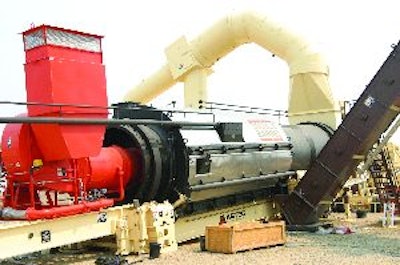
M odesto, CA-based asphalt producer/contractor George Reed Inc. has been a diehard batch plant operator for most of its 60-plus years in business. Starting out as a driveway paving contractor in 1944, serving the Greater Stanislaus County Area, the company acquired the Beerman & Jones Co. in 1960, and in doing so acquired its first hot-mix batch plant. The plant is still used today.
In 1985, the company acquired its second batch plant operation through another acquisition. Along with its concrete and aggregates businesses, George Reed acquired a third batch plant as it continued to grow over the years.
So when evaluating future growth opportunities in 2007, along with the potential of significant Caltrans' contracts, the company knew a fourth plant would be needed; and while the batch plant operations have served George Reed and its customers well over the years, it was decided that a modern drum facility should be the next addition to the company's asphalt producing capabilities.
"We were awarded a $24 million overlay on I-5 and we felt the demand from that one job alone would require drum plant technology," says Jeff Reed, president and CEO of Basic Resources Inc., parent company of George Reed Inc.
Plant installation
With future growth opportunities and a major highway contract in the wings, George Reed purchased and installed an Astec Portable 500-tph Double Barrel Drum/Mixer this past fall. The 8' x 37' drum has an expanded end and is fired by a Phoenix 125 MBTU/hr natural gas burner with lean burn capability achieved via a 100-hp blower.
The plant package also included portable 10' x 14' five-bin cold feed system, a portable 36" x 60' conveyor with 5' x 16' screen. It's also equipped with a portable 52,264-cfm express baghouse with inertial dust separator and a variable frequency drive on the exhaust fan. The plant has a 330-ton New Generation Storage System and a 10' x 60' low-profile truck scale. It's also set up with a portable 8' x 14' single-bin recycle feed system.
One of the unique features of the plant, which Reed points out as a favorable option in California, is the 12,000-cfm Blue Smoke Collection System with Fiberbed Filter.
Blue smoke is the leading cause of odor complaints at an asphalt facility. Reducing fugitive blue smoke emissions decreases the level of detectable odors from a facility and improves the work environment, as well as the surrounding environment.
Astec's Fiberbed Mist Collectors are designed to filter out blue smoke emissions from batching and mix transfer operations by routing those emissions through ducting to the collector, where the gas stream enters the enclosure and passes through pre-filters.
After passing through the pre-filters, the gas moves underneath the tube sheet and into the candle filters of the coalescing section. The Astec coalescing section design collects hydrocarbons on the inside of the filters.
As the hydrocarbon particles collect on the inside of the filters, they coalesce into droplets which drain off into the bottom of the enclosure for collection. The cleaned air moves through the filter walls and flows out through the stack. The exiting air has less than 5 percent opacity. Cleaning efficiency of the system is as high as 99.5 percent based on particle size.
The portable plant is operated from an 11' 6" x 26' 9 1/2" Pilot Control Center, which houses the Astec Total Control 2000-HMA PLC Control System. The plant is also equipped with a portable 30,000-gallon Heatec Heli-Tank liquid asphalt storage system with all the piping, pumps and metering required to control and supply AC to the mixing drum.
Going green
When George Reed purchased and installed the new plant this past fall, the asphalt producer/contractor did so with the intent of installing Astec's Green warm mix technology. This spring, an Astec Multi-nozzle Device, used to foam AC during the mixing process in order to produce mix at a lower temperature, was installed at the facility.
The benefits of warm mix asphalt, such as reduced fuel to produce the mix, lowered emission and eliminated blue smoke emissions, were an important consideration when George Reed Inc. researched its plant options.
"We definitely want to be in a position to pursue work that allows warm mix to be used and in California we see that as a strong possibility in the future," Reed says. "California has always been very conscious of protecting the environment and so we see the warm mix technology as not only a way to expand our business opportunities, but to also be a steward of the environment."
Warm mix technology allows mix to be produced and placed at a temperature that is typically 50 to 100 degrees F lower than conventional hot mix. Astec's warm mix technology achieves the low viscosity (free-flowing) at a lower temperature by foaming the asphalt with water rather than using additives Atec's Multi-nozzle Device mixes a small amount of water with the liquid asphalt to create microscopic bubbles that act to reduce the viscosity of the AC coating on the aggregate of the mix.
The 10 production valve assemblies in the multi-nozzle arrangement can produce as much foamed asphalt as required to maintain a production rate of 500-tph when all the valves are opened. As production rates vary, a computer control opens and closes the AC solenoid valves to maintain the right amount of foamed asphalt.
Ready now, future
With the new plant in place, George Reed Inc. is ready for the work at hand and the opportunity to pursue future business.
"The I-5 project represents 225,000 tons of mix and this plant will definitely take care of that," Reed says, "and I think the commitment and investment we've made to install a state-of-the-art facility will lead to other Caltrans' project and other larger projects as well."
The company's batch plant operations will also continue to serve it and its customers well. As Reed points out, the "grocery store" business of supplying lots of different customers with lots of different mix designs has been the foundation on which the company has built its business and it will continue to be an important part of its business.
"We had some internal issues to overcome in deciding to build a drum plant because our batch plant operations have always worked well in serving the type customers we have," Reed notes. "But with larger projects, like the I-5 overlay, we realized we needed a different technology to produce the quantity those jobs require."
Reed also points out that the company purchased a Roadtec Shuttle Buggy for the I-5 project. Again it a was decision based on having the right technology to deliver a customer's quantity and quality needs.
With the addition of the high-production drum facility, Reed expects the company will produce over 1.7 million tons of mix this year, and the investment in warm mix technology will undoubtedly lead to some additional growth opportunities.
"Our batch plants will continue to serve the needs of our outside customers (with 50 percent of the asphalt produced at the three batch plants going to outside customers/contractors), and our new portable drum plant will be moved as needed to serve the high-production demands of major road projects," Reed says. "Sixty-five percent of the mix produce at this new plant will be used to support our own paving crews who will focus on large highway projects. Our forte has always been quality materials and quality work. We've built our business on providing quality work and now we're in a position to do that on larger projects."