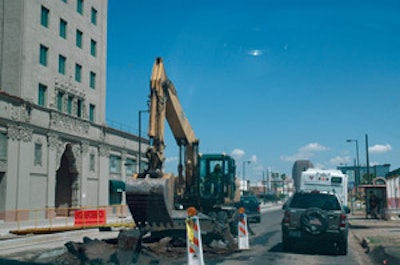
In the 1950s when the first hydraulic excavators were introduced, the machines were all equipped with rubber-tire undercarriages. Such configurations continue to be highly popular in Europe today.
In North America, however, wheel excavators have yet to achieve firm footing. "They are still considered a niche product," says Bill Metzgar, product training coordinator, Doosan Infracore America. Popular among county and state governments, these machines are just starting to see more use in road work and scrap handling operations, he adds.
Chad Cremeens, wheel excavator marketing for NACD and LACD, Caterpillar Inc., agrees that wheel excavators are still largely viewed as niche machines. "But for many, it's a niche machine they cannot live without," he says. "For years, the wheel excavator has been an essential part of governmental fleets (municipalities, highway departments, etc.). Recently, private contractors have started to realize the value, as well."
Instant mobility
Archer Western Contractors, a division of The Walsh Group, is one such company. This general contracting, construction management and design-build firm handles building, civil and transportation projects throughout the country.
Its Phoenix Regional Office is nearing completion of one the segments of the Valley Metro Rail Line, a light rail system that will run through the heart of downtown Phoenix. Four wheel excavators - two Caterpillar M318s and two M322s - have been on the job almost since its inception roughly 26 months ago. Mobility is the primary reason they were brought in.
"We have nine miles of work through city streets and we have to be able to be a little like 'nomads' - go to work someplace for a few days, pick up and run down the street four blocks, work for a couple of days, then pick up and run down the street to another location," says Bob Fouty, senior project manager.
Being able to make those moves without bringing in transport vehicles is a huge benefit. "We can just basically run them through the streets," says Fouty of the wheel excavators. "It was really site logistics and the need to be completely mobile at a moment's notice."
As part of the project, Archer Western will have performed a complete reconstruction of all the utilities that will pass underneath the future rail line. "We had about 75,000 lineal ft. of storm, sanitary and water mains to replace as part of this construction," says Fouty. "And of course, those are all made up of runs that are 40, 50 or 60 ft. long. It's not one big, continuous pipe."
The rubber-tire excavators proved invaluable for this task. "We used them on all the utility relocation. That was kind of their duties," says Fouty. They were also busy tearing up pavement, sidewalks and curb and gutter, as well as moving Jersey barriers around the site. "For what we used them for, they were workhorses for us for two years."
Their mobility proved crucial to staying on schedule. "Here's an example of a situation we encountered over and over," Fouty cites. "We would be installing a utility - maybe it's a 12-in. water line that crossed Washington [Street]. During the course of the work, we would find an unknown utility. That work stops. You have to either backfill the ditch or shore it, cover it with plates, then be able to pick up and move up the street maybe a block and a half.
"It just became readily apparent we needed that instant mobility, and the ability to make that move without having to arrange a lowbed truck to put a crawler on," Fouty says.
Ease on down the road
Ease of movement around and to jobsites is one reason wheel excavators are such an integral part of the equipment fleet at K-Five Construction, Lemont, IL. This heavy highway construction contractor handles 135+ jobs each year, ranging from large parking lots to interstate highways and airport runways, in and around the Chicago area.
The company has been using Gradall chassis-mounted excavators for nearly four decades. "They eliminate the lowboy," says Dave Gorski, equipment superintendent. "They're easier to move up and down big jobs. You don't have to have a lowboy on site to move them if you have a larger, longer job on the highway."
This means transport vehicles are free to move other, less mobile machines. "We try to keep our fleet unit numbers to the point where the utilization numbers can stay high," Gorski says. "With that in mind, and all of our equipment and the number of jobs we do, our lowboys are tied up moving other equipment every day."
Their self reliance also means the wheel excavators can handle multiple tasks throughout the day. "The guys can go back and forth between two or three jobs if they have to," says Gorski.
In addition, the highway-speed Gradalls have the capability to be street legal. "The Gradall is licensable for highway use," Gorski points out. "It is a regular on-highway truck chassis with the excavator mounted on top."
Cost comparisons
Cost could be one reason wheel excavators haven't gained more ground in the U.S. They can carry an initial purchase price premium of 10% to 15% over track models, Cremeens points out.
"The components included in the rubber-tire undercarriage increase the initial cost and the maintenance costs of the machine," says Bill Thomas, vice president of marketing and sales, Gradall Industries Inc. Yet, these costs can be offset by the versatility and speed the undercarriage offers. "The flexibility of attachment design and the rubber-tire carrier allow the machine to maneuver around the job better than a crawler."
"The advantage of a [wheel excavator] is that it can eliminate wasted idle time and the cost associated with truck transportation," Cremeens states. "But once on the job is when you see the real value. Jobsite mobility is key to the wheel excavator's success and where you see the advantages it offers over tracks."
Cremeens likens the debate between tracks and wheels to that between computer formats. "The desktop [computer] costs a little less than a laptop, but it is hard to carry around," he comments. "I can take a laptop from place to place and be productive. The laptop provides great mobility and versatility."
For the majority of manufacturers, the upperstructures of their wheel and crawler excavators are comparable. "From the swing ring up, both machines are (or should be) practically identical," says Bret Jacobson, product specialist - excavators, Liebherr Construction Equipment Co. "The differences are mostly in the undercarriage."
As such, the owning and operating (O&O) costs between the two configurations should be similar - as long as the machines are properly applied.
"It would be foolish to have a wheel excavator work in hard digging applications with rocky material over long periods of time and expect its O&O costs to be that of a crawler machine," Jacobson elaborates. "This is not what the wheel machine was designed and built for.
"On the other hand, it would not be very efficient to have a crawler excavator run around on a large jobsite and perform small or emergency jobs all over (e.g., cleaning under a conveyor belt). Its O&O costs would go up drastically," he says. "Applied more or less correctly, the cost of O&O should be comparable."
Metzgar asserts the O&O costs are actually lower with rubber-tire models. "Owning and operating costs over time will be less with a wheel excavator," he says. "There is no undercarriage maintenance, which reduces operating costs."
Gorski at K-Five Construction notes, "We put more maintenance into our Gradalls for two reasons: They are an on-road vehicle, and for us, they are high-production units, so downtime is not an option. For our operation, when you get into owning and operating and your cost per hour, the Gradalls are less expensive because of higher utilization."
Performance characteristics
Because of the similarity in upperstructure designs, the basic performance characteristics between wheel and track machines also tend to be fairly comparable.
Because the upperstructure is lower to the ground, track excavators may offer more digging depth, says Thomas. "The track operator has better visibility without a steering wheel on the self-propelled excavators," he adds.
Stability of a wheel excavator may also be a factor if stabilizers are not in use. "Track machines have more breakout force and lifting power because they have more stability through the track," says Metzgar.
However, wheel models can offer a smaller overall footprint, making them well suited for urban areas. "The footprint is nice and compact, so they work in a little tighter environment," says Fouty at Archer Western. "They have a little narrower swing radius."
This was crucial on the Valley Metro Rail Line project. "We had to maintain vehicle and pedestrian traffic on the streets we were working on," Fouty says. "Having a little tighter swing radius made it a lot more practical to use."
Yet, some lift capacity may be sacrificed, depending on the model. "For the same horsepower, you don't get quite the lift capacity as you do on a track machine, just because of the stability of the unit," says Fouty.
But once outriggers are applied, it's another story. "When the wheel excavator is equipped with outriggers, it can lift as much as the next size larger track excavator," Cremeens states.
Jacobson agrees, adding, "Once the machine is stabilized on four outriggers... its lift capacity, especially over the side or 360°, may outdo the crawler machine - a big advantage in tight situations."
Overall, the differences between wheel and track models are minimal. "There are more similarities than differences with regard to performance between Caterpillar's wheel and track excavators," says Cremeens. "They both accomplish hammer, dig, trench and truck loading [functions] with comparable performance. The difference is that the track machine is right at home on a steep incline or in soft underfoot conditions.
"A good rule of thumb," he continues, "is if you would take your BHL (backhoe-loader) on the site, you can take your wheel excavator. If flotation or steep inclines are present, a track excavator may be a better choice."
Project-specific needs
Ultimately, the decision to use a wheel excavator comes down to the particular circumstances on the project.
For example, Fouty cites a tight urban environment where equipment must be removed each night. "Just think about if you had to move all your equipment back to a yard every night and get it off the street. With a tracked excavator, that would be a huge burden - in the morning to get it out to the job, and at the end of the shift to get it off the street and back to the yard," he points out. A wheel excavator eliminates this burden. "Mobility is a pretty big factor with these things."
For K-Five Construction, the choice boils down to which machine can be most productive and cost effective for a specific task. "Everything is about production - how quick can it get done... and what is an inexpensive route to get there," Gorski comments.
"If you have a tracked excavator on site moving large amounts of dirt or material, it will outperform our Gradalls hands down," he admits. "But when you need to have the ability to go from job A to B to C in one day and maybe do some light excavation, some curb removal, light concrete or asphalt pavement removal or grading of ditches, then your tracked excavator can't compare."