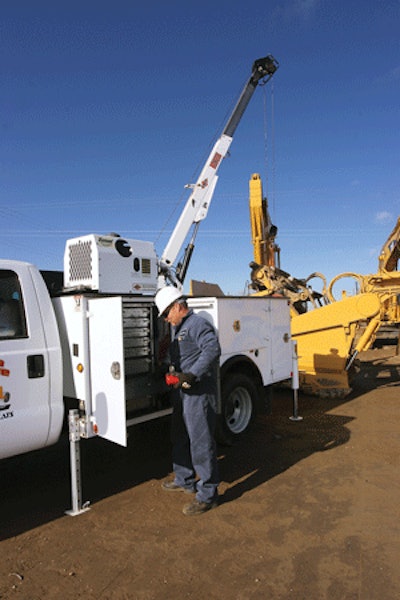
Mechanics trucks are mobile shops on wheels. The larger the truck, the better equipped your shop will be.
"I liken it to a house," says Jason Ollerich, vice president, Feterl Mfg. "No matter how big your house is, you always fill it full of stuff. So what it comes down to is figuring out what you really need on a daily basis - the tools you are carrying or the spare parts." Then factor in the load carrying capacity required. "Are you frequently pulling a component and having to transport it somewhere?"
Obviously, larger trucks cost more money. "You have to balance a truck that is large enough to meet the needs and small enough to be affordable," says Tim Worman, product manager for commercial vehicles, Iowa Mold Tooling Co. Inc. (IMT). "To me, it is more important to have a truck that meets your needs. If you don't, your affordability went out the window because your cost of doing business is impacted. Your utilization costs are impacted."
There are many examples where a contractor purchased a truck based purely on price and it didn't work, says Worman. In such cases, he adds, "You better not have high expectations of what you can do with it."
Size matters
Tough decisions are necessary when sizing the vehicle for your operation. "It is really a matter of what do you need every day vs. what would you like to have," says Ollerich. "What is a necessity, what would be nice and what is just kind of a luxury item?"
The size of truck will dictate what you can accommodate. However, there are a few downsides to a larger truck besides the initial purchase price. "Not only does the cost of the truck go up, but with $3/gal. diesel, that is another consideration," says Ollerich. "Some of our customers, when they travel between jobsites, they may be 200 miles apart."
Yet, small GVWs create limitations. "With smaller units, some of the compromises you have would be limitations on what you can carry back to the shop, and what tools and optional equipment you could have on your unit," says Gary Hibma, national sales manager/Western region, Maintainer Corp. of Iowa Inc. "This also limits the size of crane you can mount on the truck, which limits what a heavy equipment mechanic can accomplish on a jobsite."
It all revolves around the intended payload. "I tell operators to look at the weight of their heaviest normal load and build their mechanics trucks around those components," says Tim Davison, product manager for bodies and cranes, Stellar Industries. "The worst thing is when a field mechanic has an undersized crane and truck to do his job. The whole idea behind a field mechanics truck is to perform a majority of his work in the field. Having a correctly spec'd truck is crucial to his performance and efficiency."
"The payload you want to carry will dictate the size of your chassis," says Worman. Another important consideration is CDL requirements. There has been a progression away from Class 5 trucks toward the 26,000-lb. CDL limit. "Everything is getting bigger. I see a trend for 14- and 19-ft. bodies."
It's also important to consider maintenance costs. "The cost of maintaining a larger truck is less than a smaller unit," says Hibma.
This is due to the greater wear and tear on the smaller Class V chassis. "You chew up drivetrains, you chew up brakes, you beat up transmissions - just because you are trying to do the heavy-duty work of a truck in that lighter vehicle," says Worman.
Resale is also better on larger trucks. "The value of a 26,000-lb. GVW truck with a service body is higher than a 19,000-lb. GVW truck," says Worman. "There is more of a secondary market for the larger truck."
Select the right wheelbase
Wheelbase has a great impact on weight distribution.
"Really, it's maneuverability vs. compartment storage," says Davison. "Is a shorter wheelbase for increased maneuverability, or a longer wheelbase for better weight distribution, more desirable? [Operators] who have longer drives tend to need more storage. Most mechanics like a shorter wheelbase for maneuverability. This also decreases the chances of overloading the front axle."
Carefully consider the trade-offs. "A shorter wheelbase does increase mobility, but limits your weight distribution because you will have more weight on your rear axle," says Hibma. "A longer wheelbase will give you better weight distribution." He adds that certain chassis now offer a tighter turning radius, making maneuverability less of an issue.
To choose the appropriate wheelbase, you need to be realistic about the weight you intend to carry. "I will sit here and do a weight distribution every day of the week and tell someone what his available payload is," says Worman. "He will overload it every time - more tools, more parts. We make sure when it leaves that it is a legal truck and we tell them what they can haul in it (the payload)."
Sticking with standard cab-to-axle lengths such as 84, 108 or 120 in. can save money up front, since custom wheelbases, such as 88 or 110 in., will cost more. In addition, make sure the wheelbase is appropriate to achieve a legal weight distribution and meet your objectives.
"If you have to move an axle after you have the chassis, you are looking at $1,500 to $1,800, depending upon the shop and the region," says Worman. "You want to make sure you get it right the first time."
Don't sacrifice strength
The more weight you can take out of a body, the more payload capacity is available. But be cautious about how you achieve the weight savings. "It really comes down to cost vs. durability vs. weight," says Ollerich. Unfortunately, you can't have it all. "I always say durability, weight and low cost - pick two."
With service bodies, durability should be a priority. "Weight is important, but not at the risk of decreased durability," says Davison. "To decrease weight properly, a great deal of engineering has to be done to maintain or increase durability."
IMT, for example, uses high-tech design tools to optimize weight while maintaining overall strength. "We put it through our virtual engineering and finite element analysis to see where we can take material out and where it has to be," says Worman.
Be cautious of lightweight materials, such as aluminum. "Using lightweight material on the bodies decreases durability," says Hibma. "You need to be careful of substituting light weight for durability, especially with the substructure."
Get the right crane
Make sure the crane capacity matches both the truck's capacity and your needs.
"The real capacity of the crane is in the ft.-lb. rating, not its maximum capacity," says Davison. The ft.-lb. rating is a calculation of the load lifted multiplied by the distance from the center line of the crane's point of rotation. "A 55,000-ft.-lb. crane can pick up 10,000 lbs. at 5.5 ft. from center line rotation. Some manufacturers like to play games with the maximum capacity of their cranes, while offering the same or less ft.-lb. rating than other manufacturers."
Don't get caught up in the ratings confusion. "No matter what the crane is called or what it is named, you need to look at the ft.-lb. rating," says Ollerich. "You can have a 6,000-lb. crane rated at 30,000 ft.-lbs. or a 6,000-lb. crane rated at 40,000 ft.-lbs. That 40,000-ft.-lb. crane is going to be much more capable."
To choose the correct crane, calculate the load you want to lift and multiply it times the distance from the crane. For example, if you want to lift a 4,000-lb. load at a distance of 11 ft., it would require at least a 44,000-ft.-lb. crane.
"If you are interested in a certain manufacturer's product, look at the load chart," says Ollerich. "Make sure you pick a crane that is going to do what you want."
Worman recommends sizing the crane to 80% of your worst-case scenario - in other words, the heaviest component you would ever try to lift.
The weight of the truck also comes into play. "Do not get more crane than the truck can handle," advises Hibma.
The more a truck weighs, the more it can safely lift. "The main science of the stability of the truck is what it weighs at the time you are doing the lift," Ollerich explains. "We are always super conservative." Feterl actually calculates stability with an empty body mounted on a truck, which is a worst-case scenario.
Customize a Solution Price Backhoe Service, Science Hill, KY, performs horizontal boring operations, drilling holes under roads for sewer, water and gas lines. Six service trucks support its operations. Four of the trucks are T300 Kenworths - three with 11-ft. bodies and one with a 14-ft. body. Two Peterbilt 379 models have 18-ft. Stellar bodies. The contractor uses the trucks to transport its crew, the boring machines on trailers and all of the supporting tools and accessories to the jobsite. "The size of the bores that the crew does has to be calculated into the size truck we need," says Gary Price, owner. "The bigger the bore, the bigger the stuff you need, and the more tools you have to be able to carry." The trucks see a lot of use. "Every Monday morning, one of those trucks goes to one of our jobs," says Price. "We work Kentucky, Indiana and Tennessee mainly. We sometimes go to Georgia." Each vehicle will typically run at the maximum legal weight capacity. "When I get one of those boring machines behind it, I'm pushing 80,000 lbs.," Price points out. A 10,000-lb. crane is used to lift the boring head onto the truck or trailer. "All of the big stuff is lifted with the excavator." The trucks carry everything needed to complete the job. "These bodies have three sets of toolboxes in them, plus two sets of bolt bins," says Price. They are also equipped with hydraulic-driven air compressors, two Miller welders per truck, four oxygen acetylene bottles and an oxygen/acetylene hose reel. These are not standard service bodies. "They are basically custom built," says Price. He didn't want the front stabilizers on the body. "So I shortened that wheelbase so the bed would come forward and you would not have that big gap between the body and the bed. The shorter you can get the truck, the more maneuverable it is." Price also changed the layout and height of the compartments to match his application. The height of the compartments on the back of the body was lowered to accommodate the welders mounted on top. This allows the operators easy access to the welders. "The front half of the bed is covered with a sliding cover," Price adds. "Inside of that, we have 100-gal. diesel fuel tanks. They are plumbed over to the oxygen/acetylene compartment with an automatic nozzle. All you have to do is flip a switch and fill up whatever you want with fuel." To accommodate large loads, Price increased the size of the latest two service trucks added to the fleet. "The newest ones are 18 ft. I did it for capacity," he states. The bodies are mounted to tandem-axle Peterbilt 379 short-hood models with 470-hp Caterpillar engines and 18-speed transmissions. They are also equipped with air ride. Price has evolved the specs for his service trucks over the years. "The main thing is to spec it to what you need," he says. Take time to figure out your requirements, he advises, and don't settle for anything less just because someone says it can't be done. "There are people who will work with you, and there are people who will say you can't do this and you can't do that. Find the people who will do it." |