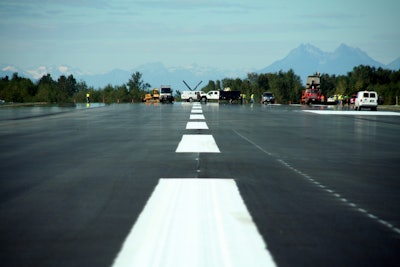
ICON Materials had its work cut out for it. The decades old runway surface at Bellingham International Airport (BLI), which is located three miles northwest of Bellingham, in Whatcom County, WA, was deteriorating due to poor subgrade soils, undrained and saturated subgrade, inconsistent original construction standards and a surface at least 20 years old.
Deterioration was accelerating due to increased MD 80 and Boeing 737 traffic introduced by regional carriers over the last five years. The existing runway also did not meet current FAA pavement profile standards. In addition, the main parallel taxiway, Alpha, was also being stressed by the new, heavier traffic and was only 60 feet wide.
The objective of the project was to bring the Runway 16-34 and Taxiway Alpha up to modern geometric and structural standards while widening the taxiway to 75 feet for its entire length of 6,700 feet.
Time crunch
ICON Materials worked at night while keeping the runway open, then it had a three-week window when the entire runway was closed for paving. In total, 107,000 tons of FAA P-403 bituminous base course using 30% reclaimed asphalt paving (RAP)and PG 64-22 asphalt binder and 66,000 tons of FAA P-401 bituminous surface course with PG 70-22 polymer modified asphalt binder were laid using Caterpillar 1055 pavers.
Other equipment used on the project included Hamm, Sakai and Ingersoll Rand double-drum vibratory rollers for the intermediate course and Hyster Hypac C560B pneumatic rollers for final compaction. A Roadtec 2500 Shuttle Buggy was also used.
The mill-and-fill and leveling lift paving for the runway was restricted to a five-hour work window (midnight to 5 a.m.) in July and a seven-hour window (10 p.m. to 5 am.) in August.
"ICON Materials aggressively used these allowed closure periods to pave as much as possible on the runway to 'push' paving tonnage out of the critical September timeframe," says Gary Babick, project superintendent. "Within these short time frames, the pavement needed to be milled, swept, tacked, paved, compacted and re-striped by 5 a.m., fully functional and available for a 5:20 a.m. scheduled flight every morning."
ICON Materials challenged its crews and critical subcontractors to become super efficient with time and coordination, says Babick.
"Paving started within minutes of the milling machine removing the existing pavement and milling/ paving were performed simultaneously to precise limits to allow for compaction and clean-up," says Babick. "George Reynolds, general paving foreman, and I developed a precise plan for each night and executed the plan under every circumstance, including late arriving planes, rain, equipment malfunctions etc. The morning commercial flight was never delayed during this two-month time frame."
Rainy weather
The final 70,000 tons was placed in a 255-hour window between September 1-22.
"Peak paving rates were 435 tons per hour mainly due to the fact that the P-401 surface course paving was difficult to compact and could only be placed during daylight due to temperature concerns related to compaction," says Babick.
The thicknesses of the asphalt varied from 5.5 inches thick on some pavement reconstruction sections to 4 inches on the major "mill and fill" surface replacement of the existing runway pavement to 2.5 inches in the top four lifts on the taxiways and runway. Most of the tonnage was placed at 2.5 inches compacted.
The major paving was performed using two pavers with material transfer devices working in echelon at 18.75 feet wide for each paver, resulting in 36-foot-wide paving passes after the joints were cut back, according to FAA specification, says Babick.
The main challenge was weather during the 255-hour closure, says Babick.
"The runway opening date for September 22 could not be delayed as the airlines relied on this date for operational and ticket sales purposes," he explains. "The first three weeks in September set records for rainfall for that period. ICON Materials was literally paving between rainstorms. Had it not been for the early decision to perform mill-and-fill paving during nights in July and August, the project could not have been completed on time."
The work at BLI began on April 27, and the project was substantially complete on October 14, 2010. Pavement grooving required a 30-day cure period for the new paved surface. Therefore, grooving was complete on October 28.
Complying with FAA specs
One tool ICON Materials used on the BLI project was its Paveset Grade Control System.
PaveSet is an electronic screed control computer from PaveSet America that has desired pavement elevations input into its memory in a grid determined by the contractor from the design drawings.
"ICON used an 18.75-foot by 25-foot grid pattern," says Babick. "Entering the existing elevations versus desired elevations can be done with a simple spreadsheet or can be input manually in the field."
The PaveSet control allows for the screed to place the pavement to the desired elevations including providing an allowance for uncompacted versus compacted hot mix. A PaveSet consultant can be employed for training and initial system set-up.
PaveSet is a "plug-and-play" system with robust components, says Babick. The system can be installed in minutes and can be adapted to any brand of screed control. It is plugged into the grade/ slope control valve of the paver with the computer "brain box" mounted at the back near the screed operator station.
During paving, the PaveSet system checks the screed elevation every 2.5 feet and makes adjustments accordingly. When used with a 20 foot ski, the result is a smooth "automatic" pavement surface, says Babick.
"PaveSet was used on all the critical paving passes to ensure compliance with FAA surface elevation specifications," he says. "The final surface elevations were 99+% within the FAA specification of not more than a 0.04 feet of variance from design elevations. 90+% of the survey certified elevations were with 0.02 feet of variance. One survey shot out of over 600 was out by 0.05 feet.
"This has been ICON's typical experience since replacing stingline systems with PaveSet in 2006," Babick continues. "This is the fifth runway/ taxiway paved by ICON using this system. PaveSet allows ICON to pave at full speed with assurance that we are paving the surface to exacting tolerances."
If the acceptance criteria for the pavement is the FAA "grade" specification, it is imperative PaveSet be used, explains Babick.
"Stringlines and slope control will not meet the FAA pavement grade spec," he says. "ICON prefers to input the elevations from points surveyed on the pavement for the last few lifts so that the paver operators can cross-check the screed controls constantly. This requires additional surveying, but is not strictly necessary for the use of PaveSet. "
As ICON chooses to input final elevations in the field, the survey crew must work in tandem with the paving crews.
"Everything we learned from the first runway we paved with PaveSet in 2006 has been used and refined in the five airport projects pavements we have constructed since 2006," says Babick. "We learned that the PaveSet system is stable, reliable and robust. If we set it up correctly, we can trust it and produce excellent results."