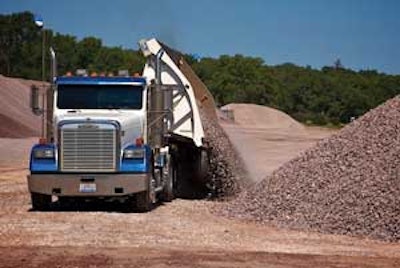
Dump trailers come in a few basic configurations: semi-trailer end dumps, bottom dumps, side dumps, pups and transfers. While regional weight and axle spacing regulations often determine the best choice for the application, you should be aware of which application each is best suited to perform, as well as advantages and disadvantages.
End dumps handle the tough stuff
End dump trailers allow you to carry larger loads than a standard dump truck, plus offer rapid unloading. They are also capable of hauling difficult materials, such as large demolition debris.
End dumps usually incorporate a heavy-sided design that enables them to handle such abusive material, says Brent Beall, Beall Corp. "When you get into that stuff, they are kind of hard to beat," he states.
A key disadvantage is that they can be unstable when raised in the dump position, especially in applications where the dumping location is uneven or off level.
"With end dumps, you need a really conscientious operator because they are prone to rolling over," says Beall. "You rely on a good operator to know when to dump and where. Even when they are empty and they are lifted, you have a really high center of gravity."
Bottom dumps keep it flowing
Bottom dumps feature a clamshell dump gate on the bottom of the trailer. When the clamshell opens, it allows material to be precisely laid in a windrow left and right, or spread evenly across the rear of the trailer when it opens front to rear.
According to Jim Ladner, Landoll Corp., there are three types of applications for which bottom dumps are widely used: stockpiling, material transport and asphalt paving.
Contrary to common belief, a bottom dump can be an effective stockpiling tool. "When you are truly stockpiling, you have a loader or dozer actually building that pile," Ladner points out. In this situation, a bottom dump offers a very quick turnaround time. "The wheels never stop turning. You actually drive right through that dump zone and open the gates to full open. You can dump an entire 21-yd. load in about 25 ft." The material can then be easily handled with the loader or dozer.
With cross-gate models, you can easily spread materials on roads. "We have found that driving at certain speeds, it will actually dump a load as wide as 16 ft. and do a nice job of flowing that material out," says Ladner.
They're also a popular choice for laying a windrow of asphalt in front of a paver laydown machine, since they can help produce a higher quality mat with fewer seams.
"Each time a new dump truck backs up to that asphalt machine, it has to stop, so there is always a seam," Ladner explains. "If the time between trucks is several minutes or longer, then you have quite a seam that builds up." This can result in weak spots in the pavement.
With a bottom dump, there is no need to stop the laydown machine. "It is basically a continuous flow of asphalt," says Ladner.
Dean Word Co. has seen the benefits of this first hand. The highway/heavy road, bridge and paving contractor based in New Braunfels, TX, also operates its own quarry and asphalt plants.
Keeping asphalt flowing between the plants and paving operations is a fleet of 53 belly dump trailers. According to Tim Word, these trailers increase the quality of the mat by laying a constant windrow of material in front of the paver.
"You can keep the laydown machine steadily moving," he notes. "You don't have starts and stops. You get a little improvement in mat quality and a little reduction in segregation. So the overall quality is as good or better than you can achieve any other way."
Of the company's bottom dump trailers, 39 are Landoll models. "We are running maximum interstate loads of 80,000 lbs.," says Word. "At the time I started with Landoll, they had the lightest unit on the market. They are very lightweight, which is extremely important."
Despite the lower weight, the bottom dumps have proven very durable. Most of the work is on the highway, but there are some off-road excursions. "We haul on dirt roads and partially completed roads," says Word. "We haul crushed stone in them for road base delivery.
"We don't have problems with them. There are not a lot of moving parts," he continues. "We have run them long enough to actually wear through the thin steel from the sliding action of the material. We have a shop, so we just replace those areas."
A bottom dump trailer is quite versatile; yet, like any equipment, it has its limitations. "The same trailer can do airport work, site work, road work, material stockpiling or actually lay down asphalt," Ladner states. But he adds, "There are restrictions on material size that can come down through the gate and flow out cleanly underneath the axles. If you are looking to haul material that averages 1 to 2 ft. in diameter, that is really not the application for bottom dumps."
Side dumps are a stable alternative
A side dump trailer has hydraulic rams that tilt the body to dump material to the right or left side of the trailer. This allows for maximum payload, as well as rapid unloading. The trailer also remains stable during the dumping cycle.
"The tipover accident rate is so much lower than an end dump, insurance companies often charge lower premiums," says Ralph Rogers, head of research and development for Side Dump Industries.
Rogers explains that side dump trailers are particularly well suited for site prep work. The design allows the operator many options when dumping. He can stop and dump the load, windrow it or dump it over a K-rail or bridge.
"Side dumps are being used in site prep and other construction work, demolition and debris work," says Rogers. "The water-tight tub makes it ideal to haul products that would leak out of an end dump or other trailer."
Knodel Contractors, Freeman, SD, specializes in site preparation, road construction, demolition work, environmental and emergency cleanup, as well as dirt, sand, rock and gravel hauling. It extensively uses Side Dump Industries' side dump trains, which consist of two trailers hooked together.
"What I can haul in one load would take a contractor running end dumps up to four trucks alone," asserts Kelly Knodel. "Plus, my drivers can place product - whether it's dirt, gravel or rock - exactly where it needs to be. It can all be done on the run. We don't have to stop, scrape out the tub, then move the material where it's supposed to be."
The trailers' 50° dump angle ensures the product comes out faster and cleaner. "That's especially important when I am hauling dirt. Nothing sticks to the tub," says Knodel. "Another great thing about my side dumps is that the dump distance is so far from my wheels, I never worry about running over the product or damaging my tires."
Stability has been another major benefit. "We are very comfortable dumping our fully loaded trains on the run," says Knodel. "I've seen other guys tip not only the trailer, but their tractor over, causing severe damage to the equipment and the operator. My guys simply don't worry about that."
California-based G&J Heavy Haul has had similar success with its fleet of 10 side dump trailers from Side Dump Industries. The company has been hauling for many freeway widening projects in the state. During these projects, the traffic needs to keep moving.
"Where we're really seeing the side dump shine is when the grade they want the material on is lower than the traffic area and there's a K-rail separating the work area from the traffic lanes," says Gordon Archer. "We haul in base rock and dump the entire load over the K-rail onto the grade area on the move. Since we never leave the pavement, we don't drag rock, dirt and dust onto the freeway either."
G&J Heavy Haul also performs a lot of levy work, where stability is a major concern. "It can be intimidating unloading on top of a levy, particularly dumping on the water side," says Archer. "However, our side dump trailers are so stable, my drivers don't even worry about it."
Pups prove nimble
Pulled by a standard dump truck, a pup trailer has its own hydraulic ram, which makes it capable of self-unloading. This setup maximizes payload capacity without sacrificing maneuverability. A key point is that you don't have to unhook the trailer.
"They are pretty nimble, but you still need a little room because you jackknife them to dump," Beall points out. "You can really dump fast. Drivers don't have to get out of the truck to dump. You can still haul large payloads and they are pretty versatile. You can spread material well; you can pave. You can do a lot of different things with them."
Because the sliding drawbar is the key to a pup trailer, the amount of tongue slide is an important consideration. "We offer 7 ft. So when you get into a tighter area, you pull the trailer closer to the truck to make it a shorter, more nimble vehicle," Beall explains. "When you are travelling down the highway loaded, you stretch it out to meet the bridge law. And you can do that on the go."
Transfers double load capacity
The transfer trailer is nicknamed the 'slam-bang' due to the noise it makes while transferring. Pulled by a standard dump truck, unloading starts by unhitching the trailer, then dumping the load out of the standard dump box. You then back up to the transfer, which rolls on rails from the trailer to the standard dump truck box via electric, pneumatic or hydraulic power. The transfer box can then be dumped using the standard truck and rolled back onto the trailer rails.
The attraction is that you can haul two full loads of material to the jobsite. "When you get to that jobsite, you put the trailer body in the truck," says Beall. "Then you have the ability to efficiently work in a confined space."
He adds, "If you are travelling a long distance - anywhere from 30 to 50 miles from your source of material - it favors a transfer." Consider a regional comparison to a Superdump (a 16- to 18-wheel dump truck with an 11- to 13-ft. trailing axle). "We can get 32 tons [with a transfer] in Oregon compared to a Superdump, where you get 25 or 26 tons."
But there are drawbacks, like numerous working parts. They are also prone to damage. "You can drop bodies on the ground," Beall states. As such, additional training and conscientious drivers are required.
Level ground is needed to perform the transfer. And, Beall adds, "There is a limitation on where you park the trailer, because you must leave it unattended when you are unloading. Some cities and counties have cracked down. They don't want those trailer chassis sitting unattended while operators are off dumping."
Another issue is weight restrictions. "When you put the trailer body in the truck, most of the time you are overloaded because you have the weight of that trailer body," says Beall. "Some areas and cities have cracked down on that."
Weight vs. Payload
Landoll Corp. divides bottom dump trailers into two categories: heavy-duty for off-road applications, and ultra-light for maximizing road-legal payloads. Each will maximize productivity when used in the proper application.
Heavy-duty trailers feature a lot of steel and reinforcements. "They are more for real off-road applications where you are moving heavier material and never really hitting a legal highway that you have to scale," explains Landoll's Jim Ladner. You are dealing with a lot of off-road applications where the trailer is going to be twisted through shoddy-made roads, or soft conditions where they may actually be pushing a bottom dump along with a dozer. You are going to find that heavy-duty, rugged series trailer is going to tare weight heavier just so it can withstand that rugged application."
The ultra-light series is at the other end of the spectrum. Typically, it is not a rugged application. "It is made strictly for maximizing payloads for you to run on a legal highway," says Ladner. "You can move more material per trip because the trailer weighs less. Every pound you save on the trailer, you are hauling a pound more material.
Assume that you can haul an additional 1,800 lbs. with the ultra-light series. "On eight rounds that is 14,400 lbs.," Ladner points out. "That doesn't sound like too much, but if you work 22 days that month, that's 360,000 lbs. Now, let's say it's a four-month job - all of a sudden, it becomes a million pounds. That's with one truck. What if you have four, five or six trucks on the job?"
These lightweight trailers do initially cost more, but you have to consider the operating cost differences, especially if you get paid by the ton/mile. "You can be lured into a trailer that is going to cost you $5,000 less, but in a short period, you can recoup that by making the extra investment in that ultra-light series." Remember, you are talking about a trailer that is going to last six to 10 years."
But Ladner cautions you won't see the true benefit if you don't spec the right tractors for the job. "A lot of guys will try to buy a road tractor and do bottom-dump work," he notes. "You are hurting yourself by using the wrong truck. A day cab with the right wheelbase may actually weigh 3,000 to 5,000 lbs. less than that over-the-road truck."
Match Body Material to the Application
Steel continues to be the most common material used for dump body construction. However, not all steel is made alike. It's important to select the type best suited to the application.
According to Jeri Retzlaff, marketing manager, Truck Bodies Equipment International (TBEI), there are three main specifications to consider before purchase. "Brinell hardness measures the resistance to abrasion. Customers who carry sand and gravel may be concerned with this measurement, whereas a heavy construction user may not be as concerned," he notes. "Tensile strength refers to the ability to withstand load impact." Understanding tensile strength measurement would be a consideration in chassis frame construction.
The yield strength of the steel would be the most important measurement in the majority of applications. This is the ability to resist dents. "Steels used in the construction of dump bodies vary from 30,000 to 190,000 psi of yield strength," Retzlaff explains. "Typically, higher yield strengths are needed in the floor of the body, followed by the sides and rear.
"When choosing stainless steel bodies - which have approximately 35,000-psi yield strength - many customers will opt for a carbon floor of at least 145,000 psi for Class 8 bodies," he points out. "The exact specifications of the body materials depend on the customer's intended usage."
Although a more expensive option than traditional carbon steel, aluminum is becoming more popular for maximizing payload.
"It provides another material that can reduce weight by over 30% in many cases," says Retzlaff. "Contractors can utilize the weight savings to haul more material, increasing their payload and profits."
Corrosion resistance is also a primary concern in many parts of the country. "The aluminum construction helps minimize corrosion," Retzlaff comments. This, in turn, can reduce maintenance costs.
Trucks Prove a Viable Alternative
Of course, the alternative to a dump trailer is a dump truck. There are several dump truck variations available to meet regional weight and axle spacing regulations, with each offering advantages and limitations in terms of maneuverability and payload.
Standard dump trucks
Standard dump trucks feature a short wheelbase, which maximizes maneuverability. The main drawback is limited payload as specified by regional weight and axle spacing regulations.
Standard dump trucks are available in many wheel and axle configurations (from six to 14 wheels) with a choice of dump body designs to meet various applications. "Intended use is the primary consideration when selecting a Class 8 dump body," says Jeri Retzlaff, marketing manager, Truck Bodies Equipment International (TBEI). "Knowing the body's intended use, from sand and gravel to construction debris, will guide the buyer to choose an appropriate design and steel construction.
"Specifically, elliptical body designs lend themselves to uses where material typically hangs up," notes Retzlaff. "The elliptical contoured floor will assist with an easier flow. In addition, the elliptical design deflects large rocks from hitting the floor flat, which can help reduce the denting normally associated with a heavy impact."
Superdump
A Superdump is equipped with liftable pusher axles and a liftable trailing axle, which extends 11 to 13 ft. behind the rear axle to stretch the outer bridge measurement to the maximum overall length. When you are ready to dump, the trailing axle is raised up on two hydraulic arms to clear the rear of the vehicle.
This configuration allows the maximum gross weight in states that conform to the federal bridge formula. These trucks can be rated as high as 80,000 lbs. GVW and carry 26 tons of payload or more. If you are close to your source material, notes Brent Beall, Beall Corp., there is a real advantage to having a single truck that can haul up to 26 1/2 tons. The Superdump offers quick turns.
However, you must exercise caution when dumping on uneven ground due to the extreme weight. "You could damage the grade because of all of the axles on the ground," says Beall. "Technically, when your pusher axles are up, you are carrying the entire load on three axles. You are probably over the weight rating of the rear axles. As the ground gets moist, you have to be careful."
He adds that the turning radius is not great, as well.