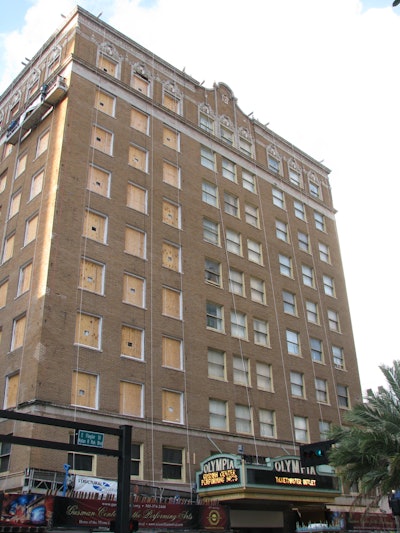
The Challenge:
Install a new support system and restore severely damaged sections of the historic Olympia Theater in Florida.
The Players:
City of Miami
Miami Parking Authority
R.J. Heisenbottle Architects, P.A. (RJHA)
Wiss, Janney, Elstner Associates, Inc. (WJE)
Helifix, Inc.
STRUCTURAL
The Process:
The Olympia Theater and Apartment Building has been around since 1926 and became a historic landmark in 1984. Its years of existence wore on the building, though, and the 10-story high-rise complex found itself facing structural and safety issues on its exterior brick masonry cladding and terra cotta façade. If an emergency and long-term repair solution could not be found, the building would have to be torn down and rebuilt.
The City of Miami and Miami Parking Authority enlisted R.J. Heisenbottle Architects, P.A. (RJHA) to head the building's restoration effort. RJHA enlisted structural engineers from Wiss, Janney, Elstner Associates, Inc. (WJE) to conduct an onsite assessment in October 2009. WJE and Helifix, Inc. decided to use the Helibeam System from Helifix as a supplementary and sustainable lateral and gravity support system for the distressed veneer.
The original building is comprised of a steel-framed structure with clay tile infill supported on the steel spandrel beams. The brick and terra cotta veneer was unsupported within the piers but supported over the punched window openings by steel lintels anchored to the spandrel beams.
The Helibeam System would offer a non-invasive and sustainable solution comprised of HeliBars, HeliBond, DryFix remedial ties, and Crack Stitching. The key focus of this system was installing 22.97-foot-long stainless steel (austenitic grade 304 or 316) HeliBars to create a reinforced "beam" across each spandrel level to distribute and support the structural loads across the piers and into the steel lintels and spandrel beams. "The Helibeam System is fully concealed (once installed) and its flexibility allows it to be bent around corners with no loss of performance," says WJE Associate Principal Brett Laureys. "With all work undertaken externally, there was minimal disruption to the upper floor tenants during this 'emergency restoration' phase."
Specialty repair contractor STRUTURAL worked with Helifix's on-site quality control and assurance support team to install the Helibeam System. During installation, 1 ¾-inch-deep slots were cut in the mortar joints, vacuumed and then flushed out with water. The contractor laid a bead of thixotropic cementitious HeliBond grout, placed the HeliBar in the slot, and then placed another layer of grout on top. This created a deep masonry beam to distribute the structural load and provided gravitational support around the entire building. The HeliBar overlapped by 1.5 feet at the ends to create one monolithic run around the building. The recessed Helibeam was pointed over the top to render it virtually transparent to the naked eye upon completion. DryFix remedial ties were used in tandem for lateral restraint in the façade. The ties were power-driven into position using a small pilot hole and special installation tool that leaves the end of the tie recessed below the outer face. Crack Stitching secured local cracking and stabilized any further movement of separating brick areas.
The Helibeam System installation was completed in August 2010. Now that stabilization is complete, restoration of the façade and repair/replacement of the terra cotta tile can be done. The final phase is expected to be completed in 2011.