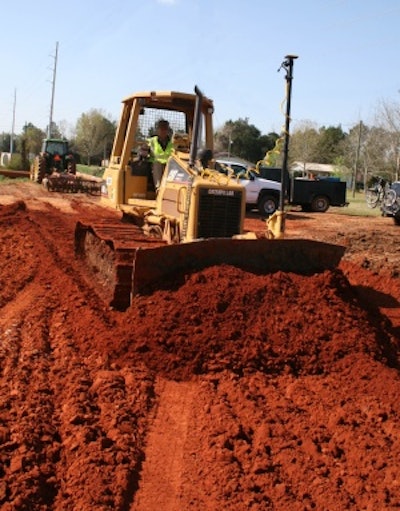
There is a lot to be said for memberships in industry organizations. Through groups such as the Associated General Contractors, Construction Owners Association of America and Associated Specialty Contractors, to name a few, construction professionals can network with their peers, learn about new or changing legislation and, perhaps most importantly, keep abreast of technology as it is introduced or evolving.
For John Walton, owner of Mobile, AL-based John G. Walton Construction Company, speaking with colleagues at an AGC national function played a pivotal role in his company's move to add GPS capability to its operation. Today, as the company tackles a southeast Alabama road widening project, the effects of that meeting are evident in a dozer and excavator -- both of which now run Topcon machine control systems accessing a reference control network. Adding that capability, Walton says, has paid dividends from day one and continues to do so as the job progresses.
Heading for the Coast
State Road 181, along with US 98 located a few miles to the west, are two of southwest Alabama's major access roads from Interstate 10 to the south Alabama coast. As US 98 has become increasingly congested, efforts are being taken to upgrade SR 181 and offer a good alternative for travel. The widening facet of the job is being handled by John Walton Construction Company (JWC) working as a sub to Mobile Asphalt.
According to Josh McElhenny, JWC's project manager, the project is being let in segments, with their firm landing the first stretch in Daphne. "We are widening four miles of 181 and doing it in kind of a different way," he says. "Where most jobs would call for us to totally remove the old road and lay down a new four-lane, ALDOT (Alabama Department of Transportation) is having us keep the existing road and add to it on each side. It's different but we're okay with that."
The $11.8 million project started in June of 2009 with selective clearing and grubbing, removal of sidewalks, driveways, curbs and gutters, and then moved on to upgrades in drainage and construction of the additional lanes.
In the past, a project like SR 181 would have been heavily laden with stakes, reflecting JWC's reliance upon traditional surveying techniques to get the job done. Today, those stakes are few and far between, the result of John Walton's AGC meeting experience a couple years back.
"I was talking with other contractors... and was asked what GPS we were using," he says. "The answer, of course, was that we weren't using it at all. At the time, I knew the technology was out there; I guess I didn't think it was as widely used as it was. Immediately after returning from that meeting, we started researching GPS and machine control for our operation and, having chosen Topcon, contacted Earl Dudley, our area Topcon dealer."
JWC purchased a HiPer Lite+ base and rover and became Dudley's first contractor in the area to be running 3D-MC2 machine control on its Cat D5G. The impact on the operation was immediate and substantial.
"I have done most of our jobs before without the MC2 and the difference is huge," says Dwayne Anderson, JWC's operator. "In the past, we would have to call in a surveying engineer to lay it out, line it up, hub it, flag it, offset it and so on. With this system, I just show up, check out my machine, get my GNSS ready, plug it in, dial it in, get my radio links and I'm ready to go. On this job, it's really been a plus, especially in grading all the ditches and other cut sections. Because it does all the layout work for us, we are not setting stakes every fifty feet. That's been outstanding."
Getting Connected
There's no denying that MC2 was a vast improvement over the way JWC had been working. However, when the company first took delivery of the system, it quickly learned that even the best technology can be stymied -- in this case, by Mother Nature.
"This part of Alabama, especially in summer, is prone to afternoon thunderstorms," says McElhenny. "So, on a project we were working across the bay, when the storms would move in, our signal from the base station would degrade and production would suffer. About that same time, people from Earl Dudley had been talking to us about getting onto their reference network. We did, and we've never had an issue with signal strength or quality again."
Earl Dudley's network, called iNET, provides internet-based network GPS RTK service across Georgia, Alabama, Tennessee, and Mississippi. The network provides subscribers like JWC with network corrections that include data from both the US Navstar and Russian Glonass satellite systems.
"John Walton's operation was actually a beta test site for the latest version of the software for the iNet network," says Tony Ozimek, Dudley's regional sales manager. "What makes our network unique is that we are pulling signals in from five towers in the area and running a VRS correction. By doing so, we are coming up with a better solution for our subscribers, and that ultimately improves their operation."
Never Move Dirt Twice
Throughout its 20+ years in business, one of the issues that had periodically plagued JWC had been the tendency to either overcut or undercut large sections when excavating, thereby violating the basic earthmoving tenet: "never move dirt twice." That problem was resolved with the addition of a machine control system for its Komatsu PC 200LC, says Ozimek.
"In their earthmoving projects, Walton would work solely off grade stakes and it was not uncommon for them to have an area where they'd be a foot and a half too high or too low," he says. "When that would happen, they'd have to stop the operation, bring in a dozer, clean up the high or low area that they couldn't push with the excavator, then go back to the cut. We showed them that Topcon's X63 machine control system could get their digs to within a tenth -- the first time -- and they were impressed. In fact, we offered to let them try it for seven days; after just two days, they made the purchase."
The combination of both machine control systems and the added accuracy of the network has helped JWC keep the SR 181 project moving along at a nice clip, according to Austin Harvill, the company's project superintendent,
"On this job, ALDOT specs are calling for 18 inches of base to go down first," he says. "The excavator is set to cut in at a -2.7, then the dozer comes behind and has to place material in 8-inch lifts. So we have it broken down into 8-inch increments and dialed in on the dozer until we get to actual subgrade of -1.2. That ensures us a nice consistent 8-inch layer throughout each lift which is then rolled and compacted."
Without that control, he says, they would be working off a line of grade stakes placed along the side of the road. The need to set stakes then reset them when they were knocked over would tie up three men for a day. All that, says Harvill, is pretty much a thing of the past now.
"It's hard to say how much faster we are now, but it has to be in the neighborhood of 30%," he says. "We've eliminated the need for a superintendent to do the layout and figure elevations, as well as two guys setting the hubs and another one doing stakes. Now those workers can be down at the other end of the job doing other work. Couple that with the added accuracy and it's easy to see why we're happy we made the switch."