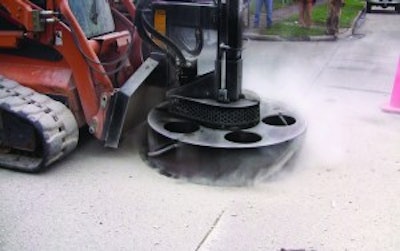
Some might think replacing a manhole casing, or lid, and bringing it up to grade is an easy job. But what about when you're replacing over 1,000 manhole casings?
FeeCorp Environmental Company did just that. The company replaced 1,033 sewer casings in Ironton, Ohio, so the city could mark its sanitary system. In addition, FeeCorp had to bring many of the casings up to grade with the road surface to eliminate any dips in the roads, says Ed Jones, FeeCorp's general manager of operations.
FeeCorp started the job in October 2009 and is scheduled for completion in September 2010. Aside from stopping for three weeks due to cold temperatures, FeeCorp worked the entire year on the job. "We averaged about 40 casings a week," Jones explains.
Jones says the project started on one side of town, on mostly asphalt surfaces, but the company was soon encountering concrete surfaces. The manhole leveling attachment system the company was using was having a tough time with the concrete, so FeeCorp crews tried different equipment including jackhammers and core saws to cut the concrete around the manhole casings. Unfortunately, those methods were not time efficient.
During a construction industry trade show in Louisville, Ky., Jones came across the new HS-57 Manhole Saw from Coneqtec/Universal. The HS-57 is designed to repair manhole casings by cutting through concrete or asphalt, attaching to the casing and lifting out both the casing and the cut pavement. Jones decided to test the HS-57 saw on the Ironton job.
After testing a demo model in April and offering feedback to the manufacturer, Jones had a revamped model on site in May. It worked very well, he says. "It is set up on the same principle as a planer. The HS-57 uses cutting teeth. You set the saw over the top of the existing casing and lock it in place, start the saw and saw through the surface of the road. When you reach the gravel base you're able to pick up the casing and the concrete and remove it," he explains.
Using the hydraulically driven saw attached to a compact track loader, Jones and the FeeCorp crew were able to easily cut through the concrete and remove manhole casings. "This saw is great for raising and repairing casings," Jones says. "One man can use this saw to do the job completely. The saw is easy to use and has a smooth operation. Once it's locked onto the casing, the machine does not tear or bounce the equipment around. It does all the work itself. This saw saved a lot of time on the job." Jones' biggest regret is that he didn't learn about the saw earlier in the job.
FeeCorp did run into another challenge on the job when encountering casings in concrete. Underneath the concrete was a lot of thick rebar. The FeeCorp crew did have to use a jackhammer and core saw to cut through the existing rebar.
Once the old casings, rebar and concrete were removed, FeeCorp worked with a local ready mix company to pour the new concrete and bring the casings up to grade, Jones says. Then FeeCorp moved on down the road to the next one.
Do you have a project you would like Concrete Contractor to consider for "On the Job"? E-mail your idea to Kim Johnston at [email protected].