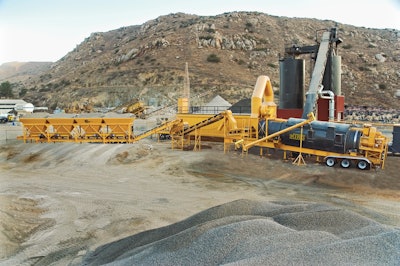
When Jason Papich acquired a 180 ton-per-hour (tph) CEI Rap King asphalt plant in 2009, he knew it was a necessary investment to support his company’s rapid-growing paving operation. Papich, owner and president of Papich Construction Co. Inc. of Grover Beach, CA, says he could no longer rely on area producers to meet the quantity and quality demands of projects his company is constructing.
Papich Construction is a professional general engineering contractor specializing in civil construction. It was established in 1997 by Jason Papich, who wanted to continue the quality construction legacy of his father, Bill.
“My father operated his own (construction) company from 1978 until 1995,” Papich notes. “In 1997, I decided to start my own company in an effort to provide the same type of quality service my father provided for so many years.”
Today, the Southern California company’s earthwork services include excavation, building pad grading, road building, trenching and demolition, as well as underground utility work.
“We began providing asphalt services in 2004-2005 and ever since then we have been growing that part of our business,” Papich says.
Of the company’s approximate $50 million in annual revenue, $30 million is tied to asphalt construction work, keeping two paving crews busy 10 months a year.
Time to buy a plant
With the amount of California Department of Transportation (Caltrans) state highway projects the company has been pursuing and awarded, Papich realized he needed his own production facility.
“The area we serve really didn’t have many asphalt sources for us to buy from, and the changing (asphalt mix) specifications required by Caltrans required more QC/QA control that we could not provide by purchasing mix from other producers,” Papich says. “There really is too much at stake with incentives and penalties tied to state projects. Most of the state projects we work on have bonus money tied to the quality of the mix and how it performs, and we simply could not leave that up to an outside source.
“Also, the two other production facilities in our market area just didn’t have the current technology to produce RAP (reclaimed asphalt pavement) and warm-mix designs,” Papich adds. “And, we knew that in order to be competitive we had to operate our own production facility.”
When Papich did purchase his own plant in 2009, his market was struggling, like the rest of the construction industry that was just trying to survive the economic recession.
It was very competitive, with contractors submitting low bids just to get the work, according to Papich. Trying to compete in that type of environment, when you’re paying a higher price for asphalt from an independent producer, is difficult. Located approximately 80 miles north of Santa Barbara, Papich Construction performs a bulk of its services within 60 miles of its Grover Beach headquarters.
“If you’re trying to win a bid in a competitive market and you have to pay $10 more a ton than what it would cost to produce at your own plant, it’s pretty hard to make much of profit in that situation,” Papich says. “So even in a tough economy, it just made sense to own and operate a plant.”
Papich’s RAP King plant
Papich Construction’s RAP King drum mixer from CEI uses a counterflow aggregate dryer surrounded by an outer mixing chamber. The design allows residual heat from the drying drum to be transferred outward to the mixing chamber. A substantial amount of the drying drum’s heat is transferred to the full length of the mixing chamber, providing enough heat to maintain a proper mixing temperature when cold RAP material is added to the outer mixing chamber. The technology is capable of producing mixes that include up to 50% RAP with no added fuel cost.
Since airflow through the RAP King drum mixer creates a strong induced draft in the mixing chamber, the steam and fumes released from the RAP material are incinerated in the combustion area as they are drawn out of the mixing chamber.
Along with the portable RAP King drum mixer system, Papich’s plant includes four 8 ft. by 12 ft. cold feed bins and a RAP bin. The cold feed bins are mounted on a chassis for easy portability and rapid setup. The unit includes an integral collecting conveyor that runs underneath the aggregate bins. The conveyor includes an inclined extension that can be folded into a retracted position for travel. Virgin aggregate is carried by the unit’s collecting conveyor to a scalping screen. The scalping screen is mounted on a separate incline conveyor that feeds the drum mixer. The conveyor also includes an integral scale to monitor flow of material to the mixer.
The separate RAP bin is mounted on its own portable chassis and includes an integral scalping screen and incline conveyor.
Other components Papich purchased include:
- A portable control house with programmable logic controller
- A portable 100-ton surge bin with drag-slat conveyor and batcher
- A portable baghouse with an inertial separator mounted at the baghouse inlet to remove the majority of the dust from the dryer prior to the filter bags
Plenty of work ahead
When Papich reflects on the decision to purchase his own plant, he couldn’t be more pleased.
“We currently have a 450,000 ton backlog of work we need to complete in the next three years, and we no longer have to worry about whether or not we can deliver product when we need to deliver it,” he notes. “We’ve been operating the plant at up to 220 tph, with 95% of our production being used to support our highway paving projects.”
As Caltrans continues to change its mix specifications to include more RAP content (currently, Caltrans allows up to 15% RAP), Papich says his CEI RAP King will accommodate any increase up to 50%.
The portable plant is currently set up at the Hanson Quarry in Santa Margarita, north of Grover Beach, but Papich likes the fact that it can be moved and operated on a 1-1/2 acre site whenever another project calls for its mobilization.
“We bid on $40-$50 million projects that can require up to 150,000 tons of asphalt, so this plant is ideal when we need to locate close to the work,” he says. “For the next two years we plan to stay at the Hanson Quarry to complete the contracts we currently have. Our arrangement with Hanson is that we purchase aggregate from them while we’re located at their facility. If we have to move the plant to accommodate another project, we would then purchase from the nearest aggregate supplier.”
For Papich Construction, investing in a portable state-of-the-art asphalt production facility at a time when many contractors were just trying to survive a tough economy was a decision that has and will continue to pay dividends.
“We know that the quality of the plant is there since CEI is an Astec company,” Papich states. “We also know the plant technology will allow us to produce a high-quality RAP mix design when Caltrans changes its mix specifications to allow more RAP, which will be good for our business and good for Caltrans. This investment will allow us to be competitive as we continue to build the asphalt side of our business.”