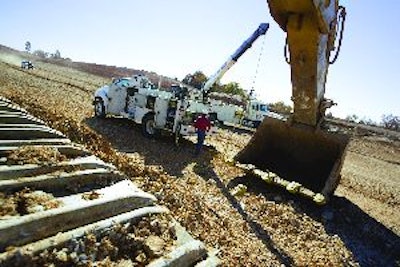
A mobile service technician equipped with a mechanics truck and service crane is a very efficient means to maximize uptime. But there are precautions the service technician should follow to ensure safe lifts.
"Today's crane service trucks have evolved along with the technology of the 21st century to become an important component of increased work site safety," says Kyle Whiteis, Auto Crane. "When a piece of equipment breaks or needs routine maintenance performed on it, having a service truck and crane on site not only gives workers the option of performing maintenance or repairs in the field or back at their facility, it allows crews to conduct that maintenance in a safer way.
"Whether that worker removes a track and works on it at the site or removes a transmission and takes it back to the shop to be fixed, he can often avoid crawling underneath or through areas that are inherently dangerous to him," he adds. "The operator can move heavier objects to a place that is more favorable for providing service, keeping the mechanic out of the way, yet still close to the job, so the equipment can get back into service faster."
However, to ensure safe lifts, service crane operation requires a knowledge of the crane, load charts and the weight of the object to be lifted.
Understand load charts
"Load charts and the weight of the [lifted] objects are the whole key to lifting safely," says Walt VanLaren, Service Trucks International, manufacturer of Tiger Cranes.
Make sure your technician understands and can read the chart. "We basically tell the owner that if the technician cannot figure out a load chart, he shouldn't be operating the crane," says Jason Ollerich, Feterl Mfg. "If you stay within the parameters of the load chart, it is pretty hard to get into any trouble."
Positioning of the crane and load does make a difference. "Cranes, outriggers and the truck work as a system to stabilize against the moment force of the object being lifted," says VanLaren. "Depending on where the crane is positioned in a rotational sense, there may be more or less ability for the body and chassis to counteract the force of the weight."
Of course, the load charts are useless if you don't know the weight of the load being lifted. Tim Worman, product manager for commercial vehicles, Iowa Mold Tooling (IMT), says one of the most common complaints the company receives is that the crane will not pick up an object that the technician thinks it should be able to handle. But when they investigate and weigh the load, it weighs more than the crane is designed to lift.
"Know the weight of what you are lifting and calculate the distance to the center line of the crane," advises Worman.
Most of today's cranes simply will not allow technicians to lift loads that are too heavy. "On the crane itself, there is an overload protection system," says Ollerich. "When the hydraulic pressure gets so high, it starts cutting out the functions that would allow you to keep increasing the load on the crane. Basically, it kicks out the electrical signal that actuates the valve. It is fool proof as long as you don't defeat the system."
Also make sure you have the appropriate amount of wire rope on the spool. "If you are doing a real heavy lift close to the truck, and you are using a lot of cable because you have your boom all the way out, keep the right number of wraps of cable on the drum so it stays attached," says Ollerich.
Use the outriggers
According to Worman, the stability of a service truck is measured with the outriggers deployed and compartments empty. Empty compartments represent a worst-case scenario; the truck will actually be more stable when it is filled with tools and other items that add weight. "But you should always use the outriggers to prevent tipovers," he adds.
Hydraulic outriggers are more likely to get used. "Ninety-nine percent of the trucks we build have hydraulic outriggers, so there is really no excuse not to use them," says Ollerich. "There is nothing wrong with a manual outrigger. It will work, it will function, it will support the load. But adding the power function to it just increases the likelihood that it is going to get used."
Age is the enemy of a manual outrigger. "When it is a new truck, that is one thing," says Ollerich. But when it gets old and becomes hard to deploy, that's when workers may take the risk of lifting without the outrigger vs. wrestling with it."
VanLaren points out, "Hydraulic up/down stabilizers are used more frequently because they are easier to deploy. Outriggers with the added feature of hydraulic extension are the easiest to use and are essentially hands off."
Besides using outriggers, you must pay attention to the ground conditions. "Be aware of the surface the truck is sitting on and its ability to support the outriggers," says VanLaren. "Use outrigger pads on soft ground."
Control the load
There are several factors that contribute to control when hoisting a load. Among these is properly attaching the load to the crane. "Rigging is very important. Make sure you carry the right slings," advises Worman. "Rig it properly to maintain control and keep the load from swinging."
The crane controls also play a crucial role in controlling the load. "Proportional controls enhance safety, especially on bigger loads," says VanLaren. "The controls give the operator the ability to feather a function in and out of engagement and control the speed once engaged. This allows the load to be moved in a controlled fashion, and minimizes swaying and bouncing. Controls that are simple off/on will apply full power every time a function is engaged, leading to a swinging and bouncing load."
Variable speed is a benefit to the technician. "Unique to Auto Crane's hydraulic cranes, the wireless FM remote's hydraulic two-speed mechanism allows for an unloaded crane to rotate at twice its regular speed to get to the load more quickly," says Whiteis. "Once the crane is loaded, the speed is automatically cut in half to minimize load swing upon stopping, thereby increasing safety."
Feterl offers Feather Touch Control. "You can be real slow when you have a load on. But when there is no load on, you pull your trigger in all the way and get your full-speed flow," says Ollerich. "If you start picking up any kind of load and you are at full speed, then it gets pretty scary pretty quick."
Tiger Cranes' Auto II Speed Control systems actually sense the load. "The system senses a load on the boom and automatically reduces the maximum operating speed of the crane by half," says VanLaren.
Wireless remotes have also become very popular for service cranes. "While wireless FM remotes are not standard on most service cranes, they are an important technological development," says Whiteis. "Technology has played a key role in the evolution of the service crane. Wireless FM remotes, for example, make it easier for the operator to position himself where he needs to be for the load, instead of being limited to a range of 20 or 30 ft."
VanLaren adds, "They provide distance from the load if necessary. The lack of a cord also reduces chances of tripping on it."
But don't let the wireless remotes lure you into a false sense of security. Even though they remove the direct connection between the operator and the crane, Worman cautions that you should never operate the service crane around power lines.
"It is a myth that you are safe because the remote removes the direct connection to the crane," he says. "You will still be within a few feet of the crane and can get electrocuted, because the ground immediately around the crane may carry a charge."
Inspect the crane
Wire rope is the most critical component on a service crane. "The wire rope assembly is required by ANSI to have a safety factor of at least 3.5," says VanLaren. But defects and damage to the wire rope during use will weaken it.
"Wire rope is probably the most critical thing to inspect," says Ollerich. "If it is taken care of and lubricated properly, wire rope will last a long time."
"Run the wire rope out and inspect it for irregularities and deformations - flat spots, kinks, frays," Worman recommends, since these can create stress points where the rope could possibly fail. Then monitor the spool on the crane to make sure the wire rope wraps around the spool correctly. Also look for any hydraulic leaks as part of a daily walkaround.
"Weekly maintenance and inspections are essential, as well," says Whiteis. "Proper torque on mounting bolts will vary from truck to truck, so consult your owner's manual. All bolts should be inspected for torque on a weekly basis."
Whiteis also recommends several other once a week checks on your service truck and crane:
- Visibly inspect all bolts and tighten as required
- Lubricate the rotation gear
- Inspect sheave bearings and replace if rough or loose
- Inspect body for any cracks around the crane box
"It may seem that quarterly inspections are less critical since they are not performed as regularly as more routine daily or weekly maintenance," says Whiteis. "Don't let the fact that this maintenance is performed less often give you a reason not to do it every three months like clockwork. This is just as important as checking your hydraulic hoses and fluid daily."
Such inspections and maintenance include:
- Inspect and grease lift cylinder bearings and the rotation bearing
- Check torque on the rotation bearing bolts
- Check and tighten bolts on rotation gear box
"At least once a year, you should drain, flush and refill your hydraulic fluid," Whiteis adds.
If a service crane is properly maintained and inspected, and the operator uses the outriggers and follows the load chart, the equipment will increase the efficiency and safety of your service technicians. However, Worman offers one final word of advice that should prevent most mishaps: "Be aware of your surroundings!"
Crane Safety Devices
Auto Crane offers the following overview of safety devices available on today's service truck cranes:
Anti-Two Block: This feature offers extra protection against potential danger if the traveling block comes in contact with the boom as the crane is being hoisted up or extended out. During operation, as the rope is retracted and the hook moves closer to the boom, the block trips the safety switch near the boom tip, shutting down the function capability of the crane. This automatic shutdown helps prevent line breakage or damage to the hoist, and is standard on most cranes today.
Hydraulic Overload Protection: Also standard in most service cranes is a sensor in the lift cylinder that monitors pressure during operation. If pressure exceeds prescribed limits, the sensor shuts off function to the crane. The sensor allows the crane to pick up only the amount of weight for which it is rated in all its positions, whether hoisting, extending or booming.
Counterbalance Valves: Counterbalance valves in a service crane's extension and lift cylinders prevent uncontrolled movement and lock the crane in where it's left, so it will not retract or extend without deliberate operation. This is particularly important in the event power is lost to the crane or a hydraulic hose ruptures, interrupting flow to the cylinders.
Redundant Pin Retention: Pins that hold cylinders in place should have dual retention, meaning if one pin fails, the bolt will not slip out since there is a second pin in place as a safety measure.
Function Interlock: Operators of most cranes in the service truck industry set the crane's speed prior to selecting an actual crane function.