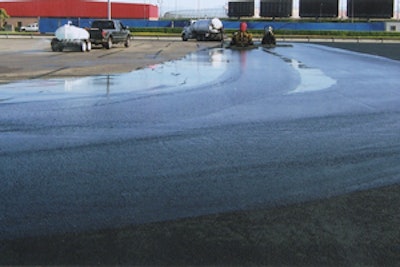
Orchestration is the key to anything in this business," says Lars Ingerslev, president, Competitive Asphalt Coatings Inc., Norco, CA. "If you have a system you're going to be that much farther ahead of the game. If you don't have a system you're going to lose. We had a system on this job, we implemented it, and it worked. And as I look back at it there wasn't another way to do it."
Probably not. So even though he's only been in business for himself for three years, his more than 20 years of pavement maintenance experience really helped Competitive Asphalt Coatings handle a 4 million-sq.-ft. sealcoating and striping job on the parking lots of California Speedway.
"No question it was the biggest job I'd ever taken on," Ingerslev says. "I'd done a 1.5 million-sq.-ft. job with my previous company, and we'd done a couple of 600,000-sq.-ft jobs but nothing on my own approaching a million square feet yet. But I wasn't worried about it at all. I didn't even blink. We just decided that whatever we do regularly we're just going to do on a bigger scale. It was a 4-million-sq.-ft. job, and it's just a big version of a 600,000 sq. ft. job, and that's how I looked at it."
"Hours and material, that's the bottom line if you're going to make money in this business," Ingerslev says. "Bid it tight and strong and bid it so we can make some money if we do it right. Then do it right. It was more of a challenge to me just to see if we could do it, just to see if we could do it in the five days we said we would - and we did."
Ingerslev had worked in the paving and pavement maintenance industry for 18 years before starting Competitive Asphalt Coatings in 2005. He had worked 18 years for another contractor, including the last four years on the job as an estimator, and he had done "everything except for payables and receivables." With encouragement from a friend, Brenda (who he married in July), he sold his house and used much of the money to build a 2,500-gal. sealcoating tank, buy a Graco LineLazer and a 325-gal. Anders sealcoating buggy, and jumped in. Three seasons into business he has 21 employees and operates two 2,500-gal. tanks, three Anders sealcoating machines, a Kubota truck with a 14-ft. squeegee, a bobtail dump truck, six LineLazers, two LineDrivers, a Bomag 3-5 ton roller, and five F450 and F550 Ford trucks. Ingerslev says 65% of his work is from pavers who don't sealcoat or stripe; the remaining 35% is from property managers. He says 80% of the work is sealcoating and striping, and 20% is patching and overlays.
Brenda has handled all the office work from a room in their home - until recently when the company acquired a location with a yard and an office building - and the next step is to provide office support for her.
"We are just so busy it's almost out of control, but it's the greatest thing that could ever have happened to us," Ingerslev says.
"This business is all I know, and it's coming pretty easy except for the office stuff," he says. "Everything about production is under control. I have that dialed-in because that's what I'm good at."
And that's a good thing because he needed all his production skills to get the California Speedway job done on time and for profit. Early this year California Speedway decided it needed to increase parking from 14,000 spaces to 15,000 spaces in four of the parking lot's five sections, so they wanted to reconfigure all their striping.
"They wanted me to black out the existing parking lines and restripe it to add parking spaces," Ingerslev says. "I told them that the black lines are going to be so easy to see on the grey asphalt that it will look like a mess and also be confusing for drivers once the new stripes are down. So they thought about it a while and asked me how much it would cost to sealcoat 4 million sq. ft. first."
There were two other bidders on the job, but the contract went to Competitive Asphalt to black out existing striping, apply one coat of sealer in each of the four 1-million-sq.-ft. sections, then layout and stripe 15,000 parking stalls. As soon as he was awarded the bid Ingerslev took his crew to the site and walked the job with them.
"It's big, and you could actually see the curvature of the Earth. When a job is that big the guys couldn't see the end," he says. "But the job was wide open - perfect conditions to sealcoat that much space. There was no traffic, no traffic control, nothing to block off. That was a real advantage because sometimes the biggest part of the job is traffic control, keeping people moving around while keeping them out of the area you're working in, and keeping your workers safe."
Preparing the pavement
As with most sealcoating jobs, the first step was to clean the pavement, and Ingerslev decided to have the black-out crew follow right behind the blowers. He bought two Graco LineDrivers to make the black-out phase go quicker.
"We had four guys pushing Billy Goat blowers and it looked just like the Air Force Blue Angels out there, the way they were staggered and moving across the lot in formation," Ingerslev says. "The guys pushing them felt like they were never going to finish."
Early on the first day Ingerslev realized the cleaning crew couldn't stay ahead of the black-out crew, so he sent the black-out crew home and let the blowers clean the area. "When the blackout crew came back the next day they could just work their way through the lot without having to wait for anything. It was much more productive," he says.
As the job progressed Competitive Asphalt Coatings was sometimes able to borrow the jet blower used to clean the racetrack. "We would borrow that when the driver was available just to give our guys a break," he says. "The lot hadn't been sealed in 10 years or so, so the asphalt was unraveling pretty good, and there was a lot to clean off."
It took the crew two days to black out all the lines, and once the first section of pavement was cleaned and blacked out, the sealcoating process began. And what a process it was. Competitive Asphalt Coatings had five days to apply 80,000 gal. of uncut sealer to 4 million sq. ft. of pavement. Western Colloid dropped two 8,000-gallon tanks of uncut 301 Park Top asphalt-based sealer at the site then was responsible for keeping the tanks filled and moving them as needed.
"From one end to the other was at least a mile, and we didn't want to have to keep driving back and forth to a single staging area," Ingerslev says. "The success of the job was based on keeping our crews moving and keeping productivity high, and we couldn't do that with a single staging area for the tankers."
So tanks were placed as close to the sections the crews were sealcoating as possible, opposite from where the work started each day, sometimes in the next section to be done. As crews finished one section Western Colloid removed the tanks and placed a new tank on the opposite side of the new section, effectively leapfrogging through the parking lot.
"We had to move the staging area as we were getting closer to the stage because we wanted it out of the way but we didn't want to travel too far to pick up material," he says.
Ingerslev says the sealcoating operation was orchestrated throughout the project. Ambient temperature was 100°F throughout the job and pavement temperature at one point reach 180°F, so a water wagon misted the surface, cooling it off ahead of the 2,500-gal. sealcoating trucks. Two 2,500-gal. trucks cycled through the job, with one applying sealer while the other refilled from the storage tank. An Anders 325-gal. buggy edged around bleachers, light poles, fence posts, and other hard-to-reach areas, and two other Anders units followed the big tanks to finish out the job. A Kubota tractor outfitted with a 14-ft. squeegee blade Competitive Asphalt Coatings built just for this job also worked behind the tanks.
"It took us a little more than half an hour to empty the 2,500-gal. tankers. The pavement was old and very dry so it soaked it up real fast," Ingerslev says. "We would keep going and Western Colloid ran back to L.A. to come back and fill up or swap out the big tanks," Ingerslev says. "We were really hoping they could keep up and give us 20,000 gals. we needed on that job each day. And they pulled it off, and we pulled it off."
Each 2,500-gal. tanker had a driver and an operator on the back operating the valves. The initial plan was to keep each operator and driver together on the unit, but that changed early in the work.
"These guys were a team, and their job was to get the tanker filled up from the big tanks, drive to the hydrant and add the water to cut the material, and make sure to have that tank ready as soon as the other 2,500-gal. tanker was empty so there was always one tank filling up and the other tank out there putting down material," Ingerslev says.
But Ingerslev soon realized the crew could be even more productive with a little more specialization. "The biggest thing was to keep these guys going so there was never a time when material wasn't coming - from Western Colloid to the site, from the storage tanks to the tanker, and from the tanker to the pavement," he says.
So to make sure that happened Ingerslev kept an eye out to see if any workers were better at certain jobs, moving people around as the process evolved.
"I was driving an F250 pulling the water wagon, and I was watching this all happen. I saw that guys were using their fill time to take a break - and that was not the time to take a break," he says. "It took me three or four loads to realize what was happening, but I finally figured it out and we made some adjustments.
"I realized one of the four guys was the best valve operator and one was the best driver, so we put those two together and all they did was drive the tanker and put down material. The other two guys became responsible for filling the empty tanker with raw sealer and water and getting it ready to hand off to the driving crew."
Final striping
Once the sealcoating was finished Competitive Asphalt Coatings could attack the striping, which was Ingerslev's only concern. "We bid it assuming X amount of stalls per day, and if we couldn't do that then labor costs would go up and profits would go down," he says. "Striping didn't go as well as the sealcoating or as well as we'd planned, but it went okay."
Because the entire purpose of the job was to reconfigure the parking lot for an additional 1,000 parking spaces, California Speedway hired engineers to design the layout. The engineers then established reference points, which Competitive Asphalt's six-person striping crew used to get started. Early on in the striping phase Competitive Asphalt had six people on the striping crew: three people working on layout behind the engineers, two painting lines, and one person straining paint and staging buckets.
"One guy's job was to strain paint to have it ready for painting," Ingerslev says. "It was hard to do with the black paint because two people were driving, so they went through the paint so fast. But he did a nice job once we got to this point." The paint strainer also was responsible for staging buckets of paint across the parking lot.
"Just like other aspects of the job we didn't want a lot of wasted movement, so we figured that it would be easier to stage the buckets across the lot instead of driving back to a staging area when empty, filling up, and then driving back to where you left off on the parking lot," Ingerslev says. "He had to know how far five gallons would get them and then have a bucket of strained paint ready for them when they reached that spot. It was a real challenge, but it was much quicker than doing it the other way."
He says the crew also turned it into a personal challenge, almost a game, where the two people striping were constantly trying to catch up to the three doing layout, and the strainer was working to see how close he could hit the spot right on so the paint was right where they needed it.
Ingerslev says relying on the ride-on attachments had a big impact on helping the crew get the striping done on schedule. "This job was the first time we used ride-on machines, and our workers got broken in on them doing the black outs," he says. "You can't mess up on black out so by the time they had to use them on the actual striping they could use them pretty well, and they painted all the new stalls with the ride-on machines."
He says his crew found line stops and starts to be the biggest challenge with ride-on machines. "I was out there watching them and worrying that there was no way they were hitting their marks, but they did, all the way across," he says.
But he says the striping didn't go as quickly as he'd anticipated, partly because of delays waiting for the engineers but also because he frequently had to reduce crew size on the California Speedway project to handle other clients.
"We had a job in Flagstaff, AZ, that we needed to get a crew on, and we had other local work. We had to cater to other customers because you can't forget about them," he says. "So striping became fill-in work for us toward the end of the project and we'd take care of our other work and then send a crew over there to get done what they could. Toward the end of the job we often only had three people doing the striping. That didn't increase our costs at all, but it did slow our work."
Fast-paced finish
Ingerslev says planning was the key, and he felt a little like a conductor orchestrating the job on the site.
"We had trucks coming and going throughout the day, there were tankers filling up and putting down sealer, sealer buggies were following to spread it and finish it off. There was activity all over the place," he says. "It was like a NASCAR pit stop, especially filling the tankers from the storage tanks. I was joking with the guys a little bit about 'how fast can you do this? How fast can we change this hose pump and get it connected? How fast can we fill this truck?'
"Because the key to this job was how can we be the most productive. How can we start putting the sealer down, and how can you do it without stopping; because as long as the buggies are moving in the right direction we were going to be okay," he says. "I was being a conductor, watching everything that was going on, watching how we were going through sealer, deciding when to move tanks and where, and basically orchestrating the entire thing.
"But the crew is what made this job happen. I could have done all the planning I wanted, but if they hadn't pulled together as a team and executed the plan, and if they hadn't been able to adjust to some of the changes we made on the site, we couldn't have pulled this off."