want to choose as a business partner. If we take care of our customers, we'll be rewarded and we'll be able to continue investing in our business."