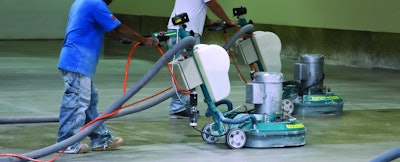
Selecting equipment to grind, hone and polish can be a daunting task. There are several factors to take into consideration, among them the equipment's power requirements, weight, motor size, overall dimensional size, working dimensions and direction or directions the abrasives rotate. At this point you may be thinking, "What is so daunting? It looks pretty basic to me." There is a saying in this business,"The more you learn the more you realize how little you know."
As you read this article keep in mind it addresses common or typical machines; specific characteristics vary from one manufacturer to another. Let's examine the selection factors.
Power requirements. Equipment is either powered by cord electric, battery electric or propane, and in some cases hydraulic driven motors are used. With propane power there are no cords and no electrical requirements other than the battery used for starting the machine. Electrical requirements for cord electric equipment are typically 110 volt single-phase, 220 volt single-phase or three-phase, and 460 volt three-phase. Some 220 volt pieces of equipment allow you to run them single- or three-phase. Amperage requirements can range as low as 20 amps and as high as 60 amps.
Keep in mind high motor voltage equals lower amperage requirements and smaller gauge power cord. Although, many electrical panels are thought of as 220 volt and often their true output is only 208 volts. If you plug your machine into a source that is only 208 volts make sure the equipment has the ability to run on the lower voltage. If not you will have to invest in a transformer, often referred to as a buck booster, to boost the voltage. NOTE: Always use a qualified, licensed electrician when hooking up your equipment for use.
Weight. Walk-behind equipment ranges in weight from 110 pounds to over 2,000 pounds before optional weights are applied. Ride-on equipment can weigh over 13,000 pounds. Equipment weight is important from a transportation point of view, but more important is the actual weight or head pressure over the abrasives.
Motor size. Motors range from 1 hp on a small, single-head rotary machine to 40 hp on a walk-behind machine with a multi-rotary head. There are three variables that affect the amount of power required for a machine to efficiently operate — how much contact area there is between the abrasives and the concrete surface, the grit designation being used, and the weight of the machine. These variables contribute to friction between the abrasive and concrete. The higher the friction, the more power required to drive the abrasives.
Overall dimensional size. You can find equipment small enough to fit in the back of a small hatchback and equipment so large it will only fit on a flat bed tractor trailer. Equipment comes in all shapes and sizes. Some break down into multiple pieces for easier transportation and some are all one piece.
Working dimensions. This is defined as the overall area the abrasives affect when the machine is running. Equipment working dimensions can range from square and 14 inches to round and 15 inches to 98 inches with multiple planetary heads.
Push, propel or ride on. Some machines are designed to be pushed, pulled or moved side to side while others are propelled with motor-driven wheels or come as ride-on units.
Belt/chain, gear or direct drive. The rotating heads of the machine are most often driven by a main or centralized motor that uses a belt or chain in conjunction with a pulley system. Some equipment eliminates all belts or chains and uses a gear system. Small, single rotating head machines are usually driven directly from the motor.
Abrasives drive. There are machines that have a large fixed single rotating head that may measure 15 to 20 inches, fixed dual rotating heads that are positioned side by side, machines that have two to eight rotating heads that intertwine in a gear-like fashion whose working width is up to 56 inches, and then there is planetary equipment where one large head rotates in a direction in addition to smaller satellite heads that also rotate in the opposite or same direction.
Planetary equipment can be considered passive or active. Passive planetary is when the satellite heads spin in one direction and the main head spins in the opposite direction as a result of it following the path of least resistance. Active equipment is when the satellite heads and the main head spin in opposite directions or in the same direction because they are driven independently of one another, each with its own belt/chain or gear system.
Some equipment gives you the option to control which direction the main head and satellite heads rotate through the use of a second motor. One last note — some equipment has variable speed and the ability to change the direction the heads spin while others are only one speed and only work in one direction. Is your head starting to spin yet?
What equipment is right for you?
Okay, so here is the million dollar question, "How do you decide what equipment is right for you?" Below is not necessarily the answer but a good guide and thoughts to help narrow down your decision.
You need to first decide the immediate market you are going to service. Is it residential, commercial or a combination of both? If you are going to service the residential market, it will be rare to find three-phase power. To prevent the added expense and the need to tow or have a generator mounted in your truck or trailer, you will have to choose equipment that runs on 110 volt or 220 volt single-phase power. Also, keep in mind that your equipment will have to fit through residential doorways and be able to be moved up and down stairs unless you are only working in garages.
If you service the commercial market there will be times when three-phase power will not be available. When it is available it is usually only 220 volt three-phase not 460 volt three-phase. Motors that run off of 220 volt three-phase power have high amperage requirements. When running 220 volt three-phase equipment with long runs of power cord you will need four-gauge wires. I can tell you from experience that four-gauge, four-wire cable not only gets very heavy but also the cost of 60 amp plugs will make your head spin faster than the satellite heads on a planetary polisher.
Will you offer surface preparation, polishing or both? If you would like to perform heavy surface preparation you will need a machine that has adequate weight and horsepower. Remember the heavier the machine and the larger the motor, the more power you'll need. When performing light to medium prep work with a lighter machine the proper abrasives play a key roll and the same is true when polishing with heavy equipment.
How big are the jobs you are trying to tackle? Are the jobs 2,000 square feet and under? If so, a 22- to 25-inch machine can tackle this size job in a timely manner for most processes including polishing. Areas larger and you will need multiple pieces of the same size equipment or make the decision to purchase larger equipment. When making this decision, take into consideration the ability to put multiple machines on one job for increased production or on separate jobs to have the ability to tackle multiple jobs at the same time.
Are your jobs in open areas or broken into smaller areas? Large equipment works well in open areas but when having to work in areas with lots of rooms and tight corners smaller equipment may be your better option. If your market is consistently open areas of 1,000 square feet and over with doors that are 36 inches wide or larger, a 32-inch machine will significantly increase production. Remember that smaller machines offer a lot of versatility but require more manpower whereas larger machines have less versatility but increased production. Increased production and less manpower equals more profits or the ability to price a job more competitively when needed.
There are many issues to consider when choosing the grinding, honing and polishing equipment that's right for your company. Educate yourself on the options in the industry and consider how the machine characteristics will help you produce the floors your customers want.