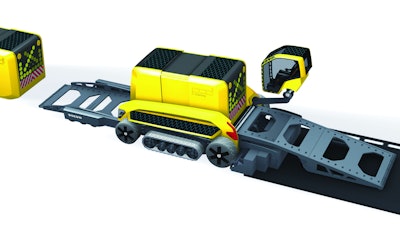
Volvo Construction Equipment (Volvo CE) has once again given its designers free rein to explore how machines might look in the future. The result is Fenix, an environmentally and operator friendly asphalt paver that simplifies and cleans up the messy business of laying a road. Named after the mythical fire bird, Fenix represents a rebirth and renewal of the paving process.
Currently, paving involves the coordinated interaction of lots of people and machines. There are workers controlling the depth, width and density of the asphalt. Not to mention the trucks, milling machines, pavers and rollers. Fenix is a single unit that performs both the paving and the compacting in a carefully choreographed fashion. It replaces the need for a team of pavers as all of its controls can be governed by a single operator. This reduction in the close interaction of men and machines will result in more consistently high quality roads, a safer work and traffic environment, as well as significant cost reductions.
How it works
Fenix uses the revolutionary idea of transporting the asphalt in 'thermopods.' If you imagine the mechanics of an espresso coffee machine, the pods work in a similar way. Just as you put coffee into a holder, connect it to the machine and pass hot water through it - the same is true of the asphalt, water and pods.
The thermopods are filled at a mix plant up to 30 miles away from the jobsite and transported to the paving site where they are positioned in front of the paver-compactor at 55-yard intervals. Three thermopods are loaded on the machine platform and unloaded after the material is laid down, which means that there is a continuous paving at a speed of 82 feet per minute.
Each pod can hold 17 tons of mix at 275 degrees F for up to three hours. The thermopods are coordinated from the mix plant to the jobsite by a superintendent. Each pod is fitted with GPS technology that keeps all people aware of each pod's exact location and estimated time of arrival to the paving site. There are even pod warning lights to create a 'virtual fence' around the jobsite.
The asphalt mix is unloaded from the pod and moved by conveyors to Fenix's auger chamber from where it is laid on the paving area. The pods are unloaded at a rate that is matched to the paver speed and depth requirements. They extend automatically when loaded and retract when unloaded.
Meanwhile, the operator sits in a state-of-the art, noise reducing cab, with the benefit of air conditioning and excellent all-round visibility using video cameras.
Uses water instead of oil
Fenix's hydraulics use distilled and de-ionized water instead of oil. Not only is this less expensive and more environmentally friendly but it also means that any leakages do not cause a problem. Using distilled water also has the technical advantage of making the machine more energy efficient, due to the water's low viscosity.
Designed to handle bio material and other environmentally friendly paving mixes, Fenix is designed with efficiency, safety and productivity in mind.
To see Fenix in action, check out its video on YouTube (http://www.youtube.com/watch?v=8BoAtlIPiAQ).