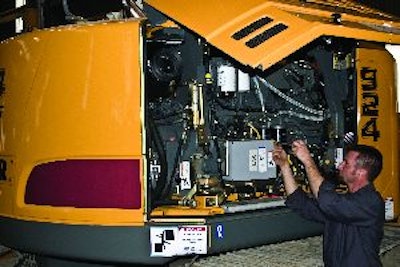
Both reduced and zero tailswing excavators can offer a tremendous advantage when maneuvering in tight, confined spaces, such as close to lot lines and foundations in a subdivision, or near traffic during road work.
"With a zero tailswing machine, the housing doesn't hang over the tracks. So you can pull up next to a wall or building and dig and swing without the rear of the machine hitting anything, or doing damage on the construction site," says Bill Gearhart, marketing and product manager, Yanmar.
But the characteristics that give them this ability can also make it a little more challenging when it comes to performing routine maintenance. And major repairs, such as rebuilding pumps, travel motors and hydraulic systems, can be more costly because more labor may be required.
"When a major component goes down, you will likely have to take the counterweight off the excavator," says Jeff Powell, general product manager, Liebherr Earthmoving. "You may not have to do that in a conventional swing model."
Same components, tighter package
The actual maintenance schedule for a reduced or zero tailswing model is essentially the same as its conventional counterpart. Routine preventive maintenance tasks such as checking the engine oil and hydraulic fluid, or changing the oil filter or air cleaner, don't change just because those components are more tightly packaged.
"You do have tighter working areas," says Gearhart. "Some of the components might be harder to get to depending on the design of the unit. That may mean it may take a little longer to do some maintenance if you have to reach through a tighter space to get to a filter, or if you have less distance to swing the handle on a ratchet wrench."
Opening the door panels may also reveal a bit different layout than service technicians are accustomed to. "Because they're in a tight area, the more the components need to be stacked on top of one another," says Powell. "In our models, the counterweight sits closer to the cab. That's where the hydraulic and fuel tanks would sit in a conventional unit. They have to be moved down, or below the engine area."
Designing in ease of maintenance
Many manufacturers have taken the more compact housing into consideration and have designed their reduced and zero tailswing models with easier maintenance in mind.
For example, technicians servicing IHI zero tailswing excavators will find all of the filters located to the outside of the machine. "This eases maintenance and serviceability," says Michael Aubrey, service manager, IHI. "Most of the filters are identical in our zero and conventional swing models, and you may only need to invest in a different type of filter wrench. Basically, everything is the same; it's just a little closer together in the zero tailswing model."
Bobcat compact excavators offer a swing-open tailgate and side access hood that provide access to the engine and pump package, valve bank, cooling system and associated plumbing, notes Greg Rostberg, marketing manager. The grease bank is centralized for easy lubrication of the slew bearing, slew pinion and swing cylinder, and track tensioning is performed via an easy-to-reach, well-protected grease cylinder fitting.
"Both types of Bobcat excavators (conventional and zero tailswing) require the same routine maintenance," Rostberg says. "The superior access designed into each model makes preventive maintenance easy, ensuring it gets completed, which in turn helps reduce operating costs and improves a contractor's bottom line."
Making maintenance easier in these machines is critical, agrees Bret Jacobson, product manager for earthmoving excavators, Liebherr. "If maintenance is difficult, it won't get done," he adds.
With that in mind, Liebherr engineers designed the new R924 compact swing excavator so that all components requiring routine maintenance are located under the right-hand door panel. "Internally, they didn't change any of the components," says Powell. "It was more in the packaging of those components."
For example, the hydraulic tank was moved under the engine. Normally, it's at the rear of the machine. "If you have to do any maintenance on it, it will take some effort because you have to remove it," Powell admits. "But the engineers were conscious of what it takes to maintain this type of unit. They made sure everything was under one door and easily accessible... Usually, you have to walk around [the machine] and open multiple doors to get to all the servicing points."
"In some regards, daily maintenance is almost easier with this model," says Jacobson. "They've put all the daily maintenance under one door that's accessible from the ground."
Take serviceability into account
When acquiring a reduced or zero tailswing excavator, it's important to take note of how easy maintenance is to perform.
"When you go to purchase a new machine, look to see where components are placed and how many panel covers need to be removed," Aubrey advises. "While there's really nothing more to maintaining a zero tailswing excavator, there are differences between manufacturers and you will want to see if components are easy to access."