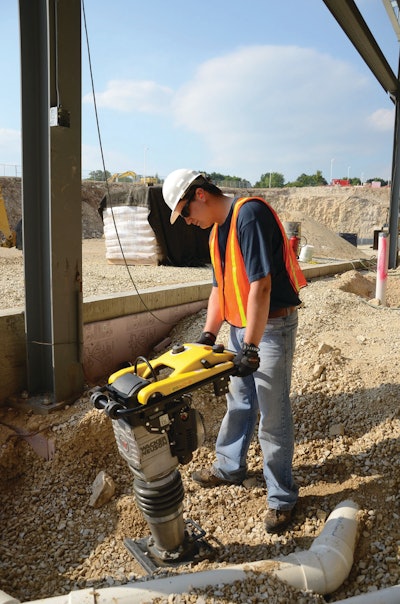
Engine manufacturers agree that rammers are the toughest application for their products. There is no other machine that creates more vibration and takes more abuse from operators than a rammer. Because of that, or perhaps in spite of it, today's rammer engines have been designed to take their licks.
A brief history lesson
About 15 years ago, Honda introduced the first four-stroke engine for rammers, a significant advancement in that it alleviated one of the key challenges centering on rammer operation – there was no longer any need to mix gas and oil, a process fraught with potential for error. Previously, four-stroke engines couldn't be used on rammers because laying the machine on its side – common during transport -- would cause gas to flood the carburetor, damaging the engine.
Since the introduction of Honda's G100K2 AR engine, many rammer manufacturers adopted the use of four-stroke technology, replacing their two-stroke models with four-stroke versions. Not all followed suit, however. Wacker Neuson, in fact, still maintains its commitment to the two-stroke rammer and is the only manufacturer that still builds a two-stroke engine for its machines.
"We've always manufactured a two-stroke engine for rammers, built in Menomonee Falls, WI," says Dave Schulenberg, compaction product manager at Wacker Neuson. "It will always be our core engine for rammers. It's the only one built specifically for rammers."
Schulenberg explains that Wacker's two-stroke engine is ideal for withstanding the intense vibration inherent in rammer use. There is no oil sump on the two-stroke engine; the oil is injected as needed, so it's highly efficient. Two-stroke rammers can be laid on their side, he adds, and while it's true that today's four-stroke rammers can handle the side orientation as well, it's less reliably true. "As machines get older, there is still a chance that laying it on its side could cause damage," he explains. "We advise that four-stroke rammers be left in the upright position for a while after use before laying them down."
Schulenberg adds that Wacker Neuson two-stroke engines are durable, have fewer moving parts than four-stroke engines and meet all current EPA emission requirements. Wacker Neuson also manufacturers four-stroke rammers, as well as diesel, to meet customer demand. "As much as we believe that two-stroke is best, the customer is always right," he says.
Designed for the application
Today, four-stroke engines dominate the rammer market and leading engine manufacturers continue to work on designing the best engine for the application. Subaru, for example, recently introduced the ER12 for rammers after working very closely with OEMs to meet their design specifications. "The application for which a rammer engine is designed is very unique and very specialized, which means the engine and its features have to be matched to each OEM's product individually," says Brad Murphy, vice president of sales and marketing at Subaru Industrial Power Products. "So we work very closely with each OEM, essentially customizing the engine to their needs, and virtually every customer receives a different version of the ER12 engine."
Currently, OEMs can choose between either a diaphragm or bowl-type carburetor, Murphy says. "The ER12 also comes with a standard air cleaner, but many times the OEM will augment our air cleaner with a primary air cleaner, and then our standard unit becomes secondary. Other times, they'll design a new, larger air cleaner that's mounted on the equipment. Either way, we work with them closely on the air cleaner modifications to make sure the engine's performance isn't affected, and to ensure the new unit meets the emissions standards. Air cleaners and carburetors are both emissions parts, so we need to be very involved with the OEMs to make sure they're still in compliance."
Murphy adds, "A rammer engine is a reciprocating part of the machine, it moves with the product, so items like mass and dimensions are very important and must be integrated into the product design. The weight and balance of the engine and the way it performs are a big deal. It's completely different than any other engine."
Honda, for its part, offers two engine models for rammers, the GX100 and the GX120. The GX100 is used primarily for 55 to 65kg rammers while the GX120 can go up to 70kg. "Honda works very closely with our OEM customers to match our engines to their applications and their specific requirements," says Rick Wendt, national manager, OEM sales, Honda Engines. "For example, some OEMs use their own air intake system and we were able to match our components with theirs to ensure that all emission regulations were satisfied. In addition, we always confirm the connection points between our engine and the OEM frame components so that the combined product will be best for our mutual customers."
Features and benefits
Honda's rammer engines have two types of carburetors (diaphragm and float) which both incorporate a special structure to prevent overflow when the rammer is laid down. The Honda oil alert system on the rammer engines is also unique because it only operates during engine starting due to significant oil splash during operation.
"In addition, our GX100 split-case OHC design allows the engine to be mounted directly to the rammer with no need for an engine base support," Wendt says. "This allows for a compact design with improved strength and toughness against high vibration."
Rammer engines are subjected to high vibration and operation in dusty environments. With that in mind, Honda rammer engines are compact and powerful. "They have designed in protection against carburetor overflow and a special oil alert system that only operates during engine starting to eliminate any nuisance engine stopping from oil splash during operation," Wendt says. "Our designs offer industry-leading protection against high-vibration operation in dirty/dusty conditions."
According to Murphy with Subaru, the number one advantage the ER12 offers is that it's a completely original design, specifically and exclusively intended for use with rammers. "We didn't copy a design, or attempt to repurpose an existing engine for a rammer," he says. "It's compact and lightweight, and maintains an excellent center of gravity to effectively transmit power to the ground, which in turn allows the rammer to offer superior performance."
Murphy goes on to say that the ER12 offers quite a few unique features that contribute to the optimally balanced, lightweight design, while allowing it to provide more power per cc of displacement. "First, the starting point is the overhead cam (OHC) design. That's really what allows the engine to offer improved performance and more power output. In fact, the ER12 produces more power than the largest engines on the market, and is also smaller and lighter than the current smallest engines," he says.
Further enhancing the lightweight design, the crankcase features a thin-wall, yet durable construction and a lightweight aluminum flywheel, Murphy says. Subaru has also reduced the muffler size and weight.
"Also, the engine has a unique torsion bolt structure. High-strength torsion bolts extend from both the cylinder head and the gear cover deep into the crankcase," Murphy says. "This unique design allows less material to be required on the cylinder, heads and blocks, further reducing overall weight while improving structural strength."
Additionally, the torsion bolt structure also contributes to optimal balance, which is key in rammer engineering. The ER12 is designed to be balanced very close to the mounting face, and also balanced on the side-to-side axis for best compaction performance and easy operation. Also, Murphy says the recoil has been integrated into the flywheel and blower housing, further enhancing balance and overall engine performance.
"Two other major features offered on the ER12 engine are the pressure lubrication system and low oil pressure shut-off system. Because of their constant up-and-down motion, rammer engines are difficult to lubricate, so the ER12 was designed with a pressure lubrication system," Murphy explains. "A gear pump transfers oil from the bottom of the crankcase to various parts of the engine that need critical lubrication. The low oil pressure shut-off system does exactly that – shuts off the engine if oil level gets too low. It also allows the rammer to be tipped on its side without any problems, which is great for transportation of the entire unit."
A tall order
Rammer engineering is tricky and balance and weight are the two toughest challenges. "Because the engine is being bounced around with the force of the rammer, overall strength is crucial," Murphy says. "Normally you design an engine to handle the internal force of the engine, and the engine is stable on the product. But in the case of a rammer, it needs not only the strength to handle the internal forces, but it also has to be able to handle the rigors of being bounced up and down and the G-forces being applied because of the product."
He adds, "As you can imagine, maintaining strength while keeping the engine light and compact is difficult to do, but it's essential on this product. The challenges presented by rammer engineering just further drive home the importance of having an engine specifically designed for this application, and our ER12 is."
Peter Witt, Weber MT, makers of rammers and plate compactors, points out the power to weight ratio has always been vital to the design of a rammer engine. "Unlike with vibratory plates, creating a weight that can be handled by one person (120 pounds) is critical. Older designs may meet the weight criteria but the engine was too weak; one could stand on the rammer shoe and literally stop the percussion function (not Weber but some competing brands)," Witt says.
Honda engines are known for their durability and "startability." They also have a reputation for being simple to operate and service. "The unique oil alert system allows the user to check the oil only before starting instead of more frequently, which minimizes the opportunity for dust to enter the crankcase," Wendt says. "The OHC belt design in the GX100 is quiet and has very high durability, designed to last the life of the engine. The split-case design allows for easier service due to no lower engine support required. All of our controls are clearly labeled and make the Honda engine simple to use."
Wendt adds, "Honda's engine application process helps to ensure that specific durability requirements and tests are met or exceeded (drop test, laydown condition, operator access to controls, etc.)."
Honda and Subaru have worked very hard to advance the state of the art of four-stroke rammer engines, but Schulenberg at Wacker Neuson maintains his position that two-stroke rammer engines are unsurpassed, adding that the incorporation of Wacker Neuson's patented compensating carburetor has significantly increased the machines' environmental friendliness. "Since making improvements to our rammers in 2010, our two-strokes have the lowest total emissions than any other rammer on the market," he states.
"Two-strokes are much smaller than four-stroke engines, but offer the same horsepower. They offer better balance because they're lighter, so it's easier to keep the rammer moving. This results in less operator fatigue and increased productivity," Schulenberg says. "Customers are worried about uptime, so the easier you can make a rammer to use, the better."