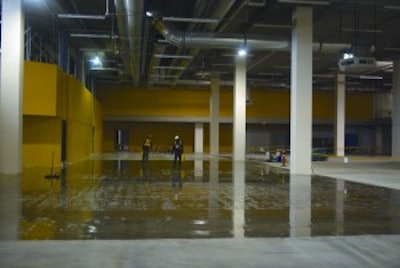
Concrete contractors are no strangers to project changes. Advance Construction, Vancouver, B.C., recently was tasked with the job of turning two purpose built slabs specified for vinyl tile into densified, light reflecting concrete floors. To add to the challenge, the two concrete slabs were both suspended requiring Advance Construction to be careful about materials leaking into finished areas below the surfaces.
The job was for a new big box store, says Jamie Gordy, owner of Advance Construction. The concrete slab was originally built to have a vinyl tile covering, but the tenant wanted light reflecting concrete. The job was to be done on two levels, with an underground parking structure located below the lower concrete slab, Gordy says.
The 125,000-square-foot project took Gordy and his flex crew of 10 to 12 employees three months to complete. Of those employees, Gordy had a crew of three dedicated employees for surface prep and repair. To accommodate the other trades working in the building at the same time, Advance Construction was given blocks of area to work in. The blocks were usually 40,000-square-foot increments, Gordy says.
The crew started by removing the super plasticizer left over from slab placement. It then used an environmentally friendly citrus-based cleaner and floor screens to clean the concrete and a ride-on scrubber to finish the wash. There was also a significant amount of repair work that needed to be done, including patching over 150 core test holes, Gordy says.
"Because we couldn't apply a great deal of water to the floor (to keep water from draining to the levels below the concrete slabs) we needed products with low foot prints in water-based solutions," Gordy says. So Gordy chose Lythic Solutions' Lythic HardWear Floor System because it would work without the copious amounts of water required for sodium silicate densifying. Lythic chemistry is refined from sodium silicate, making engineered silica that bonds to the slab to increase durability and eliminate dusting.
To start, Gordy and his crew used a 25-gallon, dolly-mounted pump sprayer to spray apply the Lythic Densifier, diluted from concentrate. This was followed by an application of the larger particle sized Lythic XL Densifier. Coverage was 500 square feet per gallon for each application. After drying, the slab was cleaned with an auto scrubber and burnished to a light reflective shine. Lythic Protector was then applied at 1,500 square feet per gallon and the floor was high speed burnished to a final light reflective shine.