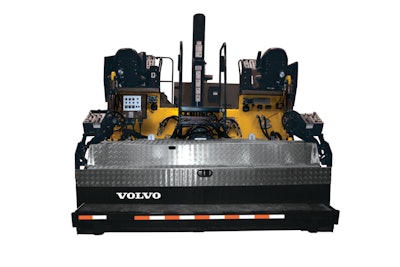
Although the asphalt paver has evolved since it was first manufactured, the asphalt paving equipment industry is seeing some recent trends and innovations that are influencing both current and future asphalt paver manufacturing.
Trends & innovations
Manufacturers agree that the trend toward electrically heated screeds is here to stay and might just be the biggest influence on current paver manufacturing. The trend toward electric screeds came about with a growing emphasis on fuel efficiency. Electric screeds eliminate the use of diesel fuel and the resulting fumes. They also offer an easier way to control heat and are cleaner thus eliminating some maintenance issues associated with diesel heated screeds, says John Sunkenberg, road industry manager for Volvo Construction Equipment.
These "cleaner and greener" screeds have been around the large asphalt paver market for nearly 15 years and have entered into the commercial paver market in the last three years, says John Hood, Bomag Americas' sales manager for paving and milling products in the United States.
The screed seems to be getting the most attention when it comes to innovations. In addition to electric screeds, manufacturers such as Dynapac are incorporating dual screeds to help compact asphalt. "Dynapac's Compact Asphalt unit has dual screeds which allows you to lay two lifts of asphalt," says Tom Chastain, Dynapac's product manager for paving and milling. "By laying these lifts simultaneously it offers better integration of the mix design and better adhesion for a stronger surface."
Another screed option is a high-density screed such as the tamping bar screeds used in Europe. These high-density screeds precompact materials before screeding, eliminating a portion of the compaction differential, Sunkenberg says. Manufacturers agree that these high-density screeds might become the standard for future asphalt pavers, and manufacturers, such as Vogele and Volvo, have or are looking to begin incorporating these screeds on their pavers in the U.S. market.
Another huge trend for asphalt paver manufacturers is a focus on operator comfort. "As manufacturers we're all trying to figure out 'If I was running this paver, would I be comfortable sitting here for eight to 10 hours a day operating. And if I put someone new in that operator's station are the controls simple enough or laid out well enough,'" Chastain says.
Ergonomics, visibility, and comfort are all playing important roles in new paver manufacturing and updates to current paver lines already on the market. For example, Bomag updated its 800 Series pavers with a lower profile for visibility and operator controls that can be adjusted to a more comfortable position for the paver operator.
Another trend is in ease of ownership responsibilities and costs. Manufacturers are incorporating longer-life wear components and fewer maintenance points on their asphalt pavers, says Vogele America's General Manager Brodie Hutchins. "Contractors used to rebuild pavers every year whether they needed to or not. Now they're wanting to extend rebuilds for two seasons or more," he says. Along with fewer maintenance points, some manufacturers are including an auto-lubrication option on pavers. This can help save the contractor time by requiring less daily manual maintenance.
One trend both paving contractors and manufacturers have been pursuing for years is a "universal paver." "Everyone is looking for a Swiss Army Knife type of paver," Hood says.
Not only are contractors looking for a paver that can do small and larger commercial and residential jobs, some are also looking for a paver that can handle more than just asphalt. "Contractors in some areas want to go into roller compacted concrete and cement-treated base, so they're looking for versatility and utilization in 'asphalt' pavers," Hutchins says.
What's new
Vogele's new Vision Series pavers offer a new alternative of Vogele pavers that were not based off any of the company's previous U.S. pavers, Hutchins says. The Vision Series, which is available in 8- and 10-ft. wheeled or tracked pavers, features an integrated leveling system and CANbus technology. CANbus allows a computer to control the running of the paver.
Volvo's 6000 paver, which was introduced in 2007, incorporates an electric heated screed. This new 10-ft. class paver also features a friction drive track and four sensors on the auger conveyor to provide more precise control of the head of material with the paver, Sunkenberg says.
Bomag's 6615 paver is a larger paver used more by municipalities and contractors paving 2,000 tons or more a day. The paver incorporates an electric screed, a 110-hp engine, and can pave up to 15 ½ ft. One unique feature is redundant controls which help keep the contractor paving, Hood says. If a switch on the paver controls doesn't work then you pull a lever instead, he says.
Looking down the road
The future of the asphalt paver equipment market, like many other equipment markets, is unclear, but that isn't stopping manufacturers from making predictions and preparing themselves for what's next.
Precision and efficiency will continue to be dominating trends. Hutchins predicts the market will see more automation advances and inclusion of GPS for slope and grade control. And electronics will become the standard over manual controls, Hood says. Tier 4 emissions regulations will also affect asphalt pavers as all manufacturers will be required to include Tier 4 compliant engines in their pavers.
The changing of asphalt mix designs may also have an effect on asphalt pavers although currently most mix designs don't require a special paver, Sunkenberg says. Warm mix, recycled, and rubber asphalt might play an increasing role in future asphalt mix designs.
Possibly the biggest consensus from manufacturers in the asphalt paver market is there will be a stronger European influence over the way U.S. contractors pave and the equipment they'll pave with. European paving standards call for a slower paving process, something both Chastain and Hood say will make its way over to the U.S. market in the future. Part of the reason, Chastain says, is because of the new mix designs contractors will be using and because a slower paving process can offer a better quality product.