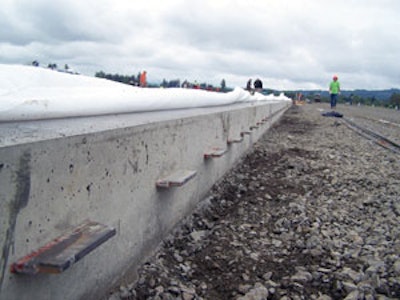
Construction joints are formed or placed into slabs to define stopping places or the extent of an individual concrete placement. There are different types of construction joints: butt-type with and without a keyway, doweled, and tied as shown in Figure 1. Dowels can be smooth round or square steel bars or plates.
Construction joints are different than contraction joints (also called control joints) but may be designed and constructed to open freely like contraction joints to help control unsightly, random slab cracking. If joints can open freely, tensile stresses caused by restrained dry and thermal concrete shrinkage are relieved. Relieving shrinkage stresses reduces the risk of random cracking. Therefore, construction joints that perform like contraction joints are desirable.
Only butt- and doweled-type construction joints can open freely or function like contraction joints. Tied construction joints cannot function like contraction joints. Also, if the slab reinforcement is continuous through a construction joint, the joint may function more like a tied joint than a contraction joint. Continuous reinforcement through joints can restrict joints from opening freely. Figure 1. Types of Construction Joints
Butt-type construction joints are basically free slab edges that deflect under forklift, wheeled traffic or vertical loads. A butt-type construction joint will not transfer loads or maintain vertical slab alignment across the joint. Even keyed joints are not recommended where vertical load transfer or slab alignment is required because the two sides of the keyway lose contact as the joint opens. As the joint opens because of concrete shrinkage, the ability of the keyway to transfer loads across the joint and maintain vertical alignment are significantly reduced. Also, concrete cracking and failure above or below the keyway along the joint edge is likely. Only use butt-type construction joints with or without keyways where vertical load transfer and alignment are not a concern.
Round dowels
Historically, 3/4 inch x 14 inch and 1 inch x 16 inch smooth round dowels spaced at 12 inches on center have been used in construction joints for 5- to 6-inch and 7- to 8-inch-thick slabs (Ref. 1). When aligned carefully and only bonded to the concrete on one side of the joint, round dowels help carry vertical loads across the joint, maintain vertical alignment of the slabs and allow slab movements perpendicular to the joint. Typically, one-half of each dowel is greased or sheathed to prevent concrete bonding so dowels are free to slip and accommodate opening of the joint. With all plate dowel systems, it is important that workers properly place and consolidate concrete around and especially under the leave-in-place pocket formers and plate dowels using internal vibrators. Otherwise, plate dowels can break out of the concrete from the top or bottom of the slab.
By allowing slab movements perpendicular to the joint, doweled construction joints can act like contraction joints and relieve shrinkage stresses perpendicular to joints. However, concrete shrinkage occurs in all directions causing slab movements both perpendicular and parallel to doweled joints. Traditional round dowels restrain or prevent slab movements parallel to joints creating tensile stresses that may cause random cracking to occur (Ref. 2).
Square dowels
Engineers first solved this problem by replacing smooth round dowels with square dowels cushioned on the vertical sides with a compressible material. Tops and bottoms of the square dowels are not cushioned so vertical loads are directly transferred from the concrete to the dowels and vertical alignment of the adjacent slabs is maintained. Using dowels with a compressible material on the vertical sides allows slab movements parallel to the joints. This reduces restrained shrinkage stresses parallel to joints and significantly reduces the risk of cracking.
Typically, 3/4 inch x 14 inch and 1 inch x 16 inch square dowels spaced at 14 inches on center have been used for 5- to 6-inch and 7- to 8-inch-thick slabs. Like round dowels, square dowels must be aligned properly and only bonded to concrete on one side of the joint in order to work. If not, joints will be mechanically restrained from opening, increasing the risk for random slab cracking. Installing and keeping round and square dowels aligned properly during the construction process can be difficult and many consider this issue a shortcoming of both round and square dowels.
Plate dowels
Diamond- and rectangular-shaped plate dowels are becoming more popular than round or square dowels at construction joints because plate dowels are more cost-effective, easier to achieve proper alignment and allow movements parallel to the joints. Plate dowel sizes typically vary from about 4- to 6-inch diamonds or rectangles with thicknesses varying from 1/4- to 3/4-inch and are typically spaced along the joint from 18 to 30 inches on center. Of course, the plate spacing depends on the plate size, loading and slab details.
Research by Walker and Holland shows diamond and rectangular-shaped plate dowels are more effective than round or square dowels because plate dowels place more steel closer to the joint where the bearing, shear and bending stresses caused by vertical loads are the highest (Ref. 3). They also showed the stresses due to vertical loads are significantly reduced beyond the first inch of the dowel past the joint and say an embedment length longer than 4 inches does not significantly increase dowel performance. Because of the plate dowel's load transfer efficiency, plate spacing along the joint is larger than typical values used for round or square dowels. Walker and Holland calculated that a 1/4-inch-thick x 4 1/2-inch diamond dowel spaced at 18 inches on center is equivalent to a 3/4-inch round dowel spaced at 12 inches on center. Figure 2. How Plate Dowels Accommodate Slab Movement
Plate dowels can accommodate horizontal slab movements parallel to joints by creating spaces along the vertical sides of the plates. Spaces allow adjacent slabs to move relative to each other in a direction parallel to the construction joint and significantly reduce the risk of random cracking caused by restrained concrete shrinkage. The spaces along the vertical sides of the plate dowels are created by: using a compressible material on the vertical sides of the plate dowels, using leave-in-place pocket formers that are slightly wider than the plate dowels, and by letting slab contraction perpendicular to the joint withdraw a diamond-shaped plate dowel from the leave-in-place pocket former as shown in Figure 2.
For the first two methods, the space is either created by the compressible material or an oversized leave-in-place pocket former. However, the third method utilizes the geometry of a diamond-shaped plate and concrete shrinkage to create spaces along the vertical edges. As the joint opens due to concrete shrinkage, the plate dowel is withdrawn from the cavity in the pocket former creating a space on each side of the plate due to the taper of the iamond-shaped plate.
Workers install plate dowels by inserting them into either a precut slot in the concrete forms or cavities in leave-in-place pocket formers that were attached to the forms and cast into the first slab. For the precut slot in the form system, plate dowels are held in place by the forms and the first side of the plate is cast directly into the first slab. With this system, there are no leave-in-place pocket formers. For the other two systems, leave-in-place pocket formers are first nailed to the forms and cast into the first slab. After stripping the forms, workers insert the plate dowels into the cavity of the leave-in-place pocket formers. When the second slab is placed, the second side of the plate dowels for all three systems becomes incased in concrete.
Because of the geometry, size of the plates and installation procedures, it is easy to achieve and maintain proper dowel alignment thus reducing the potential of mechanically locking the joint from opening. With all plate dowel systems, it is important that workers properly place and consolidate concrete around and especially under the leave-in-place pocket formers and plate dowels using internal vibrators. Otherwise, plate dowels can break out of the concrete from the top or bottom of the slab. Using plate dowels that allow horizontal slab movements both perpendicular and parallel to joints lowers the risk of random cracking.
Using plate dowels that allow horizontal slab movements both perpendicular and parallel to joints lowers the risk of random cracking. This is especially important for slabs that have two-directional doweling or slabs with long joint spacings and significant movements that commonly occur with post-tensioning or shrinkage compensating concrete. On your next slab-on-ground project, consider using plate dowels at construction joints to efficiently transfer vertical loads, maintain vertical alignment of the slabs and help reduce the risk of random cracking.
References
1. ACI 302.1R-04 Concrete Floor and Slab Construction, American Concrete Institute.
2. Ernest Schrader, "A Solution to Cracking and Stresses Caused by Dowels and Tie Bars," Concrete International, July 1991, pp. 40 -45.
3. Wayne Walker and Jerry Holland, "Plate Dowels for Slabs on Ground," Concrete International, July 1998, pp. 32-38.