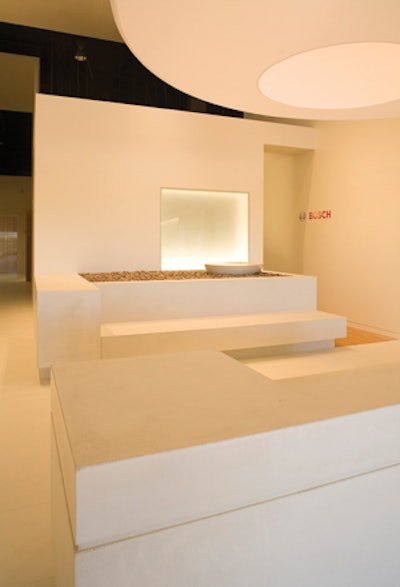
If you're looking for an alternative to traditional precast concrete countertops, here it is: glass fiber reinforced concrete (GFRC). GFRC is a composite building material that uses glass fibers instead of steel to reinforce the concrete. The result is a lighter weight product with a higher flexural strength than traditional steel reinforced concrete.
The key to GFRC is alkali-resistant (AR) glass fibers and a Polyplex curing compound, says Jim Ralston, owner of Urban Concrete Design in Arizona. "These fibers are capable of resisting the alkali attack that occurs when the fibers are mixed with normal hydrating portland cement," Ralston says. "That's the backbone of the whole thing. This random matrix of fibers transferred throughout the entire countertop is the strength of the GFRC."
Even though GFRC has been around the concrete industry for years, there are still many contractors who aren't aware of or knowledgeable about its use, especially in concrete countertops. Ralston, who has 25 years of master mould making and precast experience and is also a supplier of GFRC materials, says his company has been creating GFRC countertops and other GFRC pieces for over five years. In fact, every concrete countertop Urban Concrete Design creates uses GFRC, Ralston says.
There are many reasons Ralston prefers to use GFRC over traditional wet casting when it comes to concrete countertops. One of the biggest reasons is the weight factor. One example: Ralston created a GFRC reception desktop for a Bosch showroom in Scottsdale, Ariz. The desk was 12 feet long, 3 feet 7 inches wide and 2 feet 7 inches high. "Typically, in precast, that is going to weigh between 4,000 and 6,000 pounds. With GFRC it was 1,400 pounds," Ralston points out.
Ralston says typically the largest GFRC countertops he does are 5 foot by 10 foot pieces. But he has done countertops as long as 20 feet. And when it comes to cantilevered edges, Ralston says he will usually do them up to 24 inches. "Because of the flexibility, the GFRC actually works against itself at some point. Once the edge gets beyond 24 inches you get into an area where you need an external frame for support because the GFRC will begin to flex under its own weight," Ralston says. An admixture must be added to the GFRC to allow it to hang vertically for these drop down edges, Ralston adds.
When it comes to how large contractors can make GFRC countertops, Ralston says it's based on two factors, neither of which directly relate to the GFRC itself. "It all depends on the individual fabricators and what size casting decks they have. Another factor is how they are able to handle larger pieces," he says. If a contractor doesn't have the room to make or the ability to transport large pieces it's probably best to stick to multiple, smaller sections.
For the Bosch showroom - which also included two 9-foot-long countertops, an egg-shaped water feature and concrete benches - Ralston created a 14 foot by 4 foot deck for creating all the molds. "Off of that deck I could do the entire project. It was made out of medium density overlay plywood and coated with polyester resin so I could make pieces seamless," he says.
Another benefit of GFRC is the material has a short setup, curing and stripping time, Ralston says. "I can strip, finish, seal and install in less than 72 hours. With regular wet cast sometimes it takes 7 to 10 days to cure, and then they have to finish and install," he says.
Transitioning to GFRC countertops is not a huge leap. Most contractors doing wet cast concrete countertops will have all the tools needed for a GFRC countertop, Ralston says. The difference is in the materials, specifically the admixtures, curing compound and AR glass. "The curing compound and AR fibers are a challenge because if you're remote from a larger metropolitan area they aren't that accessible yet," he explains.
Being a GFRC supplier, Ralston didn't have any problems getting his materials for the Bosch showroom job. For him, the challenges came in the size of the pieces he was creating. The pieces were so large that Ralston went out and purchased a special pump to spray the GFRC mixes. "The challenge you run into is once you get to a certain size, you can't get the GFRC mix into the mold fast enough by hand before it begins to set," he says. The pump allowed him to spray the mix into the mold much faster.
And once the pieces were complete, Ralston had to figure out how to get them through the doorway of the building. Special carts were made for wheeling the GFRC creations in, and then the pieces were set into place.
When looking at a GFRC countertop most people won't be able to see a difference from regular wet cast countertops. But the process behind creating the GFRC countertop is quite different, Ralston says. For the GFRC mix, Ralston uses a one-to-one cement and silica sand ratio. He also adds water, a curing agent, admixtures and any colors needed.
Ralston, who teaches a GFRC training class for Cheng Design, tells contractors that GFRC can be mixed with a hand drill, mixing paddle and a 5-gallon bucket. However, unlike regular wet cast mixing, GFRC needs to be mixed in a shorter time period. "With GFRC we have such a high cement content that it has to be mixed quickly. Typically I mix within 5 to 7 minutes," Ralston says.
To be sure he mixes fast enough Ralston often uses a Collomix hand mixer. Once the mix is ready, Ralston uses a drywall hopper to spray the face coat onto the mold or pours a self-leveling mix straight into the mold.
The next step is to mix the back coat, which includes the AR glass. This gets mixed in the same fashion as the face coat, using the same tools, to make sure the AR glass is distributed throughout the entire back coat. But take caution. "When the fiber glass is added at the very end you don't want to over mix because the blades on the mixer begin to destroy the glass fibers," Ralston says. "You want to get in and mix it for about one minute."
If you prefer a self-leveling mix for horizontal concrete, Ralston says to add a self-consolidating concrete (SCC) admixture to the mix, normally the back coat. "The SCC tricks the concrete into believing it has more water then it does. It makes it so fluid that when poured out it will find its own level. At some point the switch turns and the concrete reverts back to its original water content in the cement," Ralston says.
Both the face and the back coat can be vibrated whether using a self-leveling or regular GFRC mix. A little vibrating can help achieve a level horizontal surface but is not necessary. When Ralston wants to vibrate one or both coats he hooks a vibrator to his table, turns it on and then sprays or pours the GFRC mix while the table is vibrating.
Although Ralston says most concrete countertop contractors have all the tools they will need for creating glass fiber reinforced concrete countertops, he admits that GFRC may not be the easiest material to work with. So before jumping into GFRC countertops, he suggests contractors get some training. "If you're a contractor just getting into it, training is the key that's going to save you thousands of dollars in the learning curve," he says. Often times, Ralston says the GFRC process really clicks with people after they've seen it done in person.