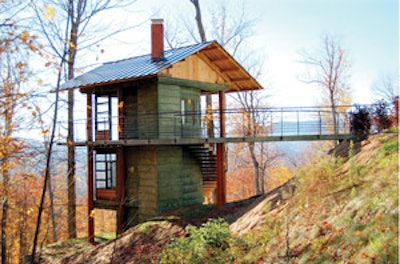
Who says a tree house has to be made out of wood? Sandy Lawton, president of ArroDesign Inc., Waitsfield, Vt., certainly doesn't think so. In September 2007, Lawton completed a concrete tree house made for a homeowner in Warren, Vt. Besides a wood roof and steel screen frames, the structure is all concrete.
It took ArroDesign a summer and a half to complete the two-level tree house. Footings were poured first to give the structure a base. After that, ArroDesign placed five 29-ft.-tall Fab-Form columns. In order to make sure no mistakes were made, two columns were poured as a test, and then the other three were completed. ArroDesign then formed and poured the 9-in.-thick walls. These walls required pours of 81/2 to 11 ft. in height. Lawton says he used a concrete mix of 4,000 psi with 3/8 aggregate and a 6-in. slump for the columns and walls.
The first floor slab was poured next, followed by forming integral beams that sat on top of the walls and were also clipped into the side of the columns. The process then continued alternating pouring walls and the second floor, Lawton says. The concrete stairs were formed using block-outs. "When we formed the outside of the wall we put those block-outs in with the rebar through there so that the rebar was sticking out," he says. "Then we were able to pull the block-outs out and form our stairs."
Perhaps the most unique aspect of this project is that instead of using traditional forms, ArroDesign used fabric. The fabric forms consisted of plywood frames and double-weave nylon textile fabric sheeting. Lawton says he has used fabric for forming before, but never with such a large-scale project. This technique, he says, allows the concrete to pillow out and create a richer texture as well as interesting shapes.
Consolidation of concrete placed in fabric forms requires a little different process than normal. "We tend not to use vibrators," Lawton says. "We generally use a mid-range plasticizer, or water reducer, and we pat the fabric with our hands to consolidate."
Lawton says this reduces the liquid on the form structure as well as reduces the chances of blowouts. "It also allows the concrete to squeeze the moisture out a little bit. So it sort of acts like a pressure release," he adds.
A complicated job like this did not come without challenges. For example, Lawton had to make sure every aspect of the project stuck to the original CAD drawings. Lawton says everything about the job was complicated, but he prefers unique projects and that is why he took on this one.
Do you have a project you would like Concrete Contractor to consider for "On the Job"? E-mail your idea to Kim Johnston at [email protected].