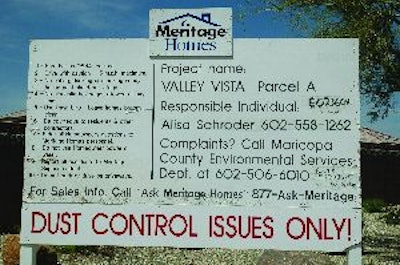
Increasingly strict regulations and steep fines should be a wake-up call that dust control enforcement is not about to go away. Instead, it is going to continue to spread.
Consider Maricopa County, AZ, home to Phoenix and its surrounding metropolitan areas. According to Lang & Baker, a Scottsdale-based law firm, the county has repeatedly failed to reach attainment of the National Ambient Air Quality Standards for airborne particulate matter. As a result, it had to adopt a plan to reduce emissions by 5% each year until it meets the standards, or face federal fines and the threat of losing $1 billion in federal highway funds.
The Maricopa County Air Quality Department (MCAQD) claims dust from unstable or disturbed surfaces is the largest contributor to the county's failure to meet federal standards. It asserts that 51% of all construction sites in the Phoenix Valley have committed dust control violations.
Predictably, the fines handed out to contractors are rising sharply. According to MCAQD, dust violations were responsible for half of the $3.7 million in air pollution fines levied in 2006. In 2007, the fines exceeded $5.3 million. This is partially due to increased enforcement.
"The number of inspectors jumped from eight to 81 in the last 18 months, and we expect that number to get bigger," says Michael Thal, Lang & Baker. "More inspectors allow for more inspections, more notices of violations and more fines."
A plan for prevention
Prevention is one of the best ways to avoid or mitigate dust control-related fines. "We try to focus contractors' attention on the practical ways to avoid dust control violations, and what to do when an inspector comes to the site," says Thal. "We also refer [contractors] to environmental consultants for help in developing a dust control plan, and to dust control equipment suppliers."
Contractors must first understand state and local dust control requirements. "Second, they must have a good dust control plan and make sure everyone on the jobsite understands it and follows it," says Thal. "If the inspector finds a violation, but believes that everyone is making a good-faith effort to enforce the contractor's plan, that by itself can reduce the fine."
There are several elements to a good dust
control plan. "In a nutshell, a dust control plan must address anything that will be done on the jobsite to comply with the rules, including such things as document storage and [logging of] maintenance; watering schedules and the amounts of water used; a description of the trackout devices used ? right down to how the contractor and subcontractor permits will be displayed," says Thal. "If it has anything to do with dust, it should be in the dust control plan."
Environmental consultants can help develop a sound plan. "A good environmental consultant can develop a specific plan that fits the contractor's operation," says Thal. "They also streamline the permitting process through their relationships with regulators, and by providing exhibits and calculations that [regulators] can rely on in approving the plan. Finally, since the plan is a dynamic document, the consultant can address changes quickly and limit the contractor's exposure."
By dynamic, Thal explains that the document needs to change to address jobsite changes, such as weather and the specific needs during different phases of construction.
"Specifically, a good dust control plan will include a schedule by which the environmental consultant performs the same testing that an inspector would," Thal says. "Testing generally measures opacity, stabilization, sieve analysis, etc."
Soil stabilization alternatives
Putting a dust control plan into action requires addressing the factors that generate dust. Since dust is created by disturbing unstable soil, this means finding methods to stabilize the loose soil around a site.
For many, water trucks immediately come to mind. "In the past, water has been construed as being a free entity," says Frank Elswick, western regional manager, Midwest Industrial Supply. "But there is actually quite a bit of cost involved with water." This includes the cost of running the truck, including the driver.
Dust palliatives can provide a lower-cost alternative. "Dollar for dollar, the one-time expenditure for dust control palliatives outweighs the constant expenditures of watering," Elswick states. "You may have five or six water trucks running at $60 to $80 an hour. Even then, they are only putting on 'band-aids'. They are not preventing the problem. There is no amount of trucks that will prevent dust on a windy day [in some arid climates]."
There are many dust palliatives available that will stabilize the soil and prevent dust at the source. These include polymers, modified resins and oil-based products. The choice of product depends on its intended use. "You kind of marry the product to the specified end use in the most affordable manner," says Elswick.
Consider haul roads. "You compact the soil that is existing, then we put a polymer right on top," says Kevin Hurst, applications specialist, Soilworks. This creates a very thin crust that seals the compacted material in. "It makes it a lot less permeable. It makes water run off instead of making mud that creates even more trackout, as well as dust issues." It also eliminates the need to continually water haul roads.
"With the polymer, it will cut down on haul road maintenance dramatically," Elswick states. "It will not completely eliminate it, but it will eliminate 90% of the potholes and rutting and those types of things. You are also getting some load stabilization benefit.
"Treating the roads ? even if you are treating a 100- or 150-ft. section before a paved area ? is a very effective way of reducing or eliminating trackout," he adds. "There is nothing picking up on the tires to track out."
The disadvantage to products that bind to the top surface layer is the inability to re-grade the surface. "If you take a grader and mess up the surface, you lose most of the advantage of the product," says Elswick.
But these products work well to maintain final grade once it's achieved. "I do a lot of construction sites in the Palm Springs area," says Elswick. "If you are in an area prone to a lot of wind, you can actually bring a project to final grade, and before you get around to building, you can actually lose grade and have to import material to account for what gets blown away." With the liquid polymer, the soil stays in place.
There are also workable products, such as wetting agents, that increase soil density. "We use it for heavy haul roads where the material is hard to compact and keep compacted," says Hurst. It allows the soil to settle in on itself a little better. "You will get less potholing. You will get less washboarding. You will be grading less because the soil becomes more dense."
Re-workable wetting agents are also useful around structures that are under construction. "You can spray those areas and it will provide dust control for long term. And you are not introducing water to your building materials," says Elswick.
When using dust palliatives, it helps to seek expert product advice. "We will come in and develop a program specific for that site, depending upon your needs, and make recommendations on product," says Elswick. "One product may be sufficient for the site [or] it may be a site where a combination of three or four products is needed."
Of course, dust palliatives are not ideal for every application. Water remains the best choice for certain earthmoving operations. "If you are constantly moving soil around, you are constantly bringing up soil that has not been treated," says Hurst. Water is probably the best solution for this scenario, since constantly re-applying dust palliative would get prohibitively expensive.
Trackout control
Trackout is a major component of dust control. Mud gets tracked onto the road and dries, then is kicked up as dust as it's disturbed by passing vehicles. "The majority of fines I am seeing over the last year are trackout related," says Thal.
Traditionally, gravel pads have been used to control trackout. This method has its downsides. "The gravel pad only works until the gravel packs down. Unless you are fluffing and replacing the gravel, not too long after the install, it is no longer effective," says Roxanne Garrett, president, Innovative Equipment Solutions (IES).
There is also the problem of cleaning the sidewalls of tires. "The simple fact of the matter is sediment comes not only from the bottom of the tires, but from the tire profile," says Garret. "Anything that is flat on the ground may help with the tread, but it is not going to do anything with what is coming off of the profiles."
Other methods for cleaning tires involve the use of water. Among these are "bird baths," which are troughs of water that trucks drive through at the entrance of the jobsite. The downside to these devices is usually the removal of the sediment from the water. "If you don't separate the dirt out, you are driving through muddy water," says Garrett. This eventually will lead to trackout.
Another option is to use employees with pressure washers. The effectiveness of this method is questionable. "To effectively spray a tire, you really can't do it by hand," says Garrett. "There is no way to give a consistent application if you are leaving it up to manual labor."
Automatic wheel wash systems provide a solution. These systems feature a heavy rumble strip that flexes the tire tread open so it can be effectively flushed out.
Proper sizing of an automated system is important. The science behind sizing is a little more complex than it may first appear. "Believe it or not, there is a bit of math to it," says Garrett. "It takes 11 ft. 6 in. to have one full revolution on an 11R24 tire, so our systems are sold in multiples of 12 ft. One, two or three tire revolutions equate to 12, 24 or 36 ft."
You also need to match the flow rates, pressure capacity and nozzle configuration to the application. The primary factors to evaluate are the number of trucks per hour and the soil type. Heavier soils are more demanding, while running more trucks will require higher flow capacity ratings.
The initial purchase price for automated wheel wash systems can vary drastically depending upon the configuration. "When we talk to our customers, we try to give them the basics, but the systems can range from a low of $27,000 to big custom jobs that are a couple hundred thousand," Garrett points out.
Depending on your situation, rental may be a better option. "A lot of our customers rent on a job to job basis, because not every site is the same. Not every system works on every site," says Garrett.
Automated systems continue to gain popularity. "The more people get used to using the systems, the less they are going to try to get by without one," Garrett asserts.
"The fines are becoming so steep in the industry, it almost makes no sense for a contractor not to use an automated system," she adds. "It doesn't take long for those fines to [outweigh] anything you would be paying for wheel washing systems."