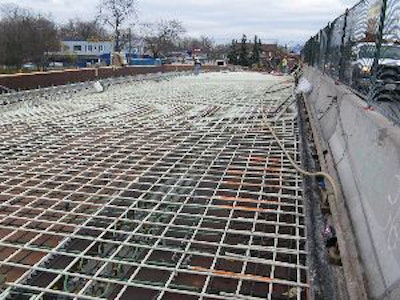
The Challenge:
Replace the complete bridge deck, side walks and steel railings economically while keeping in mind environmental factors that affect the materials.
The Players:
Schöck Canada
Total Bridge Services Inc.
Rankin Construction Inc.
ELLIS Engineering Inc.
The Process:
The City of Niagara Falls conducted a 4 million dollar project on the Weightman Bridge which crosses the Welland River along Portage Road in 2010. The bridge consists of two approach spans made of concrete slabs on steel girders and a central pre-stressed concrete girder navigational span. The project included replacement of the complete bridge deck, the side walks and the steel railings. The deck joints of the existing bridge were replaced by continuously reinforced flexible links.
Heavy daily traffic crossing the four-lane bridge and numerous frost-thaw cycles in the winters had taken their toll on the bridge deck and side walk slabs, which showed extensive damage due to corrosion of the steel rebar
The three-span Weightman Bridge is located along Portage Road in Niagara Falls, Ontario. It is 319.88 feet (97.5 meters) long and 61.68 feet (18.8 meters) wide. The bridge superstructure is a classical slab-on-girder system. The substructure is formed by two outer spans - each consisting of six large steel girders - which cantilever beyond the two piers in order to support a central pre-cast concrete segment. The steel girders are nearly 141.08 feet (43 meters) long, extending about 29.53 feet (9 meters) beyond the piers. The shallow central section is about 39.7 feet (12.1 meters) long. It allows for limited navigation underneath the bridge. Flexible links at each end of the pre-cast section allow for the transfer of vertical loads while rotation within the link is still possible.
While the steel girders were deemed to be structurally sound, the central pre-cast section was also removed in the course of the rehabilitation. It was replaced by fourteen pre-cast, pre-stressed hollow core panels oriented along the axis of the bridge. The panels are 3.94 feet (1.2 meters) wide and only 15.75 inches (400 millimeters) high. Steel stirrups were installed in the top of the panels for connection of the cast-in-place deck slab.
The new deck was cast onto the hollow core planks in the central section and onto the steel beams along the two outer spans. The sidewalk slabs were then cast directly onto the deck slab. Finally, the new PL-2 concrete barrier walls are cast onto the sidewalk slabs.
Schock ComBAR, a new generation of glass fiber reinforced polymer (GFRP) rebar, was used for the reconstruction of the bridge deck and the sidewalk slabs. The rebar was used to reinforce the top layers of the deck and sidewalk slabs while the bottom layers used carbon steel rebar reinforcement. Total Bridge Services Inc. (TBSI) installed the rebar.
The Weightman Bridge project was executed in two stages to minimise disruption of city traffic in Niagara Falls. In stage one, the right, western half of the bridge was closed. Both directions of traffic were then redirected onto the left-hand side of the bridge. In stage two, traffic was diverted onto the new deck while the east side of the bridge was rehabilitated. This construction schedule required splicing the transverse reinforcement in the deck along the centre line of the bridge. In order to do this, Schöck and TBSI developed a new technology using GFRP bars glued into corrugated polyester tube sleeves.
In stage one, pieces of 25.59 inches (650 millimeters) long corrugated PE tube with an interior diameter of .71 inches (18 millimeters) were installed in the deck along the border between the two phases. In stage two, ComBAR bars with a core diameter of 16mm were inserted and glued into these tubes using an epoxy-based adhesive.
Unlike steel, FRPs cannot be bent once they have hardened. To alleviate the resulting problems in the concrete structure, straight ComBAR bars with end heads were used wherever possible in the design of the Weightman Bridge when bent epoxy- coated bars were replaced. At the abutments, the longitudinal bars at the top were provided with end heads, as were the vertical bars at the center of the abutment end beam. To provide closure in the system of load vectors, a short section of bent bar was placed at each intersection of these headed bars.