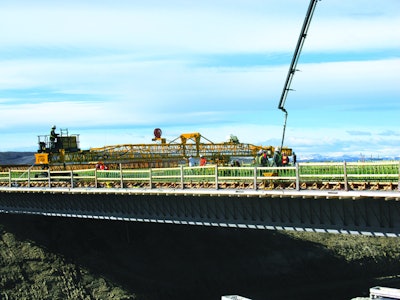
Graham Group Ltd., based out of Calgary, Alberta, Canada, started as general contractors in Moose Jaw, Saskatchewan, in 1926. Some 50 years later, the company began to build bridges, and have expanded over the years into several different areas of construction and construction management. Through all of their growth and expansion, the company has stayed true to bridge building.
When it was time to add another finisher to their inventory, the company sent an official to World of Concrete to research the latest bridge technologies and discuss their upcoming projects with the different manufacturers.
"David Impey, our Director of Engineering, went to World of Concrete to gather information, and the people in the GOMACO booth were more than pleased to help him out," Doug Kish, Concrete Specialist with Graham, said. "David was put in touch with Bob Coats, the cylinder finishers product manager at GOMACO, and we've worked hand-in-hand with him developing the exact machine for our needs."
Customized for productivity and weight savings
That machine is a new GOMACO C-450 with transitional framework, capable of spanning widths up to 104 feet (31.7 m). It was put to work right away on Highway 2 near Airdrie, Alberta, just north of Calgary, on a project with side-by-side bridges. Each of the decks would be nine inches (229 mm) thick, approximately 20,000 square feet (1858 m2) in size, and required 620 cubic yards (474 m3) of concrete to complete.
The transitional framework is a new design option for the C-450 that provides faster assembly and weight savings compared to wider-width finishers requiring an overhead truss system. The new frame features transition sections connecting the C-450's standard 24 inch (610 mm) tall framework to the 42 inch (1067 mm) tall framework used on a C-750 finisher. The frame sections only need to be pin-connected and the cross arms bolted in place.
The overhead truss system is eliminated. The transitional framework not only provides a much quicker assembly time, but also decreases the weight of the machine considerably. It is estimated to be eight pounds per foot (11.9 kg/m) lighter when compared to a machine with overhead truss.
"It's a considerable weight savings," Bob Coats, Cylinder Finishers and Trimmer/Placers Product Manager at GOMACO, said. "On Graham's machine at 104 feet (31.7 m) wide, we lightened the weight of the machine by approximately 832 pounds (377 kg)."
The transitional framework sections can also be removed and the C-450 can finish at smaller widths with its standard 24 inch (610 mm) framework. The new framework allows the versatility of two finishers in one for the narrower or wider widths. The new transitional framework can be added to new or existing C-450s.
Graham also utilized the optional third wheel assist on their C-450's standard bogies to further distribute the machine's weight while traveling on the rails. The optional, third wheel assist bogies, on each side of the finisher, consist of two single-wheel idler bogies attached to the spreader beam. It's a simple modification that can be made to any C-450 or C-750 to help spread the weight out and reduce the wheel load on the overhang brackets.
On- and off-the-job training
Specifications for bridge decks in Alberta require a concrete mix design with silica fume added. It creates a high-strength concrete, but is a challenge to finish because of its sticky texture. Graham equipped their C-450 with a heavy-duty, externally-vibrated, double-cylinder undercarriage with five foot (1.5 m) long cylinders. The external vibration helps deal with the stickiness of the concrete mix design and creates a better finished driving surface. The smoother driving surface will be appreciated by the drivers of the approximately 30,000 vehicles traveling across the bridges each day.
Training on the company's new C-450 was both on-site from GOMACO service representatives, along with a trip to GOMACO University in Ida Grove, Iowa. The company sent 12 of their people to the week-long C-450 class at the University. Personnel attending ranged from laborers to superintendents to equipment managers.
"Everybody really benefitted from it," Kish said. "We learned what questions we need to ask, from how to order the piece of equipment to what we need for the job. We were taught how to put the finisher together for our current job and also ones in the future. Our guys are now really comfortable with the machine, what it can do, and what we need to do to set it up properly."
Then, for each of the bridges, a GOMACO service representative was on hand to assist during the pours.
"They showed us some great tricks that make a big difference in the final finish," Kish said. "The biggest thing on the machine is making sure the drums are set properly. The trick for that is set the back end about 0.125 inch (3 mm) higher than the front end. It makes all the difference in the world."
Going with the flow
Each of the decks, built with a 4-inch (102 mm) crown, had to be dry run with the bridge inspectors on-site to supervise and make sure the deck would get the proper amount of concrete coverage. Once the inspectors signed off, the finishing could begin.
The silica-fume concrete was placed on the deck by a concrete pump. Slump was kept around three inches (76 mm) to help ensure easier placement. The C-450 was set on a skew and the bridges took two days to complete. Each daily pour lasted approximately five to six hours to complete the 10,000 square feet (929 m2), one-half of the deck.
The newly finished deck is covered with burlap and kept wet with a spray-mist system for seven days as part of the curing process.
"The hardest aspect of any bridge deck pour is just trying to maintain the flow... keep the concrete running, the guys working, and the finisher finishing," Kish said. "The C-450 with its double drums is a big help, and makes all the difference for a smooth surface with fast production."
Graham has successfully completed the twin bridge decks on Highway 2 near Airdrie. They've moved the C-450 onto other projects that aren't as wide.
"We're putting it together now for a few more bridges, but they aren't wide enough to require the transitional framework," Kish said. "That's the nice thing about this new machine. We just leave the transition sections out and use the standard 24 inch (610 mm) framework. It works out really well."