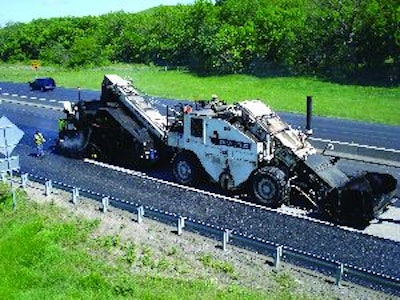
The Challenge:
Pave two lanes and the outside shoulder on a 16-mile stretch of interstate using an Ultra-Thin Bonded Wearing Course in 14 days.
The Players:
Shilling Construction Co. Inc.
Kansas Turnpike Authority (KTA)
The Process:
Shilling Construction Co. Inc. was tasked with laying down 96 lane miles of Ultra-Thin Bonded Wearing Course in just 14 days in the spring of 2010 on Interstate 35 in Chase County, KS. The $3.4-million projects was for the Kansas Turnpike Authority. The KTA required that the contractor only close down work zones for five-mile stretches at a time. "We place the Ultra-Thin Bonded Wearing Course to preserve what we have," says Mark Roberts, KTA overlay inspector. "The ultra-thin reduces the amount of mist and overspray that you get from trucks and traffic. And in the winter time, the ultra-thin bonding will hold salt in the surface a little bit longer than a conventional pavement will. So it gives us a better driving surface in the winter also."
The contractor used two special high-production Roadtec SP-200 pavers to pave the two lanes and outside shoulder on the 16-mile stretch. The pavers sprayed a tack coat of polymer-modified emulsion directly in front of the screed at a rate of .19 gallons per square yard. The hot mix asphalt used a PG70-28 binder and went down at 5/8-inch thick. The gap-graded mix contained a minimal amount of 0.75-inch top-size aggregate and some sand.
"We moved along at 60 to 75 feet per minute on average," said Travis Shilling, project manager for Shilling Construction Co. Inc., Manhattan, KS. "And there were times when we were paving 100 feet per minute." A conventional asphalt paver moves at about 25 to 40 feet per minute.
The Roadtec SP-200 spray pavers feature gravity flow to carry the hot mix from the 11-ton hopper directly onto the augers. For the Kansas project, a Roadtec SB2500 Shuttle Buggy fed one paver while a modified Barber Greene MTV3500 transferred hot mix to the other paver.
Shilling started one of the Roadtec SP-200 pavers on the north end of the project and the other on the opposite side at the south end. The contractor paved the 12.5-foot-wide passing lanes first. When that was finished on both sides, Shilling put the pavers in echelon, running with traffic, to pave the shoulder and driving lane. The shoulder paver took the lead and the driving lane paver followed.
Two steel-wheeled rollers, operating in static mode, compacted the pavement behind each paver. One roller worked in the breakdown mode, and the other handled finish rolling.
An Astec Double Barrel portable plant on-site produced hot mix at about 300 tons per hour on average, Shilling said. With two pavers working on site, Shilling says they were able to finish the job about 25% faster than with just one paver.