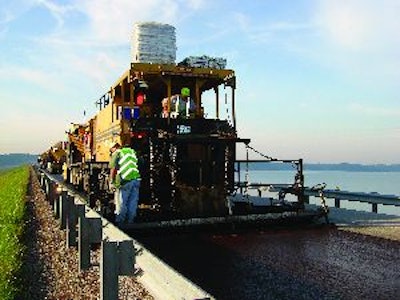
The dam road at Clinton Lake, located approximately one mile west of Lawrence, KS, received a much needed upgrade this past summer when Kansas City, MO preservation specialist Vance Brothers Inc. rejuvenated the two-lane public roadway with a two-process Cape Seal surface treatment.
Before applying the surface treatment, the contractor?s crews had to fill cracks, ranging from a ½-inch to 1-inch wide, using a rubberized asphalt material. The repaired surface was then covered with a 3/8-inch polymer modified chip seal and then a Type III (3/8-inch) microsurfacing treatment. All standard specifications outlined in the project contract had to comply with the Kansas Department of Transportation?s Standard Specifications for State Road and Bridge Construction in accordance with the International Slurry Surfacing Association?s requirements for surface treatment applications.
Vance Brothers has been serving the Midwest market since 1923, providing construction and manufacturing capabilities. Construction services provided by its experienced crews include microsurfacing, slurry seal, chip seal, under-seal, fiberized crack sealing, and Petromat installation.
On the Clinton Lake project, the asphalt road surface measured 24-feet wide at the access roads and 28-feet wide at the crest of the dam.
The south access road also has 10-foot-wide paved shoulders that run from the access road to the dam crest.
The chip seal application specified using a CRS-2P (cationic rapid-setting) polymer-modified asphalt emulsion covered by a Type CM-H washed 3/8-inch aggregate. The chip seal application could only be performed when ambient air temperature was above 60 degrees F and the pavement temperature was above 70 degrees F.
The bituminous sealer was applied at a minimum of .32 gallon per square yard at a temperature between 150 and 185 degrees F. The emulsion was then immediately covered with the specified aggregate material at a minimum rate of 24 pounds per square yard; then immediately embedded into the emulsion using a pneumatic-tired roller.
Project specifications required a minimum of three passes with the rollers to ensure adequate manipulation of the aggregate into the emulsion binder.
Inspections
Before the contractor could proceed to the second phase of the Cape Seal process, the chip seal application was inspected for deficiencies and the following was verified:
1) Finished surface has no more than four tears or untreated areas greater than 1 inch wide and 4 inches long in any 120 square yard area.
2) Joints appear to be neat and uniform without buildup, uncovered areas, or unsightly appearance.
3) Longitudinal joints have less than a 2-inch overlap on adjacent passes.
4) Transverse joints have no more than ¼-inch difference in elevation across the joint as measured with a 6-foot straightedge.
5) Chip seal edge is neat, uniform and has no more than a 2-inch variance in any 100-foot segment along the edge.
Inspections were also conducted to detect surface patterns ? ridges or streaking over the surface; bleeding/flushing ? excess bituminous material on the surface; and loss of cover aggregate ? patches of lines of aggregate lost from the surface.
Second phase
The second and final surface treatment in the Cape Seal preservation process is a microsurfacing application in which a self-propelled microsurfacing mixing machine accurately delivers the proportioned aggregate, emulsified asphalt, mineral filler, field control additive and water specified for the project.
Once mixed in a pugmill, the material is fed in a continuous flow to a spreader box.
The microsurfacing mix used on the dam road consisted of 3/8-inch aggregate, a CSS-1H (cationic slow-setting) emulsified asphalt with a polymer modified additive, mineral filler (Portland cement, hydrated lime, etc.), water and a curing additive. The mix design had to be verified by a laboratory capable of performing all of the current applicable International Slurry Surfacing Association tests. The mix design used on the dam road project had to meet the following test requirements:
- Consistency test ? 2-3 cm
- Cure time ? 2-3 hours
- Wet cohesion ? 30-minute set time (12 kg-cm minimum); 60-minute traffic time (20 kg-cm minimum)
- Excess asphalt ? 50 g/s.f. maximum
- Wet stripping ? pass (90 percent minimum)
- Wet track abrasion loss ? one-hour soak (50 g/s.f. maximum); six-day soak (75 g/s.f. maximum
- Mix time at 77 degrees F ? controllable to 120 seconds minimum
Project execution
According to Dorman Tompkins, Vance Brothers? project superintendent, the 14-man crew working on the project used a Scan Road (Bergkamp) microsurfacing paver to apply the mixture, which contained a Type III ISSA approved aggregate.
?We used a Joplin Chap lead mining by-product of 3/8-inch to minus 200 aggregate,? Tompkins says. ?We used nurse trucks to supply the rock, emulsion and water, with all the components being properly proportioned and mixed in the paver?s pugmill.?
The spreader box was equipped with two squeegees, one directly at the back of the box to spread the material and the second located 18 inches behind the first squeegee. The second squeegee provides the surface texture.
?It was pretty much straightforward as Cape Seal projects go,? says Tompkins, who?s been with Vance Brothers for 18 years. ?The road is 24 feet wide and expands to 28 feet in the center, and it has 10-foot wide shoulders on one end.
?We pulled the shoulders first and then the 12-foot wide travel lanes,? he explains. ?Our 12-foot-wide spreader box can be expanded hydraulically to 14 feet, so we were able to pull the travel lanes in one pass, even at the widest center part of the road. We also had to treat approximately 75 feet into the access roads in order to achieve good transition onto the main road.?
Even with the emulsifiers used in the mix having a one-hour cure time, Tompkins? crews had the advantage of building the project without worrying about traffic. The U.S. Army Corps of Engineers closed the road to public traffic during construction.
In total, the project required 7,000 linear feet of crack seal repair and over 50,000 square yards of surface treatment. With Vance Brothers supplying its own oil for the chip seal application and manufacturing its own emulsion for the microsurfacing portion of the project, Tompkins says it?s a lot easier to control the staging and quality of the work performed.
?When you don?t have to worry about traffic control, and you?re able to control the supply of the material you need, it makes it a lot easier to deliver a quality project,? Tompkins says. ?The Cape Seal process we used on this road will keep it in good condition for a long time to come.?