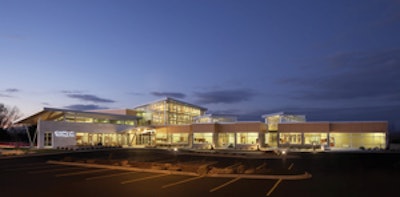
Consumers hold business owners to a high standard. You wouldn't go to a hair stylist with a bad haircut, and you've probably heard the saying "never trust a skinny chef." That's the theory commercial construction company Tri-North Builders kept in mind when building its national headquarters in Madison, Wis. The company set out to create a showcase of the latest in green building technology, and in August of this year the $8 million, 53,000-sq.-ft building achieved a LEED Gold rating.
Green features at the Tri-North headquarters include recycled denim insulation, bamboo and cork flooring, day-lighting, a green roof with indigenous plants and low-water irrigation system, and no-water urinals. The company also recycled 261 tons of construction debris and strove to utilize regional materials whenever possible.
The headquarters parking lot also includes 8,500 sq. ft. of pervious concrete, working in conjunction with asphalt and non-pervious concrete. Tom Geary, head of Tri-North's Concrete Division, explains original plans included the use of porous pavers in the parking lot. Geary saw the project as a chance for him to experiment with pervious concrete, which is a relatively new concept in Wisconsin.
"I went to the owner and pushed for him to allow us to self-perform this aspect of the project. He agreed, and I went to work learning as much as I could about pervious concrete," Geary recalls. Geary got certified as a Pervious Concrete Technician through the National Ready Mixed Concrete Association (NRMCA) and teamed with his local ready-mix supplier, LYCON Inc. in Janesville, Wis., to nail down a mix that worked well. A few test jobs were laid, and Geary was ready for the parking lot project.
On the project
With the pervious slabs at Tri-North, Geary used an air-entrained, no-sand mix with 3/8-in. aggregate and 600 lbs. total of cementitious material with a percentage of fly ash. A retardant and VMA (viscosity-modifying admixture) were also used. The mix has a very low water/cement ratio and a zero slump.
Six inches of pervious concrete was laid over a recharge bed that varied between 24 and 30 in. In areas where pervious slabs met sections of asphalt, Geary's crew installed a woven geo-textile mat to keep water draining straight down through the pervious and recharge bed to avoid water seeping under the asphalt, which might cause the asphalt to fail prematurely.
Geary says the key to success on any pervious concrete job is in the planning. "If you properly plan things, it will succeed," he says. "Once the truck arrives on the job, you have to have everything ready for the pour." Geary also thinks the NRMCA certification program for pervious concrete should be mandatory for anyone that installs pervious concrete.
He adds that curing is very important on pervious jobs due to the low water/cement ratio. Curing requires the application of a poly sheeting on top of the slab, which remains in place throughout the course of the cure, approximately seven days. "The NRMCA suggests 20 minutes between the time the mix leaves the truck to having the poly over it," Geary explains. "We try to cut that time in half if possible."
Geary had seven men working on the paving line for the parking lot job. The process moved quickly, with two men on the roller screed, four moving the concrete as it came out of the truck and one jointing and applying the poly. Expansion joints were rolled using a special pervious joint roller from Bunyan Industries.
After one winter with Wisconsin's freeze-thaw conditions and heavy snowfalls, Geary says he hasn't seen any negative effects on the pervious concrete. The pervious was plowed with conventional equipment - no special plow blades were used. Due to the large amount of snow in February and March, and no place to go with it, the snow was pushed into a large pile on the pervious concrete. The pile slowly melted well into the spring with the water draining back into the aquifer rather than running off site.
Geary emphasizes that pervious concrete has its place, and you can avoid clogging through routine sweeping and proper planning in the landscape areas. He says you want to avoid runoff from the landscape areas running directly onto the pervious as this could bring silt and other debris onto the surface and cause clogging.
Working with LEED
As head of the concrete division at Tri-North, Geary works closely with the company's LEED-accredited (LEED AP) team member, project manager Holly Hawkins. Hawkins oversees LEED projects in regards to planning what areas of a project can earn points toward LEED certification, and making sure those projects are monitored and recorded for the paperwork process required by the U.S. Green Building Council, the LEED governing body. The headquarters project was the first certification project for Tri-North, and Hawkins is currently overseeing two other projects that are planned for certification. She says for a concrete contractor it's not as important to have the LEED AP designation as it is to know about the process and how it relates to concrete.
"What's valuable for people working on a LEED project is the knowledge you gain in workshops. That's where you're going to learn the tricks of the trade," Hawkins says. The USGBC offers courses on green building and LEED certification throughout the country and online.
Hawkins says as a concrete subcontractor it's important to know what to track and how to supply the paperwork for a green project, but it's not necessary to have LEED accreditation since someone working with the general contractor, usually on the design team, will have a LEED AP designation and can submit the paperwork to USGBC for certification. She adds, "As a subcontractor you want to be involved in a LEED project early to ensure proper bidding. For example, when you start using mixes with high supplementation of fly ash and blast slag, the slabs finish slower so you might need to know about any extra time or overtime you need over a traditional slab."