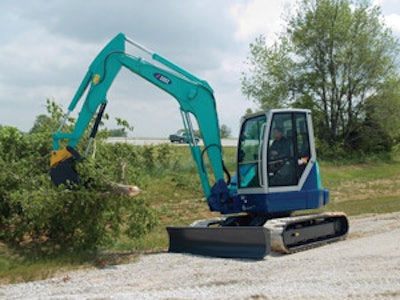
The versatility of compact excavators makes them a boon to many jobsites. With a quick switch between attachments, your customers can break concrete, load the demoed remains into a truck and grade the cleared site - all with the same machine.
"If a contractor determines he can do all these tasks with a single piece of equipment, that's pretty alluring," says Tom Connor, compact excavator product specialist at Bobcat.
In that sense, these smaller machines are more adept at multi-tasking than their big brothers. "I just don't see the same attachment utilization on larger excavators. Many times with larger excavators, attachments are dedicated, and even hard-plumbed. They do only one task for a given job, season or even lifetime. But with the compact sizes, contractors push the limit on attachments because it pushes the utilization of the machine."
But pushing the limits can create situations where these smaller carriers are asked to do too much. While you will want to make the best use of available power, you need to do so within the confines of the machine's specifications to prevent overloading, which can cause overheating and excessive and premature wear, as well as compromise stability.
Determine lift capacity
Bill Gearhart, assistant marketing manager/product manager at Yanmar, suggests you start by determining just how much your machine can lift. Some manufacturers print lifting limits on decals affixed directly to the machine. You can also find them printed in most product literature and owners' manuals.
Explain to customers that lift capacity will decrease as the boom extends. "If you're operating close to the machine, lift capacity will be greater," Gearhart says. "But as you extend the arm out to the side and up, the ability of the load to tip the machine will be greater."
Kendall Aldridge, national sales manager for IHI/Compact Excavator Sales LLC, suggests, "The contractor should always consult with the company they are renting or buying the [machine] from before using the unit in a lifting application," he says. "IHI's rated loads for lifting do not exceed 87 percent of hydraulic capacity or 75 percent of stability. The rated loads are on the conservative side to assure contractor safety."
Also, when choosing and using an attachment such as a bucket, consider the weight of the material your customer is working in, rather than strictly the volume that needs to be moved, adds Mike Conley, product manager, compact excavators at Komatsu. "There's a dramatic weight difference between a full bucket of cotton balls and a full bucket of wet clay," he says.
"It can be a challenge to know what a machine can handle," he continues. "There are a lot of factors that go into it."
Conley suggests reviewing the hydraulic capacity - flow and pressure - of the machine, especially when using attachments with high flow requirements, such as augers and breakers. "If it's a hydraulically driven attachment, you'll want to look at hydraulic flow capabilities of the machine and the requirements of the attachment," he says. "Mounting an attachment that's too large can cause it to overheat, which can be more of a concern with these compact machines because they have a limited reservoir for hydraulic fluid."
Mike Ross, Takeuchi, notes additional considerations in regards to tank size, as well as material. "The larger the hydraulic tank, the fewer the number of cycles the oil has to go through," he says. "The more times you cycle oil through the tank, the more wear and tear you put on the oil, the faster it breaks down and the more heat you create."
Ross adds that a steel tank can be a benefit to the cooling process because it disperses heat faster than one made from plastic. "Cooler oil won't put as much stress on pumps, valves, etc.," he says. "High-temperature hydraulic oil is definitely an enemy to pump life. If you can keep the oil at an even temperature, you'll find that your hydraulic pumps have a much longer life, and you won't have to change the oil as frequently."
In the area of hydraulics, Ross also points out when using an attachment such as a hydraulic hammer, its best performance will be achieved with one-way hydraulic flow.
"Most machines will come standard with two-way flow to use with attachments such as hydraulic thumbs so you can open and close them," he says. "But a hammer builds up pressure until it fires, then it repeats the process. The best way to utilize this type of attachment is with one-way flow so the pressure line fires the hammer, and the other line takes the oil straight back to the tank instead of going through the valve bank. While you can run it in two-way flow, it creates a lot more heat in the oil, and these hammers create a lot of heat anyway because they're building pressure and firing several hundred times a minute."
Optimizing hydraulic flow
A compact excavator is a hydraulically driven machine, as compared to a backhoe-loader, which is horsepower driven. But you will still want to ensure that the engine in your machine has enough horsepower to adequately power the hydraulic pump.
In some cases, manufacturers have introduced new models with smaller engines than the models they replace, although Gearhart emphasizes the smaller engines shouldn't necessarily be of concern. "We work to match the lowest horsepower possible to the hydraulic system," he states. "The pump will only have so much capacity for volume and pressure. Putting in a larger engine than is needed only makes more noise and burns a lot more fuel. We work to size the engine horsepower and the hydraulic system for each other."
According to Connor, it's important to consider the correlation between hydraulic flow and pressure when determining if an engine is of adequate size. "It's difficult to know exactly what you get out of a system," he says. "The key is to know how well flow is maintained under load. You can create hydraulic flow with very little horsepower. But when you start to run attachments that have resistance, like augers and breakers and even buckets for digging, the function begins to slow down if you can't maintain that flow."
For this reason, Connor maintains that Bobcat compact excavators traditionally have higher horsepower engines to maintain flow at higher pressures. He offers the following example of two pickups pulling a trailer down the road. "The difference between the two shows up when you load the trailer," he says. "You need more horsepower to pull more weight. The same theory applies to pushing oil out to the cylinders for digging when using an attachment. A torque limiting system comes into play for anything you do with an excavator. It actually destrokes the pump so the flow declines before you load the engine or before you pull the engine down.
"In a nutshell," he summarizes, "the more engine horsepower you have, the higher auxiliary flow loads you should be able to carry."
Ensure adequate stability
While you may be tempted to oversize an attachment to speed productivity, in the end this could not only increase wear, but it might also compromise stability.
In the case of a bucket, Conley notes that upsizing too dramatically can warp the dipper arm and cause the machine to become unstable, especially when working off to the side. "It may work now, but down the road you could have problems," he says. "The long-term consequences could be sacrificed wear."
Stability tends to be a greater concern on these compact machines because some of them have especially narrow tracks - less than 3 ft. wide in some cases - for maneuvering in confined areas. "On our smallest machine, width is less than 3 ft. so it can go through a doorway or narrow passage," says Gearhart. "Once to the jobsite, you can expand them for stability."
Ross indicates that a dozer blade, which is standard on most manufacturers' compact sizes, adds stability by acting as an outrigger. "We find that when contractors are craning heavy material, they can keep the blade in front of them and dig it into the ground, which is the best load lifting position for this type of machine," he says. "It allows them to crane more weight."
Ross offers this example: With the blade up, a 17,000-lb. TB175 can lift about 1,800 lbs. at roughly 20 ft. from the center of the machine and at a height of about 1 meter. If the blade is down, it can lift almost double the weight - about 3,500 lbs.
"If you're not well-balanced, it can become a safety issue," Ross says. "By design, the machines are much more stable when you have the hoe, or bucket, portion of the machine over the front or back so you're either over the blade or the blade is directly behind you. Those are the two most stable positions.
"When you swing over the side, the excavator will become less stable and you will want to bring the load in closer to the machine if it becomes tippy," he continues. "Also, contractors who are likely to swing loads 360 degrees will find that an excavator with a heavy-duty counterweight is much more stable when swinging loads over the side of the machine in comparison to excavators that are not equipped with a good counterweight."