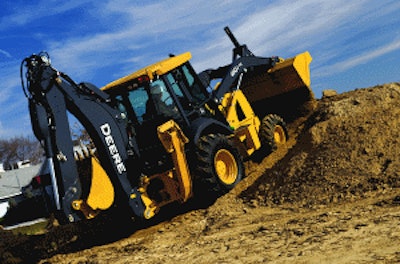
A long list of options and features allow a backhoe-loader to be spec'd to closely match your customer's needs. "The most important thing a rental business can do when adding a backhoe-loader to its fleet is fully understand the application need," says James Blower, senior product manager, JCB. "The type of application will determine the spec of the machine."
One specification that relates to application would be backhoe dig depth. "Often this spec is used more for determining reach rather than depth, but this will determine which size class to shoot for," says Bob Tyler, product marketing manager, backhoes, John Deere Construction & Forestry Division. "For example, if the application is to dig a 4-foot trench all day, then the rental customer may want to start with the 14-foot size class such as the Deere 310J, rather than the 15-foot 410J. If the application involves, say, placing stones for embankments, then the longer reach may be a consideration for some customers."
Another specification relating to application would be lift capacity. "Will the contractor be picking up manholes, or placing Jersey barriers with the backhoe?" asks Tyler. "Will the loader be used extensively for material handling? If so, higher lift specs may be an advantage. In many rental situations, the customer may already have heavier lifting equipment, so again, the [14-foot size class] may be the right solution."
Generally, a backhoe-loader is picked for its versatility. "Their advantage over other types of equipment, like tracked excavators and skid steers, is mobility," says Bargellini Marcello, Volvo Construction Equipment. "They can travel upwards of 20 mph and higher.
"Much like the skid steer, the backhoe is essentially a 'tool' that, depending on which attachment is fitted to it, can be used in a variety of applications," he continues. "Almost all backhoes are equipped with hydraulic circuits to enable installation of loader-backhoe quick-attach systems. This allows the customer to couple the machine with different attachments, like multipurpose buckets, fork frame and tines, sweepers, grapples on the front loader, and hydraulic hammers, thumbs, augers and jaw buckets on the backhoe."
Mechanical and hydraulic couplers add to the versatility. For instance, Case offers an optional factory-installed integrated hydraulic backhoe coupler.
"The Case coupler increases productivity by reducing the time required to change attachments, because the non-hydraulic attachments can be changed from inside the cab," says Joyce Szulc, marketing manager, Case Construction Equipment. "The coupler is easy to operate with push-button operation, and it maintains breakout force, unlike aftermarket couplers."
Versatile tool carrier
The loader end can come in a standard or tool carrier configuration. "Generally, a tool carrier configuration is more expensive because the loader must feature parallel lift, higher lift capacity, etc.," says Marcello. "Hence, the loader linkage is usually stronger, with extra links and probably larger cylinders. It pays for itself if used a lot in material-handling applications."
Tyler with John Deere, agrees, noting, "Tool carriers will pay for themselves when the customer is looking for maximum versatility from a piece of equipment," he says. "Being able to unload pallets from a truck, or sweep the road are just two of a variety of tasks that can be performed with a tool carrier. However, if the customer is content with just digging with the backhoe all day, then the extra cost of a tool carrier may not be justified."
But the versatility of even a standard loader design can be enhanced with a self-leveling loader control valve. "The hydraulic self-leveling loader control valve improves pallet fork work, and is easily shut off for normal operation," says Keith Rohrbacker, product manager, construction equipment, Kubota Tractor Corp.
In some applications, a loader and attachment capabilities are all that's required. "Case offers a dedicated loader/tool carrier, which is built on the same platform as its loader-backhoes," says Szulc. "The Case 570M XT is a cost-effective choice for operations requiring a durable loader with attachment versatility and rear hitch, but no backhoe."
Kubota also offers a detachable backhoe with a Category I three-point hitch to increase the versatility of its L45 model.
Reach out and touch the work
Features are available to enhance productivity and versatility on the backhoe end, as well.
For example, the ability to reposition the machine while trenching, without switching operating positions, is beneficial. "Be sure the model includes a backhoe crawling mode," Rohrbacker advises. "This allows the operator to move the machine along the trench in either direction while at the backhoe controls, saving time and money while repositioning down a long trench."
Extendible dipper sticks on backhoes have also become very popular.
"We see contractors across a wide range of applications - utility work, road and bridge work, site prep - choosing the Extendahoe option," says Szulc. "The extendible dipper stick provides extra reach that can be helpful for many applications." For example, an operator can dig a longer flat-bottom trench without repositioning the machine, which improves productivity. "It also enables the operator to place the spoil farther from the trench."
Dipper stick designs vary by manufacturer. "Most extendible dippers extend approximately 3 to 4 ft.," says Marcello. "The advantage of a design where the inner, lighter part of the dipper extends out is the resulting higher lift capacity, simpler design and no lubrication requirement." An advantage of a design where the outer part of the dipper extends is that it may allow for easier fitting of a thumb.
Your applications will determine whether an extendible dipper stick option can pay for itself. "Trenching applications are the most obvious when looking to justify the expense," says Blower. "The extendible dipper gives the machine greater reach, increasing the size of the workable trench. This becomes increasingly important when you figure 70% of a backhoe-loader's work is done on the back end."
Grab some traction
In most businesses, time is money. If the job can be accomplished more efficiently and quickly, profits can be maximized.
"Four wheel drive allows the loader bucket to be filled more quickly for loading operations," says Tyler with John Deere. "This reduces loading cycle times, which means a pile can be moved quicker, a truck can be loaded faster, or a trench can be backfilled in less time.
"In fact, less skill is needed to fill the bucket with a [four-wheel drive (4WD)] machine, since there is now effectively more grip from the tires," he continues. "It is more likely that there will be abuse and tire wear from a less experienced operator spinning the wheels in a 2WD machine while filling the loader bucket, than by having the 4WD option available in the first place."
"Most contractors don't have the luxury of operating on smooth, solid surfaces," notes Rohrbacker. "Proper tire selection helps, but four-wheel drive provides the traction required for operation on rough, uneven surfaces, or for operation on slopes, grades and hills. Using four-wheel drive, along with rear wheel differential lock, is essential when work must go on during the rainy season."
Cost should not be a factor when determining if you need to step up to a four-wheel drive machine.
"The cost difference is not extreme," says Blower. "By the time you pay to have a non-four-wheel-drive machine towed out of a predicament, you have already met or exceeded the price difference."
Four-wheel-drive models also have a higher resale value, increasing the return on initial investment. "In 2008, 97% of the backhoes JCB sold in North America were four-wheel drive, so you could easily say this is becoming the standard," says Blower.
Marcello agrees, adding, "Four-wheel drive is now more popular than ever on backhoe machines, featured in about 75% of all large size backhoes."
Still, you must balance your needs and purchase plans. "When trading for a new unit, the residual value is higher on four-wheel-drive units," says Szulc. "On the other hand, for contractors doing utility work along roadsides, or other applications where they don't have the challenges of rough terrain, a two-wheel-drive machine can be quite satisfactory."
Another option is an all-wheel-steer machine with four equal-size tires. "The all-wheel-steer machine has greater stability when using the loader end of the backhoe," says Blower. "Having all four wheels the same size gives the machine greater flotation, making it easier to maneuver in tough working environments such as snow or mud. Ground clearance is also increased with an all-wheel-steer machine."
Take control
Pilot controls have been introduced to the backhoe-loader market over the last several years.
"There are a number of advantages and disadvantages to pilot controls," says Blower. "Pilot controls increase operator comfort because they have shorter lever throws and require less lever effort. They are also more ergonomically correct, allowing an operator to keep better posture by not leaning over the 'wobble' sticks. This reduces operator fatigue, making him more productive over the length of a work day. One of the drawbacks of the pilot controls is you lose 'operator feel'."
According to Marcello, "Pilot controls, particularly when combined with closed-center, load-sensing hydraulics and variable-displacement pumps, such as on the Volvo BL70, do provide very smooth and precise control, reducing operator fatigue and increasing productivity. There are, in fact, very few and minor drawbacks, mostly relating to lack of 'function feel' - a criticism usually voiced by operators who have used wobble sticks (mechanical controls) for many years."
Just about any application will benefit from pilot controls in that the operator is more comfortable, says Tyler. "There is one area that manual controls may have the edge - if you need to run both the loader and backhoe simultaneously, say for getting out of a situation where you have mud up to the axles and you need to push with the loader, and pull with the backhoe," he says. "In this situation it can be difficult to reach the loader lever and both pilot controls simultaneously. Obviously, not everyone has a need to do this. However, Deere offers the advanced TMC controls which allow you to run both the loader and all the backhoe functions simultaneously without the need to take your hands off the controls."
As you can see, backhoe-loaders offer many opportunities to be tailored for your customers. Plus, there are the unique features only offered on specific models from a manufacturer. So make sure you know what is available and how it could apply to your operation before selecting your next backhoe-loader.