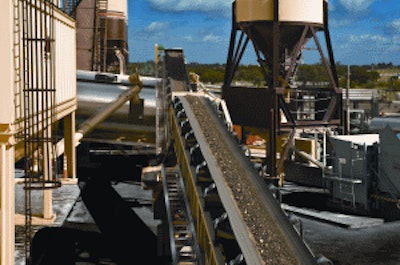
When John Miller - the owner and president of Big Creek Construction in Lorena, TX - started dreaming up designs for his company's new production and operation headquarters, he had two specific goals in mind: 1) He wanted the entire operation to be energy efficient and cost effective; 2) He wanted the facility to be aesthetically pleasing.
A few years later, Miller believes he has achieved exactly what he set out to do. "A lot of people have come down here and looked at our new place because it is so innovative," says Miller. "This is something that I have been wanting to do for years - and I finally did it. I built a place that is pleasing to the eye, and it's very work-efficient, too."
Efficiency by design
The innovative new facility for Big Creek Construction started with a 185-acre tract of undeveloped farmland southwest of Waco. The property's size and close proximity to Interstate 35 made it ideally suited to become the home for all of Big Creek Construction's operations, which include about 350 employees, an HMA production facility, and four paving crews.
"We decided to put our whole complex in there, from the asphalt plant to our maintenance shops to our offices, plus facilities for our pre-cast concrete operation," says Miller.
The front 35 acres were transformed into a park for exotic wildlife. That's where Miller keeps 15 axis deer, seven blackbuck antelope, six red deer, and the two water buffalo that are named George and Gracie after George Burns and Gracie Allen.
In an effort to make the property aesthetically pleasing, Big Creek Construction also planted a number of oak trees on the property. Miller's concern for making the property pleasing to the eye was not only for the benefit of visitors and staff members.
It was also an effort to be a good neighbor. Out of consideration for the residential properties that are situated behind the HMA production facility, Big Creek Construction built a 20-foot berm on the hilltop to block sound and to keep the plant and its storage silos out of the neighbors' sight lines.
"The berm cuts off most of the noise for our neighbors, which they really appreciate when we are working at night," Miller says. "We try to be good neighbors."
When drawing plans for the plant and all of its associated buildings and structures, Miller took a close look at the lay of the land and used its geologic features to his advantage.
About 15 feet of dirt and rock were cut out of an already low-lying area to provide the foundation for the HMA plant. The cold feed bins were positioned with their openings even with the top of that cut. The stockpiles were then placed on the elevated area just beyond the cold-feed bins.
"With this arrangement, all of the materials stockpiles are close to the cold-feed bins. In addition, the aggregates and RAP sit on solid rock that has a 6% to 10% grade. So the stockpiles drain really well to keep the moisture down in our materials," says Miller.
That layout cuts down on drying time required for aggregates and RAP, and it also saves on fuel and wear-and-tear on the front-end loaders that put material into the cold-feed bins.
"The loaders that handle both the virgin material and the RAP do not need to go up a ramp to get to the cold-feed bins. Instead, they come downhill loaded with material to the cold-feed bins and then go back uphill empty to the stockpiles," explains Miller. "It reduces equipment maintenance and saves a little bit of fuel, too."
Other built-in features in the HMA production facility's layout were designed with personnel in mind. The control house, for example, sits 14 feet above the ground, providing a clear view of the entire facility for the operator.
The plant's laboratory, situated near the truck load-out area, is also elevated to allow lab personnel to walk out and easily collect quality control/quality assurance samples from the top of the departing trucks.
Big Creek Construction's management also found a way to save time for the truck operators, getting them in and out of the facility quickly and easily. The three 300-ton storage silos - one used for commercial sales and the other two for Big Creek Construction's own paving operations - are each equipped with 8-ton weigh batchers in lieu of truck scales.
Truck drivers also get the benefit of a remote printer that produces a load-out ticket at each load-out area.
"The tickets are printed right there," says Miller. "And the drivers like that. It's a feature that keeps them moving. They don't have to get out of their truck except to grab the ticket and then they're back in the truck and on their way."
The company's management is always keeping an eye out for new and innovative ways to keep things moving faster. The new Big Creek Construction facility included an automated spray-down system for the release agent used to clean the backs of the trucks. That worked - but asphalt manager Shannon Parsons says they noticed one little item that was slowing things down.
"We sat there and watched the line of trucks backing up and we asked ourselves, why? Well, it was taking them too long to wash out after going through the spraydown system for the release agent," says Parsons. "Now, we believe that if you are sitting there and watching the same problem all day long, you really should do something about it. We did. We decided to add a water cannon so the truck drivers can blast their trucks out in one-third the time. Little things like that make a big difference in the long run."
Saving money by going green
Creating a more efficient workflow was only the beginning of Miller's innovative vision for the new facility. At the heart of his plan was a 300-tph Astec Double Barrel dryer/mixer - a production facility that is capable of incorporating high percentages of RAP in the mixes.
A little over a year after putting that facility online, Miller upgraded the plant to incorporate the Double Barrel Green System that allows the production of warm-mix asphalt (WMA).
Big Creek Construction is currently operating the most advanced and environmentally friendly technology available in the road-construction industry. And it is technology that is quickly becoming better understood and more desirable by both commercial customers and DOTs.
"We use the WMA as often as the state DOT will allow us, and we use it on private work, as well," says Parsons. "State DOT engineers are very excited about it."
Big Creek Construction takes full advantage of the Double Barrel dryer/mixer's ability to handle large amounts of RAP in everyday mixes. The company keeps as much as 50,000 tons of RAP on hand and prepares it for use in new mixes by fractionating the material into two different sizes: 1.5 inches and 0.5 inches.
The process of fractionating the RAP lets Big Creek Construction achieve better precision with their mixes, which in turn will lead to higher percentages of RAP.
"We feed the maximum amount of RAP that the state DOT will allow," says Miller. "On our commercial work, we figure we can go as high as 30% RAP."
Staying ahead of oil prices
One of the most innovative ideas that Miller implemented with the new Big Creek Construction facility may not be immediately visible to the naked eye.
It's there - but you need to know what you're looking for before you can see it. There are liquid asphalt cement storage tanks located in a concrete bunker that is backfilled with 15 feet of dirt. That setup allows Big Creek to store up to 17,350 tons of liquid AC.
"With the asphalt prices escalating like they are, we felt that we needed to hedge the market a little bit," says Miller. "So we put in a big storage facility for liquid AC. In Texas, we don't have an indexing system, so you're on your own when you bid an asphalt paving job.
"Our liquid AC storage facility has helped us a lot in keeping jobs going and not lose money," he says.
The storage facility consists of two 5,000-ton tanks; two 1,800-ton tanks; and one 3,750-ton tank.
"We only use one cell at a time so we don't have to heat the whole mass of asphalt at one time," Miller explains. "Each storage cell can be isolated from the others, allowing one 3 million BTU Heatec heater to heat just one or two at a time. As we draw down one tank, we'll start heating the next one so our operations are uninterrupted."
ƒÞ