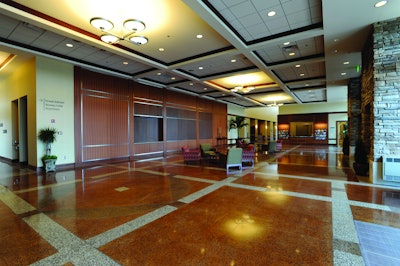
The newly constructed Clarence Brown Conference Center in Cartersville, Ga., is about an hour north of Atlanta. Visitors to the 45,000-square-foot facility are greeted by a polished concrete floor in the main corridor and entrance lobby. Natural gold, black and white surface-seeded aggregate, an intricate saw-cut pattern and a multi-color design throughout the floor create what Middle Georgia Concrete Constructors CEO Scott Truax calls "a contemporary twist on an old, stately terrazzo floor."
Middle Georgia, a full-service concrete construction firm out of Atlanta, Ga., has been offering polished concrete through its decorative concrete division, CSolutions, for four years. About 75 percent of the work through the decorative division is polished concrete. Truax is a CPAA-accredited Craftsman and oversees the work on his team's concrete polishing jobs. "Our focus historically has not been on the big box-type, large floor polishing jobs. There are enough people doing that," Truax says. "Our focus has been these boutique-type jobs — broadcasting aggregate, intricate scoring and dying, public school work, and the kinds of jobs where we can include polishing as part of our entire project package."
The work at the Clarence Brown Conference Center came about after Middle Georgia presented a "lunch and learn" program on surface seeded aggregates and polished concrete for local architects. It was the contractor's third project with this particular architect, and Middle Georgia worked closely with the firm through the design process.
Truax invited the architect to the Middle Georgia headquarters, gave her a 12-inch tray and samples of the company's available aggregates, and allowed her to develop the aggregate blend she wanted. Choosing a dye color wasn't as easy. The floor is made up of different colors, including natural concrete, a reddish-orange and tan. Since none of the standard colors offered the hues the architect was looking for, Truax worked with her to determine the correct blend of colors for the floor.
After samples were cast and accepted, Middle Georgia was awarded the work to place and finished the L-shaped 7,800 square feet of floors that would receive a polish along with the polishing work.
Placing the slab
Middle Georgia placed and finished the concrete slab in four pours over the course of two weeks. In each pour, the crew placed the concrete, floated the slab, broadcast the aggregate, floated the surface a second time and finished the concrete. Quality control is one of the advantages Middle Georgia enjoys when it places its own concrete slab before a polish. Truax explains a few placing and finishing practices the company follows in order to achieve a concrete surface optimized to take a polish.
"When you're broadcasting aggregates, flatness is the key," Truax says. "And once we broadcast the aggregates, we don't go back on the floor and walk on it. The first couple installations we did like this, we walked on the slab with traditional walk-behind trowel machines. You could really see the aggregate pushed down where the men were walking behind the trowel machines."
Truax further explains how this uneven aggregate depth makes it difficult to expose the aggregate evenly throughout the floor on the first pass with the grinders. Now his crews avoid walking on the slab after it broadcasts the rock. In order to do this, the placing crew makes narrow pours so it can access the slab from outside the forms.
An intricate cut
One of the most unique features of this project is the saw cut pattern on the floor. "Before the job we sat down with the structural engineer and came up with a control joint layout plan that also worked with the decorative design," Truax says. "So we looked at it first from a structural perspective and where the joints needed to be to reduce cracking. Then we looked at how to incorporate those joints into the design and where we would add additional cuts to get the design the architect was looking for."
The Middle Georgia crews installed the control joints the day after the pour with early entry saws. Additional decorative scoring was done during the polishing process, after the 200-grit resin abrasives pass and right before densification and dying. "You can perform the decorative saw cuts earlier, but we wait so we don't have to clean out those joints," he explains. "If you saw cut them earlier you just have to clean out the heavy sludge and slurry between each abrasive step."
The polishing process
After the place and finish, the six-man Middle Georgia polishing crew waited one month before starting the polishing sequence. The crew used a propane-powered 36-inch grinder/polisher from Eagle by Stonekor and a PowerStar Mongrel grinder/polisher. It also utilized Eagle's edge grinder for about 75 percent of the edge work, finishing out the balance of the edging by hand grinding.
Crews started the polishing sequence with 46-grit metal-bonded abrasives. They moved up to 70-grit metals and finally to 100-grit metals before switching to resin-bonded tooling. The first step in the resin-bonded sequence was a 50-grit abrasive; from there the crews moved to a 100-grit then a 200-grit abrasive. At that point, the crew densified the floor with Prosoco's Consolideck LS densifier and applied the architect-approved blend of standard dye colors from L. M. Scofield. The crew then proceeded sequentially through the CPAA-recommended polishing sequence up to 800-grit abrasives.
The floor was finished with Consolideck LS Guard and a pass with a burnisher. Middle Georgia left the owner with a maintenance plan that includes regular sweeping and cleaning.
The project was a successful one and went relatively smoothly, thanks to careful planning. "It wasn't a big job in terms of square footage, but it was the most intricate job we have done yet due to the scoring and the three different dye colors," Truax says.
Project Summary
Company:
Middle Georgia Concrete Constructors and its decorative division CSolutions
Services Offered:
Full service concrete construction and decorative concrete
Number of Years in Polishing:
4
Certification Level in CPAA:
Craftsman
Project Size:
7,800 square feet
Key Products & Equipment:
Eagle by Stonekor grinder and edge grinder; PowerStar Mongrel grinder/polisher; L. M. Scofield dyes; Prosoco Consolideck LS densifier and LS Guard; Husqvarna Soff-Cut saw for control joints; Mongoose decorative saw by Engrave-A-Crete; Superabrasive diamond tooling.