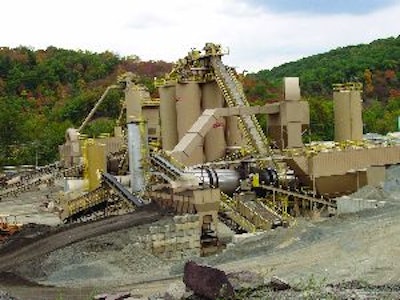
Ask Asphalt Division Manager Fred Wallenquest why Stavola chose a Dillman 600-tph skid-mounted counterflow drum plant to expand its asphalt production capabilities, and he'll likely respond: "It's built like a tank. The bearings are larger, the steel is heavier, and it's just overbuilt!"
Rick Young, corporate chief operating officer, and the Stavola family, in business since 1948 and always a leader in the industry, decided it was time for a large-scale update at one of the company's busiest locations. The search began by reviewing the main equipment producers capable of building a plant that can produce a minimum of 600 tph.
According to General Sales Manager Frank Del Guercio, the time was right. "We've built our business on service, and this plant will allow us to better serve our tonnage requirements and produce the material quality our customers demand," he states.
Stavola Contracting Company also has several large high visibility projects in the area as well. Mike Waters, contracting division manager, says the six 250-ton silos and the plant production volume mean lower costs for trucking and more crew efficiency. "It's a win-win for all divisions," Waters notes.
Since the plant was brought online in April, it has surpassed Stavola's expectations during the first five months of operation, requiring only the customary service maintenance expected for that type of output.
Wallenquest, who's been in the asphalt business for the past 20 years, and Stavola, which has been in the construction materials business for the past 60 years, have used a variety of plants over the years and the recent addition complements the arsenal of plants used to meet the productivity and growth objectives of this major Northeast asphalt producer/contractor.
Stavola operates four major division: Asphalt and Recycling Materials, Construction Materials, Contracting and Real Estate. The company operates two quarries, 10 asphalt plants, three recycling centers and gravel mining operations that in total generate over six million tons of material annually. Its Bound Brook and Tinton Falls facilities contain New Jersey's largest asphalt drum and batch plants.
Stavola's production feeds its own crews, as well as both private and public clients, ranging from individual homeowners to state and federal highway authorities.
Along with the Bound Brook asphalt facility, where the new Dillman plant and a Barber Greene batch plant are located, Stavola operates asphalt plants in Old Bridge, Brick, Tinton Falls, Howell and Millstone, NJ.
Increasing production
When Stavola purchased the Dillman plant for its Bound Brook quarry/asphalt production location, the objective was to increase productivity, as well as have the capability to increase reclaimed asphalt pavement (RAP) content in the mixes produced.
"We have a 10-ton Barber Greene batch plant at that location and we also had a Gencor plant there as well," Wallenquest says. "We moved the Gencor plant to another location and brought in the new Dillman plant."
Plant specifics
The Dillman 600-tph plant Stavola purchased includes:
- An eight-bin (10' x 16') virgin cold feed system with 36-inch self-contained collector conveyor, a 6' x 16' double-deck aggregate screen, and a 36" x 92' aggregate scale conveyor
- A two-bin (10' x 15') Series I recycle system with 36-inch self-contained collector conveyor, a 6' x 16' double-deck recycle screen, and a 30" x 80' recycle scale conveyor
- An 11' 6" x 60' Dillman Unified counterflow drum mixer with Hauck EcoStar ESII-200 extended oil and gas burner
- Dust handling equipment, which includes an 18" x 36' auger with drop chute and remote gate and 18-inch rotary airlock, 60-hp air blower package, Model AS700 (2,800 cubic foot) 12-foot-diameter atmospheric dust silo
- A 120,000-cfm Five Module Reverse Pulse baghouse with ancillary equipment
- Model 123610 two-room split-
- DEI blending control system
- Mix handling equipment, which includes three 250-ton silos, a 600-tph by 106-foot slat conveyor with reject gate, a 600-tph by 16-foot three-way horizontal transfer conveyor, and a 600-tph by 24-foot horizontal crossover conveyor
control module
The facility is operated by a Terex Roadbuilding Impulse II asphalt plant control system, which uses Programmable Logic Controller (PLC) technology and Window/E-based operator interface software to precisely control and monitor asphalt plant operations - on-site or remotely.
The system provides plant diagnostics capabilities that allow the operator to use real-time displays to monitor all functions. The system's remote plant monitoring capabilities provides access to the plant's operation via network, dial-up, Internet, local or wireless communication, providing the Stavola's management the ability to monitor operations analyze production costs.
"We set the new plant up in a way that we could tie in with the three 250-ton silos of our batch plant," Wallenquest states. "It not only gives us a lot of capacity (with the addition of three new Dillman 250-ton silos) when both plants are running, but it also gives us a lot of flexibility to produce different mix designs throughout the day."
Poised for productivity
With the two plants, Wallenquest says the Bound Brook facility will produce 750,000 tons of mix annually to support Stavola paving crews and outside customers.
"We've been running the plant (Dillman) 24/7 for the past three months (July, August, September) to supply four major paving projects, and we've been able to meet the production needs of those projects," Wallenquest says. "With our silo configuration, we're able to produce and have produced up to eight different mix designs throughout the day in order to meet the different project specification requirements on the DOT projects we're supplying, as well as the different mix requests from other independent contractors.
Along with the different mix specification requirements - aggregate size and binder type, the Dillman plant has also enhanced Stavola's ability to incorporate more RAP content into the mixes produced.
"The DOT allows 15 percent (RAP) in top course mixes and 25 to 35 percent on base course mixes, and the plant has performed well in producing those mix specifications," he notes.
When Wallenquest's Bound Brook production crew first started using the new plant, they were somewhat skeptical about whether or not it would perform up to their expectations.
"Now all they want to do is operate the new drum plant, but there are times when we still need to use the batch plant as well," Wallenquest says.
The batch plant is used when the drum plant requires normal maintenance service.
"We really have a great setup here with the two plants located in our quarry," Wallenquest says. "We commonly provide mix for 10 to 12 customers (half of those are contractors working on large projects) a day during the peak production season, and we often feed three of our own paving crews out of this location.
"We've also set up a swipe card loading system for all the (independent) truckers that haul mix from the plant to improve the efficient loading and traffic flow in and out of the facility," he continues.
"The entire facility is set up for high production, and the Dillman plant has allowed us to achieve that objective," he states. And Wallenquest is confident the plant will continue to perform at a high level.
"I come from the maintenance-side of (asphalt) plant operations, and having to oversee 10 different plant facilities, I feel pretty good about this new addition. We've been running it hard and it seems to be built for that demand."