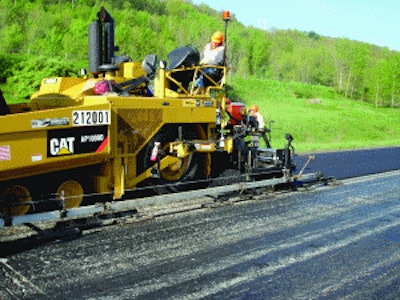
As a third-generation, family-owned business with headquarters just off I-88 between Albany and Binghamton, Lancaster Development has lots of experience doing pavement rehabilitation.
However, Mark Galasso, who now runs the company along with brother, Martin, Jr. (Marty), had not always been totally satisfied with the results obtained on their highway projects.
"Marty and I have high expectations," notes Mark, "and from our standpoint, we have had too much variability. We just weren't consistent with smoothness."
The 2009 project called for performing pavement rehabilitation on approximately 24 lane miles of I-88 Portland Cement Concrete (PCC) between Unadilla and Bainbridge, NY.
It included crack and seat work on the westbound lanes, followed by four lifts of Superpave HMA on the westbound lanes, and a final wearing surface on the eastbound lanes that had had three lifts completed in 2008. In total, approximately 92,000 tons of Superpave were required to complete the 2009 portion of the project.
Setting a higher smoothness target
In March 2009, the Galassos, along with equipment manager Charlie Goodwin, met with their Milton CAT representative Mike Courchaine and a project consultant from the team formed by Caterpillar Paving Products and Seatech Publications.
In that meeting, the Galasso brothers laid out the I-88 project parameters and emphasized their firm commitment to improved smoothness results as measured by the New York Department of Transportation (NYDOT) Pavement Ride Quality (PRQ) Adjustment Level 1.
The PRQ Adjustment Level 1 is a metric specification based on the International Roughness Index (IRI) and applies to projects with three or more opportunities for smoothness improvement.
On previous NYDOT projects with the Level 1 specification, Lancaster achieved IRI scores that averaged in the 0.86 - 1.10 m/km ranges and earned a small percentage of the available quality units.
During the meeting, the Lancaster management team and the consultant looked at the IRI results of multiple lift projects from across North America and discussed ways to improve their rideability scores.
Eventually, an agreement was reached to have the consulting team assist on the I-88 project and be responsible for directing the process to achieve an average IRI of less than 0.80 m/km on the westbound lanes.
Bringing back the contact ski
One of the first steps taken by Lancaster was to bring out of storage, at the request of the consultants, their 30-foot multi-articulated averaging skis. Bob Scalaro, I-88 paving superintendent, was skeptical at first.
"In the past we've used the drag ski, but there were times we had problems using them as reference for sonic sensors," Scalaro explains. "Nowadays we have standardized on the non-contact ski. They are more convenient and take less maintenance."
On the I-88 project, however, the higher degree of averaging provided by the multi-articulated contact ski would be needed to build smoothness on the patched, crack-seated PCC surface.
"The consultants taught us a lot about installing the contact ski and the grade sensor," Scalaro continues. "Probably the biggest point was making sure that the reference string was at least four inches above the body of the ski when we use a sonic grade sensor."
The entire paving crew took part in the on-the-job training on the use of averaging skis, and the grade and slope control system prior to the start of the first lift, a 25 mm truing and leveling lift. In particular, the crew learned how to check the settings in the Topcon control boxes and to conduct the performance test to verify correct tow point valve operation.
New truck exchange procedure
Another big step was changing the truck exchange procedure used by Lancaster crews. "We had been taught a long time ago that stopping the paver between trucks caused screed settlement bumps," says Scalaro. "So, what we try to do is slow the paver to a crawl, get the empty truck out of the way, and pick up the next truck on the fly."
The "on-the-fly" truck exchange was taught in paving seminars at least into the early 1990s. However, recent research has shown that trying to keep the paver moving between trucks has several potential problems.
The main issue is running low on mix in the conveyors and losing the head of material in the auger chamber. The screed dropping in reaction to low head of material is much more harmful to smoothness than short paver stops. Plus, with a lot mixes, the likelihood of repeat, end-of-load segregation increases when the hopper is run empty and hopper wings are cycled late in the exchange process.
New procedures implemented on the project include:
- Release the truck when it is empty, allowing the truck to pull away without dragging mix from the hopper. Continue paving at the normal speed as the old truck departs and the new truck starts to back in.
- Slowly cycle the hopper wings and stop the paver with the conveyors full and the hopper deck still covered. Lower the hopper wings and wait.
- Stop the new truck just short of the push rollers; slowly move the paver forward to contact the rear tires; trip the tailgate and raise the truck bed.
- Push the propel lever forward and let the paver ramp back up to paving speed.
Old habits can be hard to break, but the paver operator and dump man had no problems conforming to the new truck exchange procedure. The truck exchange time ran from 60 to 90 seconds.
"There was no deep settlement mark left by the screed," Scalaro says. "And, we all saw that the feeder system ran more smoothly as a result of stopping. Finally, we saw that end-of-load segregation was minimized."
Balancing production
Another step used by to improve smoothness was to calculate and enforce paving speeds. The goals are to consume the mix as it arrives in front of the paver in a consistent manner, and to have no paver stops in excess of five minutes.
The tendency among crews is to speed up when there are multiple trucks in front of the paver, and to slow down when there is just one truck left in front of the paver. That common reaction, however, poses a problem - varying the paving speed affects the screed height and, more importantly, affects the flow of mix through the paver and the head of material in front of the screed. A consistent paving speed is a fundamental aspect of paving for smoothness.
The second lift, the 2.5-inch binder, serves as an example of calculations done on I-88. On June 10 of the project, approximately 2,750 tons were laid down in 10 hours.
Based on 275 tph delivered in front of the paver, paving width of 16.3 feet and loose paving depth of 3.25 inches, the calculated paving speed was 24 fpm.
The operator stayed with that speed; increasing to 30 fpm twice when more than three trucks were in front of the paver. The longest paver stop was 14 minutes waiting for trucks. All other stops were under three minutes.
For the entire shift, paving efficiency (time paving compared to truck exchanges and other stops) was 80%. Acceptable efficiency when truck exchange paving is 75%.
"The paving speeds that were provided by the consultants using the Caterpillar Production Calculator were slower than our usual ones, but what was interesting to all of us was that at the end, hourly production and daily production did not decrease," Mark Galasso says. "We were just more efficient and there was less waiting time."
Another benefit of a slower paving speed was that the crew made fewer mistakes. The slower pace brought more control to the job. With more time to react and look ahead, the crew appeared much more organized.
Timing the tender zone
After the T&L lift, there were three more lifts:
- 65 mm Binder, 60 Series 25 mm Superpave
- 50 mm Binder, 50 Series 19 mm Superpave
- 40 mm Top, 50 Series 9.5 mm Superpave
Each mix displayed a distinct tender zone that commenced around 250 degrees F and persisted until around 190 degrees F. Any time either of two steel drum compactors entered the tender zone, the mat would shove under the drums and roll away from the drum edges. Not only does mat deformation cause low-density issues, it causes roughness in the mat that will increase IRI scores.
To help the roller operators stay out of the tender zone, three elements must be managed. First, the calculated paving speed must be maintained so the breakdown roller can run a consistent pattern that stays ahead of the tenderness.
Second, the breakdown compactor working speed must be calculated based on drum width, mat width, vibratory frequency and impact spacing to determine if the compactor can match paving production.
Third, a cooling curve should be generated to determine how much time is available before tenderness starts. To generate the cooling curve, the consultants used software titled, PaveCool version 2.400 that is available from the Minnesota DOT.
Returning to the 65 mm binder laid on June 10, following are the data used to create the cooling curve:
- Mix temperature under the screed, 300 degrees F
- Mix type, coarse-graded Superpave
- AC PG, 64-22
- Uncompacted layer thickness, 3.25 inches
- Ambient temperature at 7:30, 68 degrees F
- Base, HMA
- Base temperature, 68 degrees F
Under those conditions, there are 12 minutes of breakdown compaction opportunity before the onset of tenderness in the 60 Series Superpave.
The breakdown compactor, a Cat CB534D XW with 79-inch drums and operating at 220 fpm (11.5 impacts per foot) set in high amplitude/low frequency, used a 9-pass pattern to develop 92-93% of maximum theoretical density.
The time of breakdown compaction was just over 10 minutes for a +200-foot long panel. The breakdown compactor was able stay ahead of the tender zone and get target density for that phase. The intermediate phase was 30 minutes behind the breakdown phase to allow the mat tenderness to cease.
For the 50 Series binder and top lifts, the lift thicknesses were thinner. Consequently, the mat cooled faster and the breakdown time window decreased. However, since the mats were thinner, it took two fewer vibratory passes to reach target density. The new calculations proved that the selected compactor could match production and stay ahead of the tender zone.
"In the past, we've had problems getting consistent density with the 50 Series. It's really a stiff mix with that big tender zone," Scalaro notes. "That's when I realized that I need to start using the production calculator and the cooling curve to get more precise control of operations."
Building smoothness lift by lift
The crew responded well to the training and operational recommendations for each lift and they controlled the elements that support smoothness in paving:
- They paved at a consistent, calculated paving speed.
- They set up grade and slope correctly for each application.
The crew also got clear communications and support from the owners and from on-site supervision. Mark Galasso was at the I-88 project a lot and he noticed an attitude shift.
"The crew is more enthusiastic and seems to be a lot more confident and relaxed," he states. "We've been sharing the consultants' reports with the crew, so, and they're getting feedback on what's going well and what needs improvement."
So, was it worth the investment in consulting time and crew training?
Remember, the estimated IRI of the patched and crack seated PCC surface was 3.0 m/km. The goal was to average under 0.8 m/km or at least 74% improvement.
Lancaster Development hired their testing service to measure the westbound driving lane and passing lane after the second binder lift. The average IRI for both lanes was 1.01 m/km for a ride improvement of 66%. Therefore, the crew knew they were on track to meet the target set by the consultants and to have their own best crew results on I-88.
The final IRI numbers confirmed that the Lancaster crew did a great job improving smoothness on a tricky pavement rehabilitation project. The passing lane (paved first) averaged 0.74 m/km. The driving lane (paved second) averaged 0.71 m/km. These IRI scores represented another 28% improvement. The westbound lanes earned 45.4% of the total possible ride quality bonus.
Mark Galasso's e-mail to Lancaster personnel who worked on the 2009 I-88 pavement rehabilitation project summed it up best: "This represents our best results ever under this specification. Great job!"
Information provided by Seatech Publications Inc., Poulsbo, WA, and Caterpillar Paving Products, Minneapolis, MN.