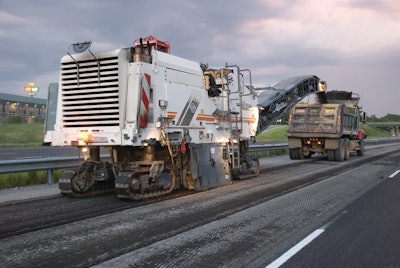
A fleet of five Wirtgen cold mills was the key in June 2010 to high production on a mill-and-fill project on heavily traveled I-75 south of Valdosta, GA, near the Florida line.
There, the volume of milling - approximately 155,000 tons - was such that reclaimed asphalt pavement (RAP) from this project was going right back into the mix being used for resurfacing.
"We're putting the same RAP from this project back into the mix," said Mike Fisher, general manager, The Scruggs Company, Valdosta, GA. "Some of this RAP tonight may end up in the mix tomorrow night."
Testing was a major element in the ability to reuse the RAP on the same job. "We came out and milled a section of road before the project kicked off, and tested the RAP for our mix designs," Fisher said. "So once we got going on the project we were able to recycle it almost immediately back on the job."
"The DOT gets a big bonus out of that," said Ferrell Scruggs Jr., president of The Scruggs Company. "We've put a big RAP credit into the project and the DOT gets a true, true savings by reuse of the existing mix on the ground, which still has a 5.5% liquid asphalt content after two decades."
Joint venture for I-75
On I-75, a joint venture of The Scruggs Company, Valdosta, GA, and Reames & Son Construction Co., also of Valdosta, milled and paved 17.25 miles of I-75, three lanes each way. In one pass, the mills were removing 2 3/4-inch raveling, deteriorated pavement two decades old, a total of some 77,500 tons each direction.
The milled course was replaced with 2 inches of a stone matrix asphalt (SMA) intermediate course, with a maximum allowed void spec at 7%, but Scruggs set a goal at 5%, followed by a 1 1/4-inch lift of porous European mix (PEM), a open graded mix with around 6.1% liquid asphalt binder and 0.4% fiber. RAP was allowed only in the SMA mix, at a rate of 10%.
The PEM binder is typically polymer modified, but the I-75 job had the option to be polymer modified or crumb rubber modified, the latter of which was the contractor's option. PEM is designed to contain about 20% air voids to make it very porous, and it serves as an open graded friction course, reducing tire spray, enhancing drainage and attenuating noise.
The project was funded under the American Recovery and Reinvestment Act of 2009.
"Between we two contractors, we are running five milling machines, with one spare," Scruggs said. On the southbound lane, milling was subcontracted by Scruggs to Oxford Construction Company, Albany, GA, which was running two Wirtgen mills, a W 2100 doing main line, and a W 2000 doing a 5-foot shoulder cut. Scruggs also was running its W 2000 in the mainline cut in the southbound lanes.
On the northbound cut, milling was being undertaken by Pavement Products & Services, Inc., of Piedmont, S.C. as a subcontractor to Reames & Son. It was using one W 2200 with full-lane head, and one W 2000.
Constraints of time
All four contractors were laboring under the pressure of time constraints. "The project has a lot of pressure in it, because of the restraints on the time we can work," Scruggs said. "We have to have the milling and paving done within the time limits of the contract. Once we mill out a section, we cannot allow traffic on it until it's been paved back."
Safety issues posed by the 2 3/4 inch drop-off between lanes is the reason that traffic is not allowed on the milled areas, Scruggs said. "From that standpoint, we have to have quality equipment out here, especially the milling machines. The pavers, plant and trucks all have to be at 100%," he said.
The joint venture, though, means that back-up mills and even plants can be utilized in case of a breakdown. "If our plant goes down, and we can't get it back up, instead of paying liquidated damages the other contractor can help us meet our needs," Scruggs said. The joint venture was subject to a $2,000 per hour penalty for failure to reopen on time.
"This big production milling is a little bit out of the norm for us, so that's why we are relying on subs for this work," Fisher said. "We are time-constrained by a certain window, having to work from 7 p.m. to 7 a.m. to mill and inlay in one night. That's why we had to hire production machines, to get in the cut and get out of the way."
Milling production was averaging about 11,000 feet per night, but the volume of milling was limited by the progress of paving and the ability to get hot mix asphalt to the job. Milling would begin by 7:30 p.m. and paving would commence about 45 minutes to an hour later.
"We like to have the last truck leave the plant about 5 a.m. and be here by 5:30, with everything completed by quarter to six," Scruggs said. "We have to have everything up, the job secure with all equipment off and traffic back on the road with striping and raised pavement markers by 7 a.m."
The Scruggs Company is a heavy/highway contractor which does grading and both hot mix asphalt paving and concrete slipform paving. While Oxford was working as a sub to Scruggs, it also is a large milling contractor in its own right, said Chris Turner, milling supervisor for Oxford Construction Co., Albany, GA