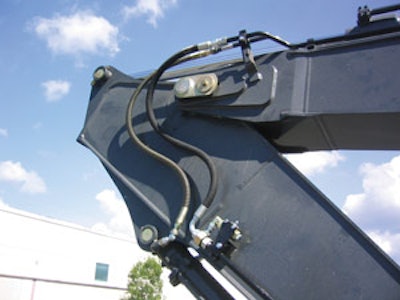
Many incidents that occur when working on mobile hydraulic machinery are careless accidents, such as slips and falls. "Fortunately, you don't hear a lot about the hydraulic injuries," says Scott Kane, global platform manager - mobile, Parker Hannifin Corp. "But when they do occur, they are very severe."
Hydraulic injuries occur mainly due to the failure to relieve pressure prior to working on a hydraulic system. "It is guys disconnecting a hose or cracking a seal... while there is still pressure in the system. Then they end up getting sprayed," says Kane.
A lot of potential energy is stored in the hydraulic system. According to Dennis Kemper, account application engineer, Gates Corp., hydrostatic systems can produce pressures as high as 8,000 psi and temperatures up to 250° F. Work groups can generate pressures up to 4,000 psi and temperatures up to 212° F. Drain or return line hoses don't have much pressure, but still have temperatures up to 275° F.
A ruptured hose releases this energy. "Unless you have ever seen a hydraulic hose rupture under 5,000 psi, you have no idea what kind of potential energy is there," says Kane. "People take it for granted."
There is also the possibility for serious burns. "Allow the system to cool to ambient temperature before performing any work on it," advises Raymond Wilkins, chief engineer, fluid conveyance, Eaton's Hydraulics Operations.
Because of the potential risks, technicians need to be qualified. "Repair personnel should be trained in safety procedures specific to hydraulics before working on hydraulic systems," says Wilkins.
Safety basics
According to Wilkins, the most generic safety procedures include ensuring cylinder-supported machine components have been blocked and/or properly restrained, then pressure relieved from the system and all cylinders, in accordance with applicable safety standards and practices. "Exactly how these steps are accomplished depends on the details of the particular system being repaired, and should be spelled out in detail in the OEM repair manual and written procedures for the equipment in question," he adds.
It's critical to avoid shortcuts. For example, Kane notes that most manufacturers of cylinders for mobile applications incorporate a counterbalance valve. The function of the valve is to prevent the cylinder from dropping if the hose breaks. "That counter balance locks everything out," he states.
But the valve is not intended to be relied on as a lockout device. "I have seen guys who have the cylinder in a raised position, and when they do maintenance, they will assume the counterbalance valve will hold the cylinder up," Kane comments. "I am not going to stick my head in there and rely on a counterbalance valve. If you have to have something extended, block it, chain it, pin it up."
Watch for clues
Hydraulic hoses often give you visual clues of impending failure. "Cover abrasion, a cracked or missing rubber cover, bent or kinked hose, oily wet hose cover and blistered cover are all signs of hose damage that may lead to failure," says Wilkins.
Of course, it isn't possible to spot all potential failures. "The obvious problems ? wear or slight leaks ? are easy to identify, but some of the failures are from within," says Kemper. "Pinholes or bursts occur because of wear of the wire or due to a bend too close to the stem. You will never see them until the hose fails."
This places an emphasis on preventive maintenance. "Hose assemblies can last a long time but not indefinitely, so a regular PM program is needed," says Kemper. "We have seen people try to use hoses for 15 years or more. While they got away with it, others were not so lucky, and that is when serious injuries occur."
"Hose is an elastomeric product," Kane adds. "It is like a belt on your car. It is going to wear out."
During a routine inspection of the hoses, Kemper recommends looking for high abrasion or wear; tight bends that exceed the minimum bend radius recommended by the hose assembly manufacturer; and areas where the hose is bent quickly from the stem. This could cause pinholes and premature failures.
Dust can also help identify leaks. "It is an accepted practice to look for collections of oily dirt or dust, which may indicate a leak," says Wilkins.
Safe inspection practices
Create a checklist for daily walkarounds. "A generic checklist should certainly include a visual inspection ? with appropriate eye protection in place ? for leaks, damaged hoses and components, twisted hose assemblies and rusted or corroded fittings and adapters," says Wilkins. "These checks, and any others that may be required, should be performed with the system properly restrained, unpressurized and at ambient temperature following the approved procedure."
If a leak is suspected, Wilkins recommends washing and drying the suspected location, then covering it with a paper towel or clean rag secured so it will not be displaced or drawn into the system. Re-pressurize the system, then visually examine the paper towel or rag periodically for evidence of leaks, while wearing the appropriate eye protection.
"DO NOT under any circumstances place hands or any other part of your body on or near a suspected leak location while the system is pressurized," Wilkins emphasizes.
Before conducting any actual repairs, it is critical to relieve all pressure in the system. "Make sure all of the hydraulic circuits are at rest," says Kane. "If it is a front-end loader, make sure the bucket is on the ground. If it is a backhoe, make sure the backhoe is down. Most pieces of mobile equipment will have gauges in the system. Make sure they all read zero. But even in that case, you can't be 100% sure that there is no pressure in the system."
If there is an accumulator in the system, the pressure must be relieved. "The most basic step is to read and follow the manufacturer's instructions for properly relieving any pressure that may be present in the accumulator," says Wilkins. "Remember that both sides of an accumulator are under pressure. Draining the fluid side does not relieve pressure on the gas side."
Proper hose assembly replacement
Building hose assemblies is a task that should not be entrusted to just anyone. "People who think they can make a hose because they can crimp it are sadly mistaken," says Lee Keddie, general manager, HKX Inc., a manufacturer of auxiliary hydraulic kits. "[At HKX], we are pretty particular about who makes the hose assembly. We have the hose manufacturer build our assemblies as much as possible, and utilize their factory trained distributors for small rush orders. We feel the same way out in the field ? it must be by certified technicians."
"Considering the safety implications, potential for environmental damage and cost associated with improperly assembled hoses, the assembly technician must be well trained in the procedures and equipment used," Wilkins agrees.
Certified technicians will understand the importance of using the correct combinations of hose and couplings, crimp dies and crimp settings, Kemper points out. "Most experienced equipment manufacturers understand this," he states. "It is not as well understood by the general public, which probably does not know the background for the development of crimp specs, such as impulse performance.
"It is critical to use the right combination of hose and couplings," he adds. "Mixing one manufacturer's couplings with another manufacturer's hose can cause catastrophic failures, such as a coupler blowing off."
"They really are a paired component," Keddie agrees. "There's a lot of technology involved in the gripping of the hose to the stem and ferrule."
Hose needs to be replaced with equivalent or better product. "Almost every manufacturer prints their information on the lay line of the hose," says Kane. "If you can't read what is on the lay line, most of the hose replacement stores can cut the hose in half and determine the hose that you need."
In addition, make sure replacement parts are with OEM-spec components. "We standardize on an ISO-approved O-ring face seal and four-bolt flange system," says Keddie. "A lot of people who do work in the field might use JIC, as an example, but that is not rated for the current pressures of 5,000 psi."
Be sure you properly torque coupler system connections. "We do specify torque values. However, we hardly ever see an installer with a torque wrench. We also supply them with a system called Flats from Wrench Resistance (FFWR)," Keddie points out. Basically, once the installer feels a resistance on the wrench, the degrees of rotation are specified in relation to the six flat faces of the nut; for example, it may specify that you turn it so the nut rotates 1/4 to 1/2 FFWR.
"In some cases, this is more accurate than a torque wrench since it is independent of joint lubrication," Keddie asserts. "The one challenge of the O-ring face seal is you can finger tighten it and if you don't torque it, the seal will work for a certain period of time before it will leak. The JIC will just not seal if you don't torque it."
To ensure nuts do get tightened properly, Keddie proposes a methodical approach. "We recommend that when you assemble the systems, you put a dot on the face of the nut after you have verified the O-ring is properly seated. Then when you actually torque the fitting, put a line across it to the fitting that it is attached to," he advises. "That is a best practice."
Injections are Serious Business
"Hydraulic injection injuries are very rare," says Scott Kane, Parker Hannifin Corp. "For that reason, most doctors and emergency rooms do not know how to treat them. That is the problem. You can't just give the guy some antibiotics, put ice on it and send him home."
Dennis Kemper, Gates Corp., explains, "This could be one of the most serious types of injury a worker can encounter. Immediate medical help is required to try to avoid the loss of a limb or even worse. Try to keep the worker as calm as possible, lay them down and keep movement to a minimum. There is little anyone but a trained medical person can do, so get help and keep them calm."
If you think you have been injected, seek immediate assistance. The injury often looks like a small pinhole. "And it doesn't really hurt a lot at first," says Kane. "So there are all of these tough guys that say I will be just fine. Don't try to be a tough guy. The first 24 hours are critical. If you can get the injury treated within 24 hours, the chances of amputation are drastically reduced."
Kane suggests keeping two web-site addresses handy in case of an injection injury. These include www.handsurgery.org, sponsored by the American Association for Hand Surgery, and www.assh.org, which is run by the American Society for Surgery of the Hand. These web sites will allow you to rapidly look up hand clinics by zip code.
Tips to Prevent Injury
Dennis Kemper, Gates Corp., provides the following tips to avoid injury when working on a hydraulic system.
- Let the unit cool down so oil is not hot.
- Refer to the owner's manual to identify the safety steps and lock-out procedures.
- Maintain a safe distance from moving parts.
- Never check for leaks using your hand. Stay a safe distance from a hose assembly that you suspect has a leak.
- Shield anyone who might be within 1 meter of the hose assembly. Normally, this is done with either a textile sleeve, such as LifeGuard, or with some type of metal plate. Be careful in the use of typical abrasion sleeving as it does not really provide line of sight protection.
- Regular PM is a must.
- Do not perform any modifications to the equipment without approval by the manufacturer.