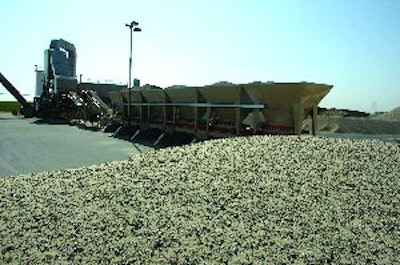
Terry Wenger, president and owner of Tri-County Paving Inc. in DeForest, WI is a man on the go. Over the 23 years of his business, he's added services to position his company as the one-stop source for customers in need of paving, gravel, grading, excavating, residential and commercial milling, pulverizing, soil stabilization and foamed asphalt recycling.
And while other contractors may have experienced the economic jitters of 2007, Wenger saw it as the right time to expand his service capabilities by adding asphalt production to his offering.
Prior to launching his own business 23 years ago, Wenger worked for another Wisconsin asphalt paving company. He started out as a driveway paving contractor and soon expanded into the excavation market.
"We do site work with our grading and excavating capabilities, but today approximately 75 percent of our business is tied to asphalt work," Wenger says. "In 2006 we placed 80,000 tons of asphalt that we purchase from other producers. Last year after we brought our new plant online, we placed 80,000 tons with our own paving crew and sold another 80,000 tons to outside customers."
Not a bad start for an asphalt contractor deciding to move into the production side of the business. Wenger, in particular, was pleased with the first year of operation, noting that it takes time for "a new producer to gain the trust of customers who've been buying from other producers."
But Wegner also notes that the investment in such a substantial plant should help convince his potential customers that he's serious about being the producer of choice in his competitive market northwest of Madison.
"There's a lot of competition out there, but we made a substantial investment in a plant that is capable of delivering whatever our customers need in the way of quantity, quality and type of mix designs," Wenger says.
The plant
Tri-County's new plant is set up in a quarry near the community of Arlington. Yahara Materials leases the mineral rights and processes all the material pulled out of the quarry, with Tri-County having exclusive rights to all the processed material produced at the site. Yahara also provides crushing and screening of the reclaimed asphalt pavement Tri-County uses in its production.
"We looked at purchasing a used plant, but then Dillman came up with a package that included new and used components, and at a price that just made it work for what we wanted," Wenger says.
Tri-County installed a Dillman 400-tph skid-mounted Unified counterflow drum mixer equipped with Hauck EcoStar ESII-125 (125 million BTUs) burner that can burn either natural gas or waste oil. Tri-County is currently firing the burner on waste oil alone.
The used equipment in the plant package included a refurbished six-bin aggregate cold feed system with a refurbished 5' x 14' single deck aggregate screen and a refurbished 30" x 70' aggregate scale conveyor. Other used components included a refurbished two-bin recycle system with a refurbished 4' x 10' single deck recycle screen and a refurbished 30" x 70' recycle scale conveyor; and a refurbished control module with controls and a refurbished PM-96 blending control system with a new I.C.E. loadout. Tri-County uses one of the bins for RAP and the other for recycled asphalt shingle (RAS).
"We produce a lot of RAP on our own projects and when working for other contractors, so we have a good available supply for our production needs," Wegner says. "We also purchase ground recycled shingles (tear-offs) from a local supplier and we're beginning to incorporate that material into the mixes we produce."
With the cost of liquid asphalt cement binder at $400 per ton (Tri-County paid $350 per ton in 2007 during the first year the plant was in operation), RAP and RAS have taken on a significant value to both producers like Tri-County and customers.
For commercial projects, like parking lots, Tri-County can produce mix designs containing 25 percent RAP content, or mix designs containing 20 percent RAP and 5 percent RAS. For city street projects or other road agency projects that use DOT Superpave mix design standards, Tri-County can use up to 20 percent RAP content in meeting specifications. If the asphalt producer wants to incorporate 5 percent RAS content, the RAP content would have to be limited to 5 percent, according to Wenger.
"We definitely want to use RAP and RAS whenever we can to offset the high cost of AC and we know the plant is set up to produce a quality mix with high content of RAP," Wenger says.
The new components in the plant package included a 10' x 54' Dillman Trunnion-Driven Unified counterflow drum assembly, a 400 tph x 98' main slat conveyor with reject gate, a 400 tph x 28' three-way horizontal transfer conveyor, three 200-ton storage silos, two vertical 30,000 AC tanks, a 3-inch asphalt pump pallet with 15-hp motor, Eddy Current drive, automated divert valve and strainer; a three-pipe package system with manual valves for two tanks, unloading pump, a 1.5 million BTU heater, a 14,000-gallon vertical fuel tank, a 100-degree external pre-heater; and a 80,000-cfm Three Module Reverse Pulse baghouse with variable frequency drive fan and ancillary equipment, a 14" x 36' primary dust auger.
Wenger is optimistic about the business opportunities he expects for the upcoming season, but more importantly the future prospects the new facility will generate.
"We have more municipal work schedule for 2008, and I'm not sure about the commercial work, but I hope to do as much as we did in 2007," Wenger says. "Long term, I do think the investment (in the plant) will lead to more business, especially municipal and other road projects, and that's the direction we want to take with the company. We started in residential but we want to move more toward the commercial and road side of the asphalt business, and I think this plant will help us do that."