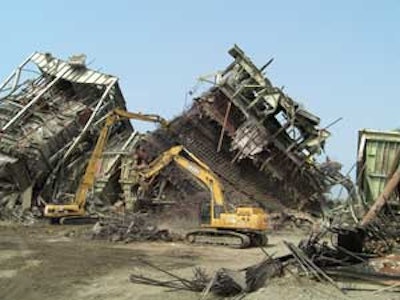
Completed in 1968 at a cost of $274 million, the 2,400-megawatt Lakeview Thermal Generating Station was the province of Ontario's largest thermal-electric plant. For 40+ years, its four 480-ft.-high concrete stacks (known as "The Four Sisters") served as a distinctive landmark west of Toronto on the Lake Ontario shoreline.
As part of a government plan to phase out all of Ontario Power Generation's six coal-fired generating stations by the end of 2007, the stacks were demolished in a controlled drop and were on the ground in less than 30 seconds, while the plant itself was imploded and leveled in under a minute. Then the real work began.
Slicing and sorting through the debris
The complete demolition project, including remediation of the 130-acre lake-front site, is expected to take up to two years. It's a huge undertaking calling for an expert team of heavy equipment professionals to finish the job safely, on time and economically.
The team on the site comes from Murray Demolition (a division of Quantum Murray LP), headquartered in Toronto, Ontario. Murray Demolition specializes in industrial and commercial demolition projects, and is one of Canada's Big Three demolition contractors capable of taking on jobs of this magnitude.
The steel structure of the power generating station housed a complex of conveyors, coal hoppers, boilers, heat exchangers and turbines. The columns of the building structures were strategically severed to effectively lay the building on an incline. This was intended to get the structure as close to the ground as practical, yet still allow crews to work on specific areas.
The tools chosen to cut through the debris include a fleet of excavator-mounted shears. Primary shearing is being used to dismantle the buildings, then the materials are segregated into #1 heavy melt, #1 prime scrap, shredding, various non-ferrous scrap, concrete and brick. Once sorted, secondary shearing takes place when needed to further break down the material.
Twelve excavators — seven equipped with shears and five equipped with grapples — work in tandem to load the revolving fleet of 30 to 35 scow trailers. Anything that can't be sheared is hand torched. Between the excavators and torch crews, Murray is regularly hauling out between 700 to 900 tons of the various sorted materials every day.
Unique shears for specialized work
Two specialized shears have been designated to take on the tasks of heavy and high-reach shearing.
The first is a Stanley LaBounty MSD 7500R, which is mounted on a John Deere 850D excavator. "We purchased the unit from Pineridge Equipment Limited, a long-time Stanley LaBounty dealer, specifically for shearing the large structural beams on this job," says Jerry Dowall, Murray's site project manager.
Weighing in at 29,500 lbs. with a 43-in. jaw opening and a 45-in. jaw depth, the MSD 7500R is one of the largest shears in the Stanley LaBounty lineup. It is best suited for matching to a 160,000-lb. excavator. Paul Lorenco, an experienced demo pro, operates the large excavator/shear combination. "This machine is used to rip, pull and tear the heavy primary structure down. Then it shears and sizes beams up to the 10- to 12-ton range for stockpiling and hauling out," he notes.
The 850D excavator and MSD 7500R shear have proven to be a good combination. "It gives me perfect control, and has excellent stability with no additional counterweight. The visibility is outstanding, right to the front end of the shear," says Lorenco. "The [shear] has the opening and the power to back up handling the really big stuff, pulling and tugging at the structure. That's why we brought it in. It really does the job, day in and day out. It's the largest Stanley LaBounty shear in our fleet and, with 800 hours on it, I am totally impressed with its shear power."
The second specialized shear in use is an MSD 1500R paired with a Caterpillar 330 high-reach excavator. "We got this machine and it has really worked well for us on this job. It has a reach of 70 ft.," says Dino Toste, a long-time Murray demolition professional. "I do the primary high pick and shear that the other equipment can't reach. There's a lot of work above the normal 40- to 45-ft. reach of the other equipment and it keeps me busy. We all work as a team to get the job done."
Five MSD 3500R shears serve as the secondary processing lineup. Mounted on John Deere 450D excavators, they work mostly at ground level to cut hoppers, ducts, sheets, beams, flooring and heat exchanger tubing.
Support proves crucial
According to Luigi Teti, Murray's equipment specialist, the shears have held up well under tough operation at the site. Murray has the Pineridge service technicians in one day a week to service all of the shears, and sometimes more depending upon the work being done.
"Some may need weld buildup or a blade turn or swap and others may not," Teti notes. "However, we have found one day a week seems to be a good balance to keep the seven units here at the jobsite in top condition."
Teti has also worked closely with the factory on any necessary adjustments. For example, the MSD 7500R was the first of its kind in Canada on a demolition job of this type. Teti had ideas for some minor improvements and called Stanley LaBounty. The company sent two of its chief engineers to the Lakeview Project site to meet with the Murray Demolition experts. They collectively came up with product improvements that will benefit all demolition operators.