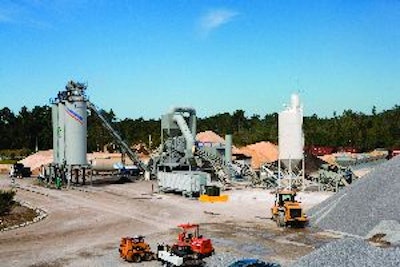
The decision to make a substantial investment in replacing a dependable plant is not an easy one for most asphalt producers/contractors, but it proved to be the right decision for Mississippi asphalt producer/contractor Dunn Roadbuilders, L.L.C.
The Cedarapids 400-tph plant Dunn Roadbuilders, a subsidiary of Dunn Investment Co. Inc., operated at its Petal, MS location provided reliable service for over 10 years, but the undersized baghouse limited production to 200 to 225 tph, and, more significantly, the asphalt producer/contractor's growth objectives.
"We spent about a year discussing how to best address the production issues, including whether or not to replace the baghouse, and finally decided that replacing the entire plant would be the best way to achieve our future growth objectives," says Rick Croy, manager of QA/QC, plant and materials.
With 67 years of cumulative asphalt production experience, Croy, along with Mike Graham, manager of plant operations, and Rusty Bradford, maintenance supervisor, were charged with the task of selecting a new plant for the company's Petal location.
Dunn Roadbuilders, which is headquarted in Laurel, MS, serves the east central and southeast Mississippi market. It has a second asphalt production facility in Laurel, and maintains a substantial inventory of mobile roadbuilding equipment capable of handling jobs of all sizes. The two asphalt plants supply the company's three paving crews, as well as other contractors and customers. Eighty-five percent of the asphalt produced at Dunn's two plants is used on DOT projects.
The decision to purchase a new Gencor Ultra 400-tph plant for the Petal location was based on the company's past experience.
"We have a 300 Gencor plant at our Laurel facility and we moved a Gecor 400-tph plant to Birmingham (operated by Dunn Roadbuilders' sister company, Dunn Construction Co.) after we (Dunn Roadbuilders was formerly the Bush Construction Co.) were purchased by Dunn Investment Co.," notes Graham. "So we've had a good working history with Gencor and we like the way the plants perform."
Plant installation
In December of 2006, Dunn began dismantling the old plant and installing the new Gencor Ultra plant, which consist of:
- Seven Gencor 10' x 14' skidded cold feed bins with 30" x 7' 6" feeders, eddy current drives, bin dividers, 30-inch collector conveyor and full bulkhead and wing walls
- 5' x 12' single-deck aggregate vibrating screen
- 30" x 50' access conveyor
- Gencor 450-tph skidded lime pugmill system with water metering system
- 30" x 70' aggregate scale conveyor
- Ultradrum Model 400 with ½-inch shell, special ceramic abrasion package, double pump AC metering system and Gencor's patented Volatile Reclaim System
- Gencor Ultra II-135 oil/gas
- burner
- Primary collector with gravity return
- Ultraflo Model CFS-151, 74,092-cfm skidded baghouse with 15,059 square feet of cloth, and 490-BCS exhaust fan with 200-hp variable frequency drive
- 14-inch auger dust return system with calibration port
- Gencor 12' x 40' skidded operator's control center with BC-250 process control, Gen 3D digital burner control, phone modem and full manual backup control console.
- HyWay HYCGO-200 hot oil heater and expansion tank
On March 14, 2007, the plant was fired up and the facility produced 125,000 tons in the first nine months of operation.
"We've been running the plant at about 310 to 320 tph with the burner operating at about 55 percent of capacity when the moisture content is at or under five percent, and we've been able to sustain the tonnage output without increasing the burner output" says Bradford.
"There have also been days when we were operating the plant at 425 tph," Graham adds. "And we've also been able to increase our RAP (reclaimed asphalt pavement) content, which will generate significant savings with more DOT projects allowing increased RAP content."
Efficient operation
Operating efficiency is also worth noting. The new plant has cut the cost of fuel needed to dry aggregate from $2.30 per ton to $1.80 per ton. Based on the 125,000 tons the plant produced during the first nine months of operation, Dunn saved over $60,000 in fuel required to fire the burner.
All in all, it's been a good investment for the asphalt producer/contractor.
With the production capacity of the 400-tph plant and the storage capacity of three 240-ton silos (Dunn purchased an additional 240-ton silo), the facility is equipped to handle multiple mix designs throughout the day in order to meet customer demand.
"We believe we're in a much better position to keep our customers satisfied and address future growth opportunities," Croy states. "We're in the process of adding a double RAP handling system that will allow us to process more RAP into the mixes we produce and we planned on doing that when we purchased the plant. (The plant control system that was installed was designed to accommodate the future upgrade of additional RAP processing equipment.)
"We have a lot of RAP coming into the facility from our own projects and we also buy RAP from other contractors," he continues. "Now that we have a plant that can produce mixes with higher RAP content, we'll be able to produce a more economical quality mix that meets the needs of our customers."
"With the old plant it was difficult to produce a mix with 20-percent RAP content," Graham says. "The inefficiency of the undersized baghouse was a big obstacle in increasing RAP without increasing emissions. But now our emissions output is much lower even when we're adding more RAP to the mix design."
Dunn also achieved additional operating efficiencies by installing variable frequency drives on the baghouse fan.
"We're now operating a plant that's more efficient, produces lower emissions, and is quieter," Bradford says. "Our neighbors like the fact that it's a cleaner and quieter plant, especially when we have to operate at night."
The investment should bode well for Dunn and the company's customers by allowing the asphalt producer/contractor to not only meet the demand of the market it serves, but to do so in a cost-effective manner.
"Whenever you can cut costs and still produce a high-quality product, everybody wins," Croy states. "We love the plant and it's a welcome change to this location. It's just good business."
About Dunn
Dunn Construction Co. was formed in 1978 as a railroad construction company in Virginia. The company moved to Birmingham, AL in the early 1900s. As the automobile became an accepted mode of transportation, Dunn recognized the potential for road paving and opened one of the country's first asphalt plants in 1915.
With offices in Birmingham, Jackson and Laurel, MS, Dunn and its subsidiaries are among the largest and most diversified construction firms in the Southeast. Its services include road-building, general construction, asphalt, ready-mix concrete and other related products.
On Sept. 1, 1996, Dunn purchased the assets of Bush Construction Co., and formed what is now Dunn Roadbuilders, L.L.C., which is headquartered in Laurel. Dunn Roadbuilders is a wholly owned subsidiary of Dunn Investment Co. Inc. and serves the east central and southeast Mississippi market. With asphalt plants in Laurel and Petal, Dunn owns and maintains a substantial inventory of mobile roadbuilding equipment. The asphalt plants support three paving crews, as well as the asphalt needs of other independent contractors and municipalities.