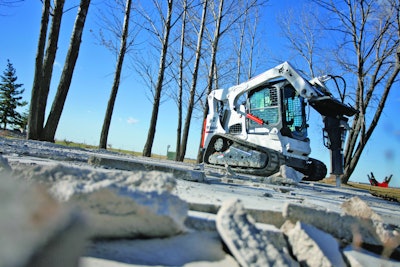
Today’s competitive market requires that fleet managers carefully scrutinize every purchase. Past experience becomes invaluable when comparing equipment alternatives. With the compact equipment market starting to rebound, one area that deserves close attention is whether a skid steer or compact track loader makes more sense.
Choosing the right tool becomes a numbers game. “Experience has taught customers that to improve their profitability, application management (matching the right task to the loader) of their fleet is very important,” says Jamie Wright, product manager, Terex Construction Americas. “Applications in certain ground conditions, such as hard surfaces like concrete or rock, can be done at reduced cost when using a skid-steer loader. For example, putting compact track loaders into application like demolition and road building can cost a customer up to 25% more per hour of usage because of excessive track wear in these operating environments over a skid-steer loader, greatly impacting their bottom line.
“We’ve see growing demand for track loaders in more applications, but as some owners unfortunately find, there are jobsites not really fit for track loaders in which skid steer loaders with severe-duty tires are much better suited,” says Kelly Moore, skid loader product manager, Gehl. “When ground conditions have larger aggregate, rocks and/or debris, it is simply not conducive for track loader operation.” It significantly shortens life of the tracks. “A skid loader equipped with severe-duty tires is better suited for these conditions. While these types of tires are more costly than the conventional flotation, lug-style tires for skid loaders, the costs for replacements of rubber tracks will far exceed the costs of replacement tires. Common sense is really the rule when choosing applications for skid loaders and track loaders.”
Either machine can usually accomplish the task. “The versatility of both machine types allows for these units to cross over into other applications, but each definitely have their arena within which they excel,” says Brian Rabe, track loader product manager, Gehl. “This versatility has led to these two markets continued growth over the years. Initially, I think customers were using track loaders in applications which may not have been suited to the machine. I think they now better understand where and when they should use a track loader over a skid loader.”
Versatility versus price
Often a compact track loader can be justified simply by increased versatility. For instance, Bobcat Bob, headquartered in Olympia, WA, performs a wide variety of tasks with its compact equipment fleet. It digs swimming pools, performs landscape rock work, does a variety of demolition work – including inside buildings, digs utility trenches, etc. Bobcat Bob takes pride in being able to tackle a wide variety of tasks with its compact Bobcat equipment fleet, which includes a 337 excavator, a Toolcat, a S220 skid-steer loader, a 463 skid loader and a T320 compact track loader.“I probably have 24 different attachments,” says Bob Aldous, owner.
But the track loader accumulates the most hours. “I use it 90% of the time,” reports Aldous. “The track machine goes anywhere. I have been to jobs where they can’t get a big excavator or dozer in because they sink on the site. As long as you keep the bucket on the ground and slide the weight across it if you have a bucket load, you will not get stuck.” It also simplifies grading. “It floats over the ground and you can get a nice, smooth grade.”
Work on slopes favors the track loader. Aldous recently purchased a 100-in. bark bucket for his track loader to mulch walking trails that were inaccessible to skid-steer loaders. “With the track machine I could drive up it forward or I could back it up the slope. With a rubber-tired machine on a steep hill, you have to turn around and drive it up backwards if you don’t have any weight in your bucket.”
It also comes in handy on demolition sites. “If there are a lot of nails I will use my track machine around the jobsite,” says Aldous. “With a track machine you don’t have to worry about a flat tire.”
But Aldous still finds a few applications where he prefers his skid loader. The most common of these is when a lot of material has to be transported over a hard surface. “I take the rubber-tired machine because I have the two-speed transmission in it. You can run it at 11 mph if you have to pack the material a long ways.”
Tracks offer capability at a price
First you must realize compact track loaders and skid steer loaders are rated differently. “You have to be careful when comparing skid-steer loaders and compact track loaders to make sure you’re really looking at machines that have very similar specs,” cautions Curtis Goettel, marketing manager, Case Construction.
“There will naturally be differences in comparing a common-sized skid loader to a track loader dependent upon the tires and bucket on a skid loader as compared to a track loader, as well as comparing load capacities where skid steers are rated at 50% of tip capacity while track loaders are rated at 35% of tip capacity,” says Moore.
But any comparable compact track loader will require a higher initial investment than a skid-steer loader. Manufacturers quote initial track loader purchase prices that range from 20% to 35% more than comparable skid-steer loaders. Most of this is due to the additional cost of the undercarriage components.
As any contractor realizes, however, purchase price is only part of the equation. Mike Fitzgerald, Bobcat adds, “There is a difference in price, but you have to consider what this machine will do for you. There are additional costs in purchasing on the front side, but there are a lot of benefits and features of that track loader.”
Tires and tracks often drive the operating costs of either type of loader. “Tires are the single highest cost item in operating skid loaders and attribute to the highest cost of replacement on these machines,” notes Moore. “Likewise, but at a considerable higher cost, are rubber track replacements on track loaders. The wear of either tires or tracks is directly proportionate to the amount of ‘skid steering’ done on hard surfaces. In addition, on a track loader, the replacement of carriage parts, such as rollers and idles, come into play. Overall, the owning and operating costs on tack loaders will be considerably higher than comparable sized skid loaders.”
Owning and operating costs will be unique for each application. “Based on customer surveys it is estimated that track loader owning and operating cost comes in around $35 per hour of operation,” says Rabe. “Track replacement is generally 4% to 6% of this cost depending upon the application and conditions. It is generally understood that the owning and operating costs will be higher of a track loader. However, for certain applications, this additional cost can be significantly offset if a skid loader is unable to get into the jobsite or won’t perform relative to conditions. Weighing the demand/utilization for conditions best suited to the product type during the purchase process is a very important factor in determining what type of unit should be purchased.”
Fitzgerald notes, “Your cost per hour on a track loader is probably going to be a little more because with tracks you are going to use a little more fuel, but you are going to get more work done. On a plain black and white piece of paper it is going to cost you more to run this. But then you are going to have to stand back and say I moved 25% more material, but it only cost me 15% more cost per hour.” These numbers are just used as an example. “Everybody is going to be different.”
Utilization also plays a role. Fitzgerald recalls seeing a contractor who seemed to be using a track loader when it didn’t seem to fit the application. “He said for 80% of what I do, I don’t need a track loader, but for the other 20% I have to have a track loader. I am willing to pay the extra on the other 80% because then it is 100% productive for me. Otherwise I can’t do the other 20% of what I need to do.”
Prices for replacement tracks and tires varies by the type of replacement you choose. “There are considerable differences between types of actual tire options for skid loaders, as there are in replacement tracks for track loaders,” says Moore. “In comparing flotation, lug-style tires to a common, OEM-type replacement track, the estimated pricing can run from approximately $200 on a tire to $1,600 on a track.”
Fitzgerald notes, “A good general purpose tire for a skid loader is going to be $150 to $300, depending upon the size and kind of tire. A set of tires would be between $600 and $1,200 depending upon what you are putting on. A set of tracks in the same range is anywhere from $1,250 to $1,700 per track. So you are looking at $2,500 to $3,500 for a set. So it is more to buy tracks.”
But there is an option other than general-purpose tires or tracks. Severe-duty or solid rubber tires can provide extended life in abrasive environments. Fitzgerald explains these tires can cost $800 to $900 per tire. “So you are looking at spending $3,200 to $3,600 per set of tires. But your cost per hour may be less by spending more on the tire than buying a cheaper tire and having to replace it more frequently.” A lot depends on downtime. Flat tires can be very expensive if you have a crew waiting for a machine or factor in lost productivity.
“Tracks and the undercarriage for a compact track loader can make up 15% to 20% of the total operational costs of the loader, depending upon the manufacturer,” says Wright. “This cost can be managed and reduced if the operator cares for and maintains the undercarriage and is well trained on application management and proper operation of the loader.”
Of course track life varies by application. “The average that I see across the nation for general purpose, general use machines, the tracks are going to last between 1,200 and 1,600 hours on average,” says Fitzgerald. “If you are working on hard ground, you are probably going to have track life in the 800 to 1,200 hour range.” If you are working on concrete or asphalt a lot, you may be in the 400 to 800 hour range. If you use the loader sctrictly for moving dirt, you may get in excess of 2,000 hours.
“The life span on a set of tracks is dependent on three factors: operation of the machine, the types of ground the machine is operated on, and proper track tensioning and carriage maintenance,” Moore explains. “When a track loader is closely monitored for its proper operation in clean soil conditions, one may possibly reach 2,000 hours on a new set of OEM tracks. On the reverse, a set of tracks can be damaged and worn down in a matter of several hundred hours with mis-operation and non-recommended application use. It has been said that a new set of tracks can be ‘estimated for track life 2 1/2 times’ the typical life of tires on a skid loader in the same application use.”
Moore adds, “As with operation with tracks, life of tires in applications is very dependent on the surface conditions as well as the amount of ‘skid steering.’ Flotation, lug-style tires will not last as long as severe-duty tires. Some tires could wear in as little as several hundred hours while others could exceed 1,000 hours.”
But there are guidelines based on past experience. “Tires, general purpose machines out in the industry are going to be in the 600 hour range,” says Fitzgerald. “We do have owner/operators, dirt work guys, who will push that to 800 to 1,200 hours on a set of tires.” Skid steers with general purpose tires that work next to milling machines may see tire life as short as 100 hours.
“The typical life span for tracks is hard to determine,” says Wright. “Given the level of and experience of an operator, the life span can improve dramatically. Everything being equal, tracks working in gravel and hard pack conditions would last about half as long as tracks working in soft, loamy material. The same factors and conditions affect the life span of tires as they do for a compact track loader.”
But the operator is really the largest variable in operating costs. “I have gotten 3,000 or 4,000 hours on my tracks,” claims Aldous. “It is all about who is running that machine and who takes care of it. I have been doing this my whole life. If you watch me run my machines you are not going to see me spin it around on itself. With the track machine, if I have to work on sharp ABN rock, I will make gradual turns. A lot of guys don’t realize that if you get on that sharp rock it is easy to cut the tracks. Keep a smooth path when loading trucks. I think the track life all has to do with the operator.”
Aldous realizes the benefits of extending track life through careful operation. “I had one of the first Bobcat 337 excavators that came out. I had to put two new tracks and all new rollers underneath. It cost me ten rollers, and the rollers are $360 a piece. It was $3,600 plus the tracks. I was into the thing for $9,000.” So extending track life can dramatically lower your operating cost per hour on a rubber track machine.
The difference in operating costs between tracks and tires is in the replacement costs. “Tracks can cost two to three times more than tires,” says Wright. “While the skid-steer loader is less expensive to purchase, the compact track loader is usually more cost effective. Because compact track loaders perform using the same attachments and applications as a skid steer, the most distinct advantage a compact track loader has is its superior maneuverability in adverse ground conditions. Compact track loaders provide exceptional operation in muddy or snowy conditions where skid steers would not be able to work at all. The operating costs of a compact track loader are marginally higher than that of a skid steer, however most compact track loaders will give you added productivity and versatility, which means more for your money. Costs can be minimized with proper operation and machine maintenance. A typical compact track loader pays for itself in approximately 18 months. If maintained properly, compact track loaders will pay for their up-keep as well.”