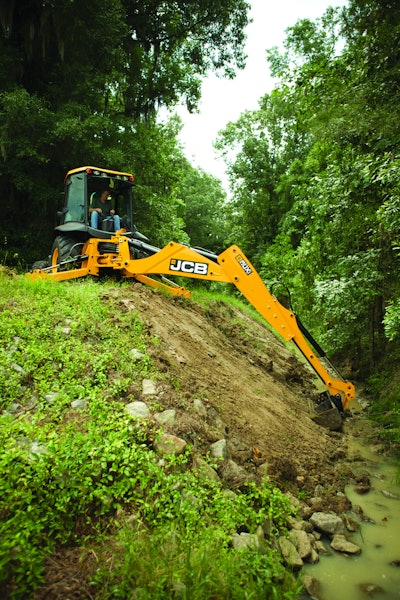
The extendible dipper stick can add 5% or more to the cost of a backhoe-loader. But it also extends machine reach, increasing the size of the workable trench. This allows you to dig a longer flat-bottom trench without having to reposition the machine, which improves productivity. It also allows the operator to place the spoil farther from the trench.
“Typically, extendible dippers add 3 to 4 ft. of reach,” says John Comrie, competency manager, utility products, Volvo Construction Equipment. “The extendible dipper will pay for itself in productivity gains, as the machine does not need to be moved as often when digging trenches or loading spoil/debris on truck beds.”
Jim Blower, senior product manager – mid-range, JCB, notes, “The greatest return is really in a trenching application. The biggest advantage is that you can set the machine up, reach farther out and dig along the trench from one position. The more time you spend moving the machine, the less time you spend digging. You just reduce the amount of machine movements and increase the amount of digging time.”
The extendible dipper stick also allows you to reach into areas inaccessible to a standard dipper. “In circumstances where dig depth changes, this dipper provides instant access to a deeper flat-bottom trench,” says Rob Marringa, marketing manager, Case Equipment. “In applications where the backhoe is being utilized as a lift and position tool, the extendible attribute increases control for finite positioning.”
There are as many answers as to what you can do with an extendible dipper as there are backhoe operators. The larger the percentage of the work you perform with the back end of the backhoe-loader, the easier it may be to justify the extendible dipper stick.
“Having a standard boom and dipper simply limits the scope of flexibility,” says Marringa. “In some cases, it may be necessary to bring in an additional machine that can serve the needs of the entire jobsite, thereby increasing costs of site work and delaying job completion.”
Weight considerations
Admittedly, an extendible dipper weighs more than a fixed dipper.
“Every machine is a little different, but it is about 500 lbs. extra that you carry on the back end,” says Blower. “When you add more weight to the back end of the machine, you have to make allowances for it by [adding] different counterweights on the front to balance it up again so when you are going down the road, you are not bouncing the front tires off the ground. Every time we build a machine, we balance it back up again.”
The extra weight can reduce lift capacity. “You are carrying that weight on the back, so you do reduce slightly the amount you can lift,” says Blower. “It depends on the geometry of where the extra weight is actually being carried.”
“The additional weight added by the extendible dipper puts a standard dipper in an advantageous position as it relates to lifting when the dipper is extended,” says Marringa. “As far as digging applications, the condition is arguable based upon the job being performed, as breakout capacities and bucket rotation are not affected by this option.”
Attachment precautions
Conrie insists the versatility and productivity increases of extendible dippers far outweigh any drawbacks. “There are virtually no disadvantages in equipping a machine with an extendible dipper,” he comments. “The loss in lift capacity with an inner slide design is very minor. Although the owner may pay additional for this feature, he will recover it in a short time through productivity gains.”
One way is through increased attachment versatility. While some manufacturers previously advised against using hammers with extendible dippers, for the most part, this is no longer the case.
“Hammers are approved for use with a JCB ExtraDig machine,” says Blower, adding that there are no backhoe attachments not approved for use with these machines. But the ExtraDig should be locked up in a retracted position for hammer use. “There is no excuse to use a hammer with an ExtraDig that is extended way out. You will just increase the wear on the slides.”
“When using a hammer or compactor plate mounted to an extendible dipper, the extendible dipper must be retracted and pinned in place,” Comrie agrees. “If the extendible dipper fitted with a hammer is used in a retracted position and pinned, the reduction in the life of this component will be minor.”
Case also advises discretion when using a hammer with the Extendahoe. While a hammer is approved for use, the operator must consider the forces applied to the dipper when it is being operated in the extended position.
Keep it tight
There is additional maintenance with any extendible dipper. One important consideration is ease of adjustment.
“It is a moving part so it will wear over time, especially when you are putting it down into the trench and into the dirt,” says Blower. “Dirt, sand and gravel will get into the slide, so there are wear pads.”
Because the operator needs a way to remove any normal wear out of the dipper in minutes, most extendible dipper sticks utilize wear pads. As the operator extends and retracts the dipper stick, the pads wears away, introducing slop — the enemy of productivity.
“You have to be able to get out there and tighten it up a little bit so that it stays solid,” says Blower. He claims this is easily accomplished on a JCB backhoe-loader. “Tightening the ExtraDig takes about five minutes. It is just re-torquing eight bolts.”
According to Marringa, maintenance on the Case Extendahoe is minimal. “Naturally, given the fact that a moving element has been added to what was a static dipper, there are some regular maintenance items, such as maintaining the proper level of grease lubrication,” he says. “But for the most part, it is all very basic and not necessarily significant.”
Design differences
Dipper stick designs vary by manufacturer. One of the most critical differences is whether the inner or outer part of the dipper extends out.
“There are pros and cons on both sides of it,” says Blower. “The advantage of a design where the inner, lighter part of the dipper extends out is the resulting higher lift capacity, simpler design and no lubrication requirement.”
Consider the geometry of the extendible dipper. “Extendible dippers with outer extending structures will have some impact on lift capacity, as the outer extending part is usually heavier than the inner part,” says Comrie. “On the Volvo BL70, the extendible dipper weighs 2,557 lbs. (The standard dipper weighs 1,700 lbs.) Extendible dippers that extend the heavier outer part may weigh around 3,000 lbs.”
On designs where the inner structure extends out, the backhoe can hold more weight, and the bigger, heavier part of the dipper stays closer to the tractor. “You keep a more stable platform. If you are lifting pipe over the side and swinging back to the trench, you actually have more lifting capability with the ExtraDig because you are not lifting the extra weight all of the way out,” Blower explains. “If you are carrying the heavier part all of the way out, you are reducing the amount of material you can put in the bucket.”
An inner extension also allows hoses to be routed internally. “We have designed all of our auxiliary circuits to run out with the ExtraDig,” says Blower. “You don’t have any loose hoses. The hose ends are on the tractor itself. With our design we keep the hoses inside so they are protected. When the boom and dipper are inside the trench, you are hitting the side of the trench with steel, not hoses and the clamps that hold those hoses on.”
The downsides materialize in certain applications. “If you stick a thumb on a dipper, the inner slide moves away and leaves the thumb attached to the tractor,” says Blower. “There are ways around that, but that is definitely one of the issues.”
Again, this depends on the design. “It is usually assumed that it is impossible to mount a thumb on an extendible dipper with an inner slide. However, that is not a true statement, as it depends on how the inner slide dipper is designed,” Comrie indicates. “The extendible dipper on the Volvo BL70 and BL60 not only accepts mounting of a thumb, but does it without requiring any anchoring or welding to the dipper structure.”
An advantage to having the outer part of the dipper extend is it limits exposure of the slide mechanism to the trench. In addition, the serrated edge on an outer box design allows for easy material clamping and keeps material out of the inner slide of the dipper stick. This also may allow easier fitting of a thumb.
“It is normally easier, depending upon the design of the outer box, to grab sidewalk pieces, debris or small logs with the bucket curled against a serrated outer box,” says Comrie.
Case Construction favors the outer slide design. “The construction or adoption of the outer slide design is a legacy component of the Case loader-backhoe,” says Marringa. “This approach to design provides a number of different advantages. From a maintenance durability level, the use of an outer slide ensures that the sliding components are consistently covered in lubricant, thereby extending the life by reduced friction and prevention of foreign material that might cause service issues.
“In cases where an application requires the use of a thumb attachment, the outer design makes it much easier and affordable to mount,” he continues. “Also, Case N Series backhoes, as with predecessor models, utilize a cast inner slider component that extends the life span and durability of the dipper assembly.”
Marringa notes that the Case engineering department has well documented the performance of the outer slide design and the company considers it an advantage under most load circumstances.
But different markets have developed unique preferences. Take Europe, for instance, where the side shift backhoe is more popular. “With the advent of side shift backhoes, the Europeans want inner slider arrangements for the stability,” says Blower, “where the North Americans prefer the outer box style.”