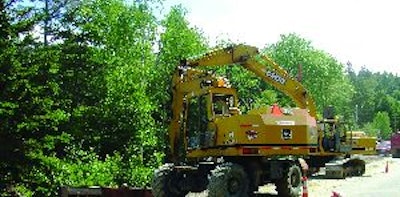
The Lane Construction Corp. ranks 52nd among the top 400 U.S. contractors. It is also the eighth largest transportation contractor and eighth largest domestic heavy contractor, according to Engineering News Record. It constructs highways, bridges, dams, mass transit and airport systems in 20 states.
"Lane Construction owns most of the equipment used on our contracts, and leases as required," notes John Irvine, director of communications. This includes 41 wheeled excavators.
"Lane Construction has a legacy of using rubber-tired excavators -- even when it was not as common," reports Robert Hoffman, director of the Mechanical Department. "Lane began with Gradall excavators in the 1960s and still uses them today. Even in the late 1970s, we used the Drott 40s. Today, as with most contractors, we have gravitated to the more common wheeled excavator. We currently use Volvo, John Deere, Gradall, Liebherr, Hitachi and Daewoo excavators. We have tried many brands and continue to try units that we may not have in the past -- we always keep an open mind to change."
The Lane Construction Corp. uses the machines for ditch work; placing material over barrier walls on roadway work; setting small structures/pipe/barrier; as a utility machine around concrete paving work; grading and placing rip-rap on slopes, etc.
"Being on wheels provides mobility and ease in getting around relatively level work sites, such as roadway, airport, commercial development sites, etc.," says Hoffman. "Additionally, some of our wheeled excavators are fitted with a dozing blade, which affords backfilling trenches when doing pipe work. This is a handy feature and typically something you don't have on a conventional track-type excavator.
"Their strengths are mobility and ease of travel from point A to point B on a jobsite, within a reasonable distance, under their own power," he continues. "And rubber tires are much more appropriate for working on paved surfaces vs. tracked machines, which typically damage pavements."
In comparing similar size machines (weight classes), the operating and performance characteristics are generally pretty similar in terms of lift capacity, arm force, dig depth, etc., says Hoffman. "Although, it's not to say that some weight classes may see the tracked excavators having some advantage in dig depth and arm force," he admits.
"One difference that does set the two machines apart is wheeled excavators are limited to working on fairly hard, smooth and level ground, while tracked excavators can also work on fairly rough and variable terrain and slopes (within reason)," notes Hoffman. "Additionally, wheeled excavators require outriggers to stabilize the machine when performing work."
Yet, both types see plenty of use on the company's projects. "Similar to our tracked excavators, our wheeled excavators generally see pretty high utilization," says Hoffman. "Their capabilities, versatility and mobility lend themselves to seeing good usage on our jobsites."
A NICHE BUSINESS
Chicago, IL-based Thornton Equipment currently owns 12 Gradall truck-mounted excavators, which are rented to other contractors with operators. These machines commonly perform road work, wetland mitigation, erosion control, stabilization and hazmat response.
Gradall excavators feature a unique design. The upper structure distributes forces across the undercarriage to provide a lifting chart that is limited by hydraulic power rather than machine stability.
"Unlike the conventional knuckleboom machines that lift much more over the front and rear than they do over the sides, all Gradall machines more evenly distribute the machine weight and load over all four wheel ends, providing a stable platform and better traction and flotation while lifting on rubber," says Bill Thomas, vice president of excavator marketing and sales. "In rare instances, a single set of optional outriggers or the grading blade can be used to remove machine stability concerns while working when maximum lift is required."
Thornton Equipment carved out a niche that keeps machines on the move. "A contractor will not want to invest in a big attachment for two days' work," says Jim Hering, owner. "That is where I live." The company performs anywhere from 75 to 100 jobs per month. The machines may be in a different spot every day. And Thornton Equipment invested in attachments to handle most jobs. "I have three telesticks, 10 boom extensions and 35 buckets that range from 18 in. to 7 ft. wide," says Hering.
This niche works well due to the nature of the machines. "The Gradall is more of a specialty machine," says Hering. "It is more of a finish machine than a backhoe-oriented unit. When everybody gets done making their mess, we come in and clean it up."
The machines have come in handy for ditching, sloping, working on sound walls along expressways, setting up barrier walls, backfilling sidewalks and curbs. "We dug a pond for the Army Corp. of Engineers," recalls Hering. "I have one setting up barriers on the Indiana toll road. I have one doing punch list work for the Indiana toll road. They are all working for different contractors."
This approach has proven successful in a down market. "We're not breaking any records, but our guys are busy," says Hering. "We work for a lot of contractors, so I make my schedule with a pencil and keep an eraser close because it changes so fast."
The truck-mounted Gradalls and skilled operators provide flexibility to operate in this fast-paced environment. "I wouldn't run them without my guy on them," adds Hering. A skilled operator makes a huge difference when it comes to wear and tear on the machine.
The 55-mph travel speeds make it possible for Thornton Equipment to quickly get to a jobsite on short notice. It also allows the units to frequently travel back to the shop for proper maintenance.
"I have to maintain the machine so it's operating 100% of the time," notes Hering. "If my machine goes down when I am renting it to somebody else, I have to get it back up right away. You have to be there when you say you are going to be there, do what you say you are going to do and have good people on the seat who really care about the customers. Preventive maintenance is pretty critical for us."
The company has rapidly expanded due to the capabilities of these wheeled excavators. "When I started out, I didn't have any idea that I would have this many machines," says Hering. "I just kept adding them because I needed to take care of the customers. Having this many machines was never in my plan."