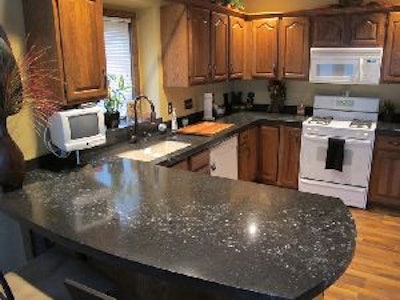
When Matt Carr, owner of Allegheny Cement Studio in Pittsburg, Pa., first met with a new residential client, the contractor had to start from scratch. The customers knew they wanted a concrete countertop, but they had no idea what they wanted it to look like.
So Carr created some samples for the homeowner using the terracotta color they originally thought they wanted. After the first set of samples, the homeowner was still not 100 percent sure of what they wanted. It was then that Carr and the homeowners came up with the idea of a black concrete countertop incorporating recycled amber glass and the couples' wedding crystal.
After creating a few new samples Carr was ready to start the 2-inch-thick, 60-square-foot countertop. The countertop was created in two parts with the only seam running down the center of the sink. After templating, Carr began the precast process back at his shop. First, he had to find the best method from breaking the approximate 15 pounds of crystal - vases, dishes, serving plates, candelabras, etc. - being added to the countertop. Manually crushing the crystal turned out to be the best option to get the broken crystal the right size. For the amber glass, Carr used beer bottles and amber Pyrex bakeware crushed with a tamper.
On two 11-feet by 6-feet box tables, Carr formed and cast the countertop. Carr hand sanded a ½-inch foam board cut out which he placed in the form for the countertop's drain board. The drain board also included two rails for a cutting board to sit on. Carr used ½-inch by ½-inch square plastic to create the void for the rails.
Before placing the concrete, Carr strategically laid out the broken crystal in the forms. When finished, the crystal would run like a river from the countertop's peninsula, across the sink and up the backsplash. Carr had to be careful not to move the crystal while placing the concrete.
Carr added 9 gauge ladder wire reinforcement before mixing up the portland cement, amber glass, black integral color and a few additives for the mix. He mixed the concrete in a 7-cubic-yard mortar mixer, poured it into a wheelbarrow to transport it to the forms and then placed the concrete by hand. It took four total batches to finish the countertop, Carr says.
Once placed, the concrete countertop was covered with plastic and a heating blanket and cured for two days. Carr then ground and polished the bottom of the countertop before stripping the forms and turning it over. Using a 7-inch wet angle grinder and diamond embedded hand pads, Carr polished the countertop starting with a 50-grit resin bonded pad moving all the way up to a 400-grit resin bonded pad.
In between polishing pads, Carr would mix up and hand apply a slurry coat to fill any voids before continuing the polishing process. He says he applied four slurry coats during the polishing process.
After air drying for two days, Carr applied three coats of a solvent and chemical free densifier and used a burnishing pad and a torch to heat and burnish each application of densifier. Finally, he finished by applying three coats of an acrylic sealer which left the concrete countertop with a gloss finish.