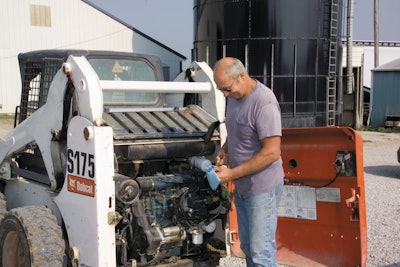
Skid-steer loaders are one of the most frequently used pieces of earthmoving equipment on a construction site. Their relatively small size, all-around versatility and maneuverability make them a quick and efficient choice for numerous applications.
Yet, skid steers can also be one of the most frequently abused, especially when you consider the inherent nature of their movement - skidding across an often unforgiving terrain. While manufacturers continue to upgrade components to make their machines more productive and reliable, there are certain things operators can do to further extend skid steer life and reduce downtime.
Consider a tire upgrade
Bucket cutting edges, teeth and attachment consumables - such as cold planer bits, hammer points, etc. - are highly susceptible to damage, says Jim Hughes, marketing manager, Case Construction Equipment. ?These components are most vulnerable because they either are the ground-engaging components, or the power for those components,? he notes.
Yet, the most vulnerable skid-steer component tends to be the tires. They are most susceptible to downtime in part because they are made of rubber, which can be scrubbed off, punctured, sliced, etc.
The obvious solution for increasing tire longevity is to avoid sharp and obtrusive objects, says Kelly Moore, Gehl. But if you?re working in harsher to severe conditions - especially in applications with rock and debris, such as demolition and recycling - upgrading the tires on the machine can certainly be a smart decision.
?Standard? tires for skid-steer loaders are typically designed with a wide sidewall, thicker carcass and higher ply rating. ?Tires are better today, but working them harder and in tough applications can cause some early wear and potential damage,? Moore notes. ?Going to an alternative tire will be advantageous.?
Switching to severe-duty or ?rock-type?, gel-filled, foam-filled or even non-pneumatic or solid tires can make a machine less susceptible to downtime caused by the inability to move. However, be aware that such options are more expensive than a standard tire.
Keep up the pressure
If you choose to stick with pneumatic tires, there are certain steps you can take to promote longevity. The most important is to monitor air pressure of all four tires to ensure it is correct and equal in each one. The appropriate air pressure can be found in the operator?s manual.
?By its nature, a skid-steer loader skids its tires left and right continuously,? says Moore. ?By not having proper and equal pressure, the machine will operate unevenly. A difference of only a few pounds will lower the performance of the tire with less pressure vs. the rest of them. The machine also doesn?t sit level on the ground. Always maintain the identical pressure that the manufacturer recommends.?
If you do end up with a tire failure, get it repaired as soon as possible. ?You don?t want to create any additional problems down the road,? says Mike Fitzgerald, Bobcat.
Be sure to carefully inspect any tire and rim assembly in which the tire has been run flat or severely underinflated. ?If you do damage to the rim and tire, call an authorized dealer or qualified repair service technician to inspect the rim and tire assembly and make necessary repairs,? advises Gregg Zupancic, John Deere Construction.
Maintenance matters
There is a direct correlation between proper maintenance and downtime. ?If your skid steer is not properly maintained, you can cause damage to the drivetrain, engine and hydraulic systems which can cost thousands of dollars [in downtime and repair],? says Hughes. ?These failures are easily avoided when the operator conducts daily grease and fluid checks, maintains the scheduled maintenance intervals and performs periodic inspection of the drive chains.
?If you service the equipment as outlined in the operator?s manual and perform the daily and periodic service, chances are [good] your machine will run more productively than if you do not,? Hughes continues. ?Daily service checks and periodic maintenance can also alert you to a wear item that needs to be replaced before catastrophic failure, potentially saving you a lot of money.?
Manufacturers continue to make maintenance easier via design features such as a single location for all check points. For example, on Case skid steers, operators can check hydraulic levels, engine oil, air filter and coolant levels all from the back of the machine.
John Deere has designed its newest skid steers to keep owning costs low by ensuring fast and easy service. Zupancic points out that the oil cooler swings out with the rear door for full, easy inspection or cleaning. ?This allows any debris caught between the radiator and oil coolers to drop straight to the ground each time the customer opens the rear door to refuel the machine,? he says.
Engine oil changes have been simplified via extended, 500-hour oil change intervals with the John Deere Plus 50 engine oil and filter. All models are also equipped with visual hydraulic fluid level checks, and a quick-pivoting cab provides access to major components within two minutes or less. All critical connectors in the electrical system utilize weatherproof seals to prevent failures due to corrosion, and instrumentation packages include a self-diagnostic check and diagnostic codes to assist in identifying problems.
Keep in mind that maintenance may need to be done more frequently in severe applications where dust and dirt can clog filters and attachments can wear out more quickly. ?Working in certain conditions may require that you clean the radiator, oil cooler and screens more frequently to keep the engine from overheating,? says Fitzgerald.
Temperature extremes - those below 0° F and above 110° F - can also adversely affect skid-steer loader performance. In addition, applications using attachments such as cold planers, stump grinders, etc., that require the machine to consistently go over relief can be hard on components.
Perform daily inspections
It?s also important to conduct a daily inspection prior to skid-steer operation.
?Walk around the machine and check the condition of guards, shields and covers,? Zupancic advises. ?Also check for worn or frayed electrical wires and loose or corroded connections. Look for bent, broken, loose or missing boom, bucket or sheet metal parts, as well as for loose or missing hardware. Check for oil leaks, missing or loose hose clamps, kinked hoses and lines or hoses that rub against each other or other parts.?
The few minutes it takes to perform the daily walkaround can promote maximum uptime by enabling you to correct any problems before failure, and subsequent downtime, occurs.