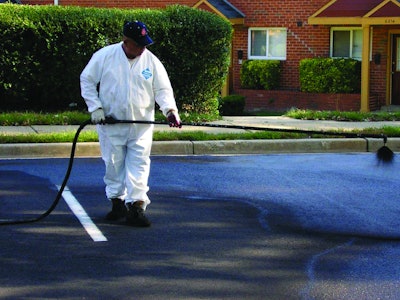
A sealant without an aggregate is like an apple pie without cheese. It’s doable, but the end result could be a lot better with the add-on. Yes, the analogy is a stretch but adding an aggregate to the sealant mix design makes all the difference in the world. Among benefits, an aggregate improves pavement surface traction, fills in hairline cracks while hiding minor surface defects, and increases the longevity of the sealing job.
Two types of aggregates are readily available, silica sand and crushed boiler slag. U.S. Silica is one of several producers of high purity silica sand. As explained by the company’s marketing manager George Dodson, high purity silica sand is found in various locations throughout the country. “The geologic environment that produces high purity silica sand usually is one where the sand has been subject to a high level of energy over an extended time period,” he relates. “An ocean beach, a wind-driven sand dune, or an intertidal zone with a lot of water movement, provides the correct geologic environments to concentrate and wash the silica sand grains.” U.S. Silica has 12 silica sand plants throughout the Eastern and Central United States.
Harsco Minerals, formerly Reed Minerals, produces a crushed boiler slag under the registered trademark of BLACK BEAUTY® abrasives. An inert by-product of coal-fired plants, the BLACK BEAUTY® slag is cleaned, crushed, and sized to produce uniform angular particulates, with color and hardness characteristics to make them attractive to the seal coat and paving industry. Harsco Minerals has 15 plants throughout Eastern and Midwestern United States.
Both aggregates have their application. Sand that is round provides excellent adhesion within the sealer. Because of its shiny color BLACK BEAUTY® abrasives lend sparkle to the pavement surface. Because particles are more angular than sand, this aggregate is often used where more traction is desirable or in applications where the surface is especially worn. No matter what the chosen aggregate is, it must be washed and dried, free of dust, clay, organic matter, or other contaminants, and meet the gradation requirements per the sealcoat manufacturers’ specifications, somewhere between 50 to 75 mesh AFS.
In the Mix
A mix design for sealcoat contains four elements: the concentrated sealer, water, additives, and an aggregate. As Geoff Crenson, Technical Manager for GemSeal/Bonsal Amercican points out, contractors typically find a mix design that works well for their applications and stay with it. The exception occurs if and when a property manager or other client specifies something different. Says Grenson, “In either case, having the right-size aggregate and using the right amount is critical.”
STAR’s President Girish Dubey agrees. “For normal applications, between 2 and 2.5 pounds of aggregate per gallon of undiluted sealer is recommended. For rougher pavements, the rule of thumb is 4 to 5 pounds per gallon, never to exceed the five pounds per gallon limit. With too much aggregate, the sealer becomes brittle and loses flexibility and resistance to chemicals, fuel, salts, and so forth.
“When selecting the size of the aggregate, it is imperative that the average particle size be very close to the cured film thickness of the sealer. The particles should be at least two thirds imbedded into the cured sealer film. For example, two coats of a sealer will dry approximately 11 to 13 mils thick. The size of the aggregate particles, therefore, should be within the same size range. An aggregate that is 50 to 75 mesh AFS would usually satisfy this requirement.”
Dubey notes that using an aggregate like sand that is too fine will soak up excessive binder amounts from the sealer reducing sealer performance. Conversely, course particles will fail to interlock and knit into the cured sealer film, and likely become dislodged under traffic. “The loose sand,” he explains, “acts as a sand paper on the cured sealer film and may cause premature failure.”
He continues, “The same attention to gradation detail is important when using crushed boiler slag, which is much harder than sand and incapable of absorbing as much binder or water. This means that the aggregate will not be as tightly held in the cured sealer film as sand, making it susceptible to being ‘knocked off’ if the grade is too coarse.”
Adding the Aggregate
A sealcoat mix design has to meet several requirements, adds Crenson. “Among them, it must be the right consistency to achieve uniform application and flow adequately enough to fully wet the surface, but not so runny that material drains off the aggregate and surface plateaus into crevices. The mix consistency needs to have enough body to envelop the aggregate and keep it coated as the sealant cures to lock it into the coating membrane.”
He advises adding in the aggregate last, after water and additives have been mixed in with the concentrated sealer and the consistency and viscosity of the design have been adjusted. “Additives are included in the mix design to improve drying, adhesion, color, and elasticity of the end product, with some having multiple benefits,” Crenson notes.
A mix consistency that keeps the aggregate suspended in the mix tank helps to ensure uniform distribution of aggregate throughout the seal coating job, he adds. “If a thin mix allows aggregate to sink to the bottom of the tank during application, variation in the appearance of the cured coating could be noticeably thin in some areas, and excessively coarse textured in others.”
STAR’s Dubey encourages contractors to purchase their aggregate in bags to ensure it is dry and can be measured accurately as part of the mix design. “Ideally, one would add in one bag per minute with agitation,” he points out.
Helpful Hints
Aggregate particle gradation is determined by its mesh size, which represents the number of openings per inch in a screen. Hence, an aggregate with a lower mesh number has particles that are coarser than an aggregate with a higher mesh number. Says Dubey, “The different grades of aggregate are classified according to their average particle size and denoted as AFS (American Foundrymen Speficications) numbers. For example, AFS 60 grade has the majority of particles passing through a 60-mesh screen”
Sealer producers like STAR, Inc., and GemSeal/Bonsal American recommend using an aggregate with their products. As Dubey notes, though, not every contractor is aware of the benefits that an aggregate like sand brings to the sealing job or has the right equipment -- having a machine with a pump capable of spraying a sealer with aggregate or a tank with agitation.
Both producers offer tar- and asphalt- based sealers. Says Dubey, “Despite their different properties (i.e., tar-based sealers being made from refined tar and asphalt sealers from refined crude petroleum , the applications for each are similar, including the use of an aggregate. Dubey and Crenson advise putting down two coats of sealer for best results when it comes to the job’s appearance and hiding minor surface defects, improving traction, and improving wear ability.