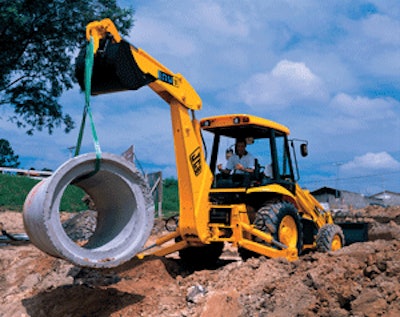
Excavators and backhoe-loaders spend the vast majority of their time digging and loading dirt or powering attachments. But they can also be periodically called upon to lift and place pipe, trench boxes and other materials into a hole or trench, or move them from one area of a jobsite to another.
Although on the surface this may seem to be a simple "lift and place" scenario, it actually requires some careful planning to ensure the safety of your employees and your equipment. Failing to follow proper protocol, as outlined in the equipment operator's manual, can have devastating results.
The risks of overloading
Prior to any lift, it's vital that you know the weight of the material to be moved.
"An educated operator should not take a guess as to what he's doing," says Paul Golevicz, marketing manager, Kobelco Construction. "He should contact the right individuals on site to find out what the material or object weighs."
When assessing the total weight of the load, be sure to include the weight of the bucket or quick coupler if they will remain on the machine. "The weight of the bucket or coupler has to be subtracted from the total weight that we say the unit can lift at that particular reach or angle," says Golevicz. "A lot of people don't do that, and they end up overloading the equipment."
This can have significant repercussions. "The most serious potential outcome in exceeding a machine's rated lift capacity is tipping the machine," says Bret Jacobson, product specialist, excavators, Liebherr Construction Equipment Co. This can place the operator and any workers nearby or in the trench at risk.
"Exceeding the rated lift capacity of the machine will also result in a decreased service life of the machine," he continues, "especially the load bearing steel structures of the attachment and the swing ring support."
There is the risk of overheating the hydraulic system, which can result in a blown valve, hose or other damage.
"You have multiple lift cylinders, too, and you could end up ruining seals and other components on the unit if it's grossly overloaded," Golevicz states.
In addition, there is the potential to bend the boom, arm or other costly components.
Know your equipment's limits
Both excavators and backhoe-loaders come with published load charts, which can be found in the operator's manual and may be mounted in the cab. Manufacturers can't emphasize enough the importance of staying within these established ratings.
Admittedly, the ratings tend to be on the conservative side. However, engineers do this for a reason, says Golevicz. "There is some overloading capability, because they know the operators will indeed overload a machine," he explains. Without these limits, he adds, "your operator would always be lifting up to the max rating - and beyond."
Continually pushing the excavator above and beyond its ratings presents several risk, says Eric Winkler, marketing manager, backhoe-loaders, New Holland Construction. "You could have hoses or a cylinder go, you could have a boom break, etc.," he points out. "That's why we make sure we have all of our load charts specific to what the machine can do so people aren't trying to pick up 15,000 lbs. when it's only going to pick up 8,000 lbs. We go above and beyond in making specifications a big portion of it."
Of course, when determining whether a particular machine can handle a lift, the operator must factor in more than total lift capacity.
Take excavators, for example. "Load charts are available for excavators. But the contractor must also be aware of the configuration of their machines - short, standard or long arm - to make sure they are reading the correct lifting chart," says Chad Ellis, product and training manager, Doosan Infracore America.
Also consider how far the excavator will need to boom out. "If you're lifting a 10,000-lb. trench box or pipe and you're doing it out at 20 ft., you need to consult the operator's manual to see if the excavator can handle it," says Golevicz.
The equipment must also be able to safely lower the load. "The biggest risk associated with using a hydraulic excavator to lift and place loads is tipping of the machine as the load is lowered into place," says Jacobson. "This is because the lifting capacity at a given radius from the centerline of the machine usually decreases as the attachment is lowered, due to attachment geometry."
With a backhoe-loader, the position of the lifting object is also an issue. "When lifting a load with a backhoe, the machine will lift more straight out the back than it will over the side," notes Jim Blower, mid-range product marketing manager, JCB Inc. "The operator needs to know the weight limits of the machine in its worst case."
Maintain for safety
Proper servicing of the equipment can significantly enhance its ability to safely handle lifting applications.
Winkler cites the following example: "Let's say [a backhoe-loader] operator is using an extendable dipper. It has a lot of 'play' and is real sloppy because it hasn't been serviced for a long time. He makes a slight movement and the next thing you know, it's rattling back and forth. That could cause a danger for the guy in the hole."
In addition to standard service items, hydraulic system components - such as the swing system and hydraulic lifting system on an excavator - need to be properly lubricated according to manufacturer recommendations. "Otherwise, the bushings will start wearing and you will develop friction inside the bushings," Golevicz explains. "That can in turn lead to failure of the actual bushing. When you're spending $200,000 to $400,000 on a piece of equipment, it really pays to do the routine maintenance and greasing."
For backhoe-loaders, proper tire pressure is also important. "If you have a bulge or something on your tire, and you're lifting up a few thousand pounds and trying to place it, you don't want a tire going out at that point," says Winkler.
This is where the daily walkaround inspection can make a big difference. "It's very important for an operator to do his daily inspection," says Winkler. "Do a quick walkaround and look at whether the tire pressure is in line, is there anything leaking under the machine - all those things you should do when you first see that unit in the morning. Then maybe check it again after lunch just to make sure."
Checking hydraulic lines is particularly critical. "The condition of main hydraulic hoses should be inspected daily on machines in constant piping or lifting applications," Ellis stresses.
The few minutes it takes to do the inspection can mean the difference between a safe lift and a potentially hazardous one. "You don't want your [co-worker] to end up with 2,000 lbs. in his lap," Winkler comments. "So do your due diligence around the machine to make sure everything is set."
Machine Features Help to Carry the Load First off, double check the load charts. "Make sure you know what that machine can do before you purchase or rent it to be sure it actually fits the applications that you have," advises Eric Winkler, New Holland Construction. "You don't want to get something that isn't going to fulfill your needs, or maybe your future needs." Next, take a look at other features that can affect operating performance during a lift. For example, with excavators, pay special attention to drawbar pull force and swing torque. "Some machines do not have the hydraulic capability," states Paul Golevicz, Kobelco Construction. "Either the total capability or efficiency of the hydraulic system may not allow them to travel and swing with a heavy load at the same time." Larger excavators may also offer independent travel. For example, on Kobelco and New Holland models, the units are equipped with two hydraulic pumps - one dedicated to the uppercarriage and one dedicated to the travel system (tracks), Golevicz explains. "When you separate the two, you're able to travel and carry a load at a constant speed," he points out. For added safety, Bret Jacobson, Liebherr Construction Equipment, advises, "The machine should also be equipped with load holding valves for the boom hoist cylinders that will prevent the attachment from falling if a hydraulic hose were to burst. Other equipment that can ensure safe lifting are items such as a heavy counterweight, swing holding brake and overload warning device." An overload warning device warns the operator both optically and acoustically when the load limit has been reached, Jacobson points out. Such a device is available as an option for all Liebherr hydraulic excavators. Regardless of machine type, take a look at the cab and control systems. "A machine with great visibility and smooth controls are a 'must' for pipe and lifting jobs," says Chad Ellis, Doosan Infracore America. Pilot joystick controls are pretty much standard on today's hydraulic excavators. However, only in recent years have they become prevalent on backhoe-loaders. One advantage is more precise, controlled movements of the backhoe - a benefit when lifting and maneuvering heavy loads. The controls may also incorporate other electronic functions, such as the push-button extendable dipperstick found on New Holland machines. When the button is fully depressed, the dipperstick extends quickly. When depressed slightly, the dipperstick "inches" out slowly, allowing for more precise work. JCB has taken this a step further with its backhoe-loaders. Its units are fitted with standard HSC (Hydraulic Speed Control), which is operated via a switch inside the operator's compartment. According to Jim Blower, this feature allows the operator to select and slow the hydraulics down, then slowly move the backhoe and position the load where it's needed. "This prevents the load swinging around in the vicinity of personnel," he adds. |
Tips for Safe, Efficient Lifts "Principally, a hydraulic excavator is one of the most stable machines that can be used for lifting," states Bret Jacobson, Liebherr Construction Equipment Co. "Provided certain safety guidelines are followed, risk factors and wear and tear on the machine can be reduced." Following are some suggestions to maximize safety when using a hydraulic excavator or backhoe-loader for lifting applications. For specific guidelines, consult the operator's manual for your particular equipment. Prior to the lift - Verify the weight of the object to be lifted and compare it to the load lift charts supplied with the equipment. Be sure to include the weight of the bucket or quick coupler if they are to be left on the machine. - Use only certified lifting slings, nylon straps, chains, etc. Verify that they are rated to the weight of the load and are in good condition. They should be attached only to manufacturer- designated lifting points on the bucket load hook, quick-coupler load hook or other approved lifting device, such as a dedicated crane hook. - The machine should be placed on firm, level ground as close to the load as possible, since lift capacities are at their highest point closest to the machine. Any outriggers or other stabilizers should be lowered prior to lifting. - Ensure the operator will be able to maintain visibility into the hole or trench as the load is being lowered. Position the machine so that lowering is done over the end of the machine and not over the side. During the lift - Ensure controls are correctly adjusted to the operator's preference (i.e., SAE or ISO). - Ensure the appropriate spotters are in place to assist with the lift. The operator should be able to maintain visibility to the spotters at all times, and know and understand the hand signals to be used. - The load should be lifted very slowly and kept as close to the ground as possible at all times. - If the operator notes any sign of instability in the machine or the load, the lift should be discontinued immediately and the load lowered to the ground. |