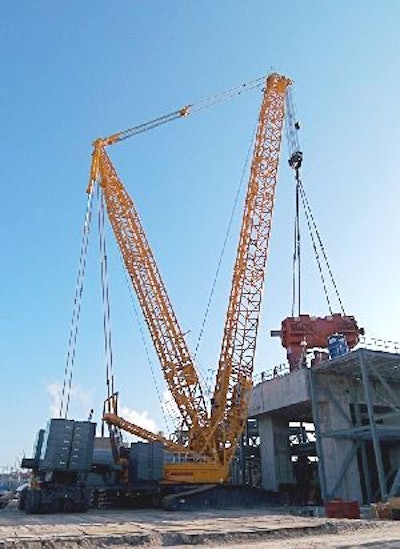
Over the past 10 years Buckner Companies, based in Graham, NC, has developed what is now North America's largest fleet of Liebherr crawler cranes to enhance its position as a leading heavy lift specialist. At the heart of its inventory of 80+ cranes are 13 Liebherr LR 1400/2s rated at a 440-ton capacity, as well LR 1350 and 830-ton-capacity LR 1750 models.
Now, Buckner is adding an initial four units of the new Liebherr LR 1600/2 lattice-boom crawler cranes rated at 660 tons, with the likelihood of more to follow. The first two models were delivered in fall of 2009. The third unit is scheduled for delivery in the third quarter of this year, with the fourth unit arriving in the first quarter of 2011.
"Our intention is that these four units are just the beginning," says Doug Williams, president of Buckner Companies. "We anticipate adding more in due course. Our first units have already proven themselves on power projects using full components of derrick, ballast wagon and luffing jib."
Targeted for Energy Installations
While the 440-ton class of crane continues to be popular, demand is also growing for the 660-ton class. "With all the power work coming up -- conventional, nuclear and wind -- this size of crane is becoming more the norm," says Williams.
Butch Robertson, Buckner's project manager for alternative energy, says, "The LR 1600/2 is going to be the crane of the future for the wind industry to erect masts up to 328 ft. high. We can set the 2.4MW Mitsubishi turbines that are becoming very popular without derrick or ballast wagon. This makes it much easier to move between turbine sites on a wind farm and will be up to 20% quicker than other 660-ton cranes."
"The LR 1600/2 has the perfect balance of capacity vs. ease of transportation and assembly," Williams states. "They are the perfect crane for erecting the latest generation of taller and heavier wind turbines. With other 660-ton cranes on the market, you generally have to fit a derrick mast to lift the larger wind turbines. But with the LR 1600/2, we can do windmills without a derrick and with far less ground bearing pressure."
Buckner has opted for the 79-in.-wide (2 meter) crawler tracks rather than the industry standard of 59 in. (1.5 meters). This reduces ground bearing pressure, which saves time and money in ground preparation and matting, not only to do the lift but also to move between lifts. In many instances, the LR1600/2 has less ground bearing pressure than the LR 1400, Williams says.
The LR 1600/2 offers a maximum tip height of 630 ft., which is reached with a 315-ft. main boom and a 315-ft. luffing jib, in conjunction with the derrick system. Buckner has also opted for the hydraulically adjustable ballast trailer, which can be adjusted -- even under full load -- from a roughly 43-ft. radius for a more compact footprint where space on site is an issue, to 59-ft. radius for even greater capacities.
Proof is in the Performance
Buckner's first unit was put straight to work in Loxahatchee, FL, for Zachry Industrial to upgrade a Florida Power & Light gas turbine plant. The crane began the project with 276 ft. of main boom, with derrick and full ballast wagon (SDBW configuration) to set the 22 heat recovery steam generator (HRSG) modules weighing up to 479,000 lbs. The boom was then shortened to 197 ft. to set the 778,000-lb. steam turbine generator and combustion turbines.
Having completed work in Florida, this crane is now at the Stennis Space Center in Bay St. Louis, MS, where Beyel Bros. Inc. is setting the test cell for the new Ares I space rocket, which is set to be used in the upcoming NASA missions.
The second unit is on site in Fulton, AR, helping Babcock & Wilcox Construction build the new $1.3 billion, 600-MW John W Turk Jr. coal-fired power plant for American Electric Power (AEP). It is now six months into a 24-month project.
Buckner project manager Jerry Masten says that both units have really proven their value. "The LR 1600/2 has a capacity advantage over other cranes in its class. The finish is top notch and, from a maintenance standpoint, everything is laid out in a very common sense fashion. It has proven to be a very good machine, even beyond our expectation.
"One of the biggest advantages is the adjustability of the ballast wagon while there is a load on the hook. That has been great for the space constraints on power plants. We can pull the ballast wagon in and add more weight to it, maintaining capacity with a smaller footprint," Masten says.
He adds, "There is also the benefit of the Liebherr LICCON software, which is a step up from other lift planning software. It allows us to do lift planning in real time. We can quickly work out the boom length we need and simulate the lift. It also enables us to plan the ground bearing pressure, how best to spread the weight. It really saves a lot of time and is another big advantage of the Liebherrs to us."