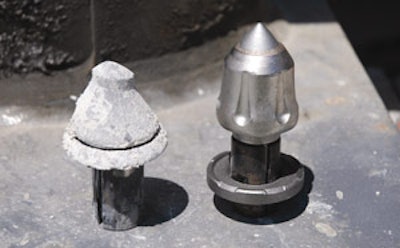
If you run a milling machine then you know that wear is going to occur. But there are some areas of the machine that naturally wear more than others. Below are the major wear parts for half-lane and smaller milling units.
Cutting teeth
The teeth, or tooling, on the drum are probably the biggest wear part of a milling machine because they are in constant contact with the asphalt. These teeth are constantly spinning when grinding the asphalt, but if buildup of material causes a tooth to stop spinning it will cause uneven wear on the tooth, says Tom Chastain, product manager for paving and milling with Dynapac. A worn tooth will affect how well the drum mills. And if the tooth isn't replaced it can wear into the holder and cause more damage to the machine and be costly to repair.
A worn tooth can be visibly seen in two ways. First, a contractor can look at the tooling on the drum and see which teeth are worn or uneven, Chastain says. Round tips indicate even wear, says Jan Schmidt, vice president of product support for Wirtgen America. If a tip is flat on one side it has worn unevenly.
A contractor can also look behind the machine at what he is milling to indicate wear. A worn tooth will produce a solid streak in the milling pattern, according to Chastain.
The lifespan of the teeth varies depending on many different factors. These include the type of material being cut, the depth of the cut, and how fast the milling unit itself is moving, says Schmidt.
How often teeth need replacing also depends on the job and the above factors, says John Hood, sales manager for paving and milling products with Bomag Americas. "Depending on the job and the scope of the work, I've seen tool changes in very abrasive, heavy cut situations done in as short a period of time as every 30 minutes," Hood says. "It's a variable that's all over the place."
Whether you're replacing teeth daily or weekly, the tooling is one wear part a contractor cannot ignore.
Moldboard wear strips
The moldboard helps clean out the trench and keeps cuts clean. These strips are often made of hardened steel or carbide, and like the teeth are in constant contact with the asphalt. That constant contact wears the strips down and can even cause the strips to bend. If they wear too far the containment door will start to wear, Chastain says. Repairs to the containment door can be costly.
Wear on the moldboard results in more material being left in the trench and a less smooth surface. As a result, the finishing crew has more cleanup work to do, Hood says.
Chastain says that on average moldboard wear strips will need to be changed once or twice a season depending on the type of material being milled.
"It's going to be a contractor's decision as far as when they want to do it. Most milling contractors have a set maintenance as far as when they do certain things. But, if the wear strips have worn themselves down to paper thin then you do need to replace them," Chastain says. "If everything looks pretty normal, then they might let it go." Contractors should also keep an eye out to make sure the strips wear evenly, he adds.
Undercarriage
Depending on what size milling unit a contractor has, the undercarriage may be tires or tracks, Schmidt says. Most half-lane units will have tracks while smaller utility units can have tracks or tires.
Tires are usually not profiled, Schmidt says, so it's easy to judge where there is wear on the tires. If you see exposed rims, the tires need to be replaced.
On tracked units, track pads cover the undercarriage to protect it from wear and damage. A worn or damaged track pad can cause inconsistent cut patterns, Hood says. "As that pad comes around, instead of making a smooth transition from the top to the ground, it's like you're walking along with a limp," he says. "And when you do that it's tough to maintain a consistent cut because sometimes your grade controls can't keep up and you don't get a good, smooth finish."
Hood suggests doing a daily visual inspection of the roller, idler, and pads to monitor wear. Worn pads will also affect traction during milling, Chastain says.
Track pads will wear down naturally, but Chastain cautions about causing premature wear as well. This can be done from stationary turning while the machine is running. "You don't really want to turn the track pads flat around the ground," Chastain says.
Another habit to avoid is climbing up over the sidewall of a cut you've made. "When you climb up over a curb or over an edge of asphalt that you've just cut you're pinching that track pad, which can put a tear in the track pad. Once you've torn it then it's going to start breaking down the bonding, and you're going to start losing chunks of the track pad. And before long you've lost that track pad," Chastain adds.
Conveyor Systems
How many conveyor belts a unit has depends on its size. Smaller utility milling units usually only have one belt that works as both the pick up and discharge belt, although some may have two separate belts. The half-lane milling units have separate pick up and discharge conveyors, Schmidt says.
Wear and tears in conveyor belts can become a serious issue. "If you get a slight tear in a conveyor belt it will go ahead and continue to rip on through. And if you lose a conveyor belt, effectively your milling job is done at that point in time," Hood says.
Cleats on the conveyor belt - raised rubber pieces that carry material along the belt - are also susceptible to wear and tears, Chastain points out. Worn or damaged cleats prevent the machine from carrying as much material as it normally does and could cause the material to go everywhere instead of where the belt is directing it.
The material being milled aids in the wear of the conveyor system. Chunks and abrasive asphalt can tear the belt, Hood says. Another possibility is the asphalt wears down the steel wear plates on the bottom side of the conveyor. If this happens a contractor may end up having to replace the entire lower assembly instead of just the belt, Hood says.
Washing down the conveyor system at the end of each day is an essential maintenance task. This prevents any material from building up on the conveyor. "If you have buildup and you can't see the components, then you can't judge if they're about to fail or not or if they need replacement. If you don't clean it you lose production time and will spend more money on repairs," Schmidt says.
But the belts aren't the only wear parts in the conveyor systems. It is also important to keep an eye on the rollers. "They all have drive rollers, return rollers, carry rollers, and cleaner rollers," Schmidt says. A worn roller can be just as detrimental to a milling unit as a worn belt.
Contractors should inspect rollers for uneven wear just like with teeth. Flat spots on a roller are a sign that the roller hasn't been turning and is wearing unevenly, Schmidt points out. And an uneven roller can cause even more downtime to the milling unit.
Uneven rollers will create more vibration. This vibration causes the belt to bounce, taking it out of constant contact with the rollers. This bouncing is another way to wear down the belts.
One other area of concern is the flashing on the conveyors. The flashing helps contain the material flow on the belt and prevents material spillage. "Flashing which is worn or adjusted too high creates a gap which allows material to escape from the belt, requiring more cleanup behind the milling machine as well as increasing material buildup, requiring further cleaning at the end of day," Schmidt says.
"Flashing which is adjusted too low, causes it to rub on the belt which can result in damage to the belt surface and, in extreme cases, even bond the flashing permanently to the belt."
The best way to monitor wear and tear on conveyors is to do visual inspections, Hood says. Chastain says to also make sure the belts are tight and cleaned on a daily basis. And make sure the belt is not angled. An angled belt will cause wear on the idlers, Hood adds.