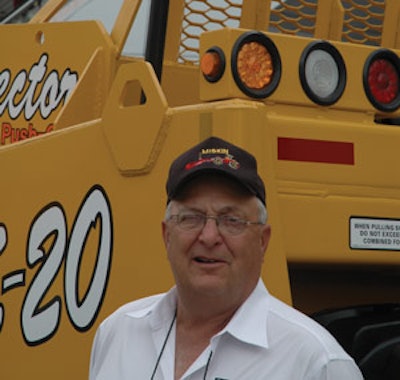
Laser and GPS systems increase the versatility of pull scraper systems when properly set up. We turned to four earthmoving professionals to get the inside scoop on how they're using grade control to enhance the performance of their equipment.
An efficient, flexible solution
Evans, GA-based Garnto Gearig Brothers Construction is a grading and utility contractor that grades large commercial sites, as well as a few residential projects. "We move anywhere from a million yds. down to 50,000 yds.," says Travis Gearig.
The company uses Reynolds 18-cu.-yd. CMX and 14-cu.-yd. 14 CS scrapers pulled by 436-hp Case IH 430 tractors. "We pull some tandems and some triples depending upon what kind of situation we are in," says Gearig. The six scraper operators vary from two to seven years of experience.
Gearig explains the benefits of the pull scraper systems. "Pull scrapers work a lot better as far as regular dirt, not wet dirt and rock. You don't have to have a dozer pushing like with a rubber-tire scraper. You cut the dozer out, and you reduce fuel consumption," he notes. "[Pull scrapers] are more efficient for hauling up to 3,000 or 4,000 ft. After that, a lot of times, we will get trucks in there."
But even on longer hauls, there are advantages to a scraper system vs. trucks. With the scraper system, one operator can load and dump. "With a truck, you have to have a trackhoe to load it and a bulldozer to knock [the soil] down after you dump it. Then you have to come over it and fine grade it," Gearig points out.
For precision work, a carry-all scraper is equipped with a Trimble laser system. "We can get to half a tenth," says Gearig. "If we have a building pad that you have to get 'dead on,' then we will have the motor grader work with the scrapers." Once the scraper does its pass, the motor grader with a laser performs the final grade to get within a couple hundredths of an inch.
In certain rough grade applications or where the tolerances aren't quite as tight, a carry-all scraper equipped with a Leica GPS has proven effective. "If we are building a lot that [requires] within a tenth, we can have the GPS on the scraper," says Gearig. "You can probably get closer than that, but we don't ever figure any closer than a tenth.
"The GPS is a lot more versatile," he adds. "With a laser, you can only shoot a flat beam."
Some roads raise and drop in elevation. "You really can't do that with a laser unless you check each point with a stick laser," Gearig states. "You just cannot beat the GPS for a road. You are not going to get it within a hundredth, but for rough grading, you can't beat it."
Construction of the electronic maps is outsourced. "They put all of the points in, then we will download that and put it in our GPS," says Gearig.
Once on site, Gearig claims it takes a little less time to set up the GPS system than the laser after you get past initial startup. "If you are starting a job, it takes longer to set the GPS up," he admits. "But once you have all of your points in there, the GPS takes less time."
One trick the company uses to save install time is to cement a pole in the ground for the base station. "We just screw our base station down on it," says Gearig. "So you don't have to go back and reprogram it."
The laser and GPS systems, in conjunction with the pull scrapers, have helped Garnto Gearig Brothers Construction succeed in a competitive market. "We can definitely be more competitive on price than the wheel scrapers," Gearig asserts.
Developing a competitive niche
Reid Laser Leveling, Ontario, Canada, has been in business since 1990. The company started out leveling fields and evolved into construction of large greenhouse sites. "I did one and it just snowballed from there," says Jim Reid.
He recently completed a 30-acre greenhouse project. Precise grading is important on such large sites, because once the water travels to each plant, it moves to the outer edges where it is picked up and sent around again.
Reid Laser Leveling uses two Miskin 15-yd. 315 scrapers and a 24-yd. 24C, which are pulled by New Holland 360-PTO-hp 9682 and 395-PTO-hp TJ450 tractors. The scrapers are mainly pulled as singles.
"We have anything from clay to sand to gravel," says Reid. "Some of the hardest loading stuff is 'blow sand.' But these things really load well. I am really impressed."
The 24C construction scraper is the most recent addition to the fleet. It enables Reid to handle the very rough terrain on the greenhouse sites. As a side benefit, he discovered the extra capacity translated into increased productivity. "I should have had the 24-yd. scraper a lot sooner," he adds. "I get double my finish time vs. [the 15-yd. scraper]."
The cutting width has also proven an important attribute for achieving final grade. Reid previously owned a 17-yd. scraper that had a 10-ft. cutting width. "I didn't like it vs. my 315 because the 315 is 15 ft. wide," he explains. Cutting width also influenced the decision to acquire the 24C. "That's why I went to the 24C for doing finishing cuts with a laser. It is 14 ft. wide on the cut."
Fixed blades are also important for accuracy. "For me, the best feature about a Miskin scraper with a laser is it is one of the only machines - unless you go to an ejector scraper - that the blades are fixed," says Reid. "So I can cut and fill on grade with a laser. With some of the dump scrapers, their blade pitches with the dump action. I actually leveled a field one time with a dump scraper and I had to go back over it with my Miskin to re-level it."
The scrapers are set up with a Trimble laser system. "When you get the scraper and the laser working together, it does a nice job," says Reid.
The finish grade is automated. An indicate system in the cab lets the operator know exactly where grade is. "I usually run on manual at first and do all of the cuts," explains Reid. "Then all you have to do is throw it in automatic. Manually, I am usually moving dirt around 10 mph. I am finishing at 6 mph."
The range with the laser is more than adequate. "You have no problems with a 50-acre site," says Reid. "I will set it up in the center."
The niche Reid Laser Leveling carved out continues to grow as the larger greenhouses continue to pop up. And with his current setup, Reid has been able to save the greenhouses money by moving dirt more efficiently than many of his competitors.
Simplifying with laser system
Southern Missouri-based Dirt Works performs primarily construction and precision land leveling for agriculture. "We try to stay within our area," says Nathan Dillenger. However, the company has also performed jobs for the Memphis International Airport.
Dirt Works currently runs John Deere 1814 and 1812 18-yd. scrapers and a Reynolds 16LSE finishing scraper. These are pulled by two John Deere 475-hp 9530 tractors and a 450-hp 9520. The tractor operators have between five and 12 years of experience running the pull-type scraper systems.
On construction jobs, Dirt Works has performed a lot of work with both stake grading and lasers. "I have been there and done them both," says Dillenger. "The laser system is so much easier."
The accuracy with the Trimble laser systems has been within hundredths. But it sometimes depends on the soil. "You may have to loosen it up to let the soil start flowing a little better," Dillenger says.
Although the pull scrapers are equipped with an automated grade control, the choice between using manual or automatic control for the final grade depends on site conditions. The automatic feature is not always the best option. "It is real sensitive," reports Dillenger. "If the wind is really bad, you can't run automatic because the light gets moving a little and it throws it all over the place."
The manual operation has not proven very difficult to use. "The receiver in the cab gives me a high light, a low light and a grade light," says Dillenger. "The grade light is green, and we try to keep it green all of the way across."
While Dillenger is sold on the laser technology, he believes some contractors are just set in the old ways of grading with stakes. "I try to tell them that they could do a much better job with the lasers," he adds.
Dillenger is now investigating a Trimble GPS system for the pull scraper systems.
Maintaining tight tolerances
Louisiana-based Quad M Investors LLP uses a Topcon laser system with its John Deere pull scrapers. The scrapers are pulled by two John Deere 9420 scraper tractors, in addition to two John Deere 8520 and 9370 tractors. The operators have five to six years experience running the pull scrapers. "The same guys run the same tractors every day," says Mark Frey.
Project sizes vary. In Baton Rouge, one job is 750,000 yds., and the company just picked up a job for 110,000 yds. It has also tackled 1/2-million-yd. jobs where the scrapers were top loaded.
On the bigger sites, the range of the higher-power Topcon laser system is a benefit. It has a range of 1,000 to 1,200 ft. on each side of the laser, or roughly 2,400 ft.
Many of the projects completed by Quad M Investors had to meet tolerances of about three hundredths. This is one reason the company chose the laser system vs. GPS. "We had the opportunity to go to the total GPS, but there was still too much discrepancy from the time you start until nightfall came," says Frey. "You had to continually go back to the benches and check the accuracy.
"With a laser, we continue to have accuracy throughout the day," he states. "If you check the transmitter while you are setting up and everything is within specs - within a hundredth on each axis - you can tolerate that. You will not have any problems."
To further enhance accuracy, scrapers used for finish work have fixed blades. "We run the ejectors to do all of the finishing work," says Frey. "The bulk hauling is done with the carry-all scrapers. Those scrapers will definitely get off grade after about half a dump."
So the 18-cu.-yd. John Deere 1812 carry-all scrapers are pulled in tandem for bulk cutting and filling, and the ejector scrapers, with a 14-ft. cutting width, are pulled as singles for finish grade work. The final grade is accomplished with an automatic grade control system.
Quad M Investors purchased the scrapers in 2001 and the units have proven very durable. "Both the carry-alls and ejectors at this point have somewhere around 9,000 hours on them. We have only had one cylinder fail, and that was on an ejector cylinder that I changed this past year," says Frey. "I am not going to trade them in. There is nothing wrong with them. As far as wear and tear, they are good scrapers."